Canned Motor Pumps Reliably Redirect Unwanted By-Products out of the Gas Flow
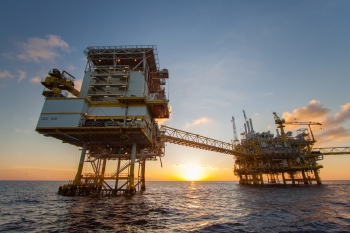
The delivery of the 16 canned motor pumps is planned for February 2020; the expanded gas field is expected to start up in 2022. (Image source: shutterstock)
In addition to powerful pump technology, it is crucial to remove the medium reliably and safely, since the substances separated with this method often form a toxic, highly corrosive mixture. The Nikkiso non-seal pumps being used function without dynamic seals and also feature twin safety shells consisting of an inner stator lining and external pressure-resistant stator housing. As a result, leakage and the associated risks for the environment and employees can be effectively prevented. An integrated E-Monitor also ensures increased process safety at the customer s onshore installation by monitoring the bearing conditions of the hermetically tight pumps. The project is expected to be completed in 2020, including detailed planning and procurement plus construction and installation work.
In the course of raw material processing, unwanted by-products are continuously removed from the oil or gas flow. "The unusable mixture of substances that is derived from the clean gas flow mostly consists of hydrogen sulfide, carbon dioxide, and amines," explained Riccardo Marcotti, Senior Product Manager at Lewa Nikkiso Italy. "Hydrogen sulfide is particularly worth mentioning here, since it is a highly toxic chemical compound even in very low percentage and, dissolved in water, it is also highly corrosive to piping and equipment by sulfide stress cracking." This is why it is only possible to remove unwanted by-products with conventional pump technology to a limited extent – the risk of leakage and thus the release of hydrogen sulfide in the atmosphere is too high.
Second protecting shell and elimination of dynamic seals
In light of these challenges, the global oil and gas company contacted Lewa Nikkiso Italy, a subsidiary of the German pump manufacturer, in February 2019 and commissioned the production and delivery of a total of 16 Nikkiso non-seal canned motor pumps. The pumps are necessary to guarantee that the toxic by-products are transported without complications, while avoiding negative effects on the environment and personnel at the expansion of the onshore gas field. "As you can imagine, the user s requirements for pump quality and project organization were very detailed," said Marcotti. "Above all, the customer placed priority on the aspects of pump reliability and safety. Our Nikkiso canned motor pumps were able to meet their standards optimally."
In total, the delivery to the major customer from Saudi Arabia includes six type HN23F-D2 canned motor pumps, two type HN24E-D3 models, four pumps in the HN23F-D3 basic design – as well as additional four warehouse spare pumps – each model sized for rated performance conditions. All of the variants being used feature a motor that is integrated right into the respective canned motor pump and is protected against leakage by a seal-welded, corrosion-resistant lining. And the entire motor exterior is encapsulated in a second leak-proof protective shell. As a result, we can eliminate the possibility the mixture will escape and contaminate the surrounding area and the environment. "Omitting dynamic seals has also allowed us to significantly boost operating safety during the work process," added Marcotti.
E-Monitor determines current bearing condition
Absolute process reliability also includes ensuring constant motor cooling to prevent immediate and long-term damage to the pump. Therefore, in the canned motor pumps being used, the medium being conveyed circulates in the area between the rotor and stator lining, affecting the motor temperature while lubricating the slide bushings at the same time. The integrated thermostats attached at the overheating points of the winding monitor the temperature and switch the motor off in case of overheating. This prevents subsequent damage.
In addition to monitoring the temperature, it is possible to check the bearing condition during pump operation. To do this, the sensors integrated into the stator transmit the relevant measurement data to a modern E-Monitor – for example, if the rotor leaves the safe operating position due to bearing wear. The sensors register this type of status change and report it to the monitoring unit. "A green LED lights up on the display to indicate a good bearing condition to the personnel, for example," explained Marcotti. "A yellow light, on the other hand, indicates that the pump should be checked during the next system downtime. If a red LED lights up, the pump must be shut down immediately." The device makes it possible for customers to perform preventive maintenance work based on bearing wear and check that the pump s direction of rotation is correct. As a result, it is not necessary to measure phase rotation during commissioning.
Everything from a single source
In this major project in Saudi Arabia, Lewa Nikkiso Italy has been entrusted with the full spectrum of project implementation. This means the subsidiary of the Leonberg Group has been commissioned with detailed planning and procurement, as well as carrying out the supervision assistance for construction and installation work. "Thanks to our extensive experience with other EPC projects, we will be able to meet all the existing requirements without a problem," said Marcotti. "In addition to the necessary levels of safety and reliability, this applies to the specifications for compactness and maintenance, in particular." The modular structure of the pumps to be delivered is helpful here, since they consist of just a few components. All that is required is straightforward assembly and maintenance – without any spacer discs or clearance settings. And no additional motor or pump bearing lubrication is needed, since the medium being transported coats the sliding parts on its own. "This makes the pumps extremely easy to maintain and minimizes expensive downtime at the same time," Marcotti explained. Delivery of the 16 canned motor pumps is planned for February 2020; he expanded onshore gas field is expected to start up in 2022.
Source: LEWA GmbH