Breathing New Life Into Pumps of Any Age From Any Brand with OEM Knowledge
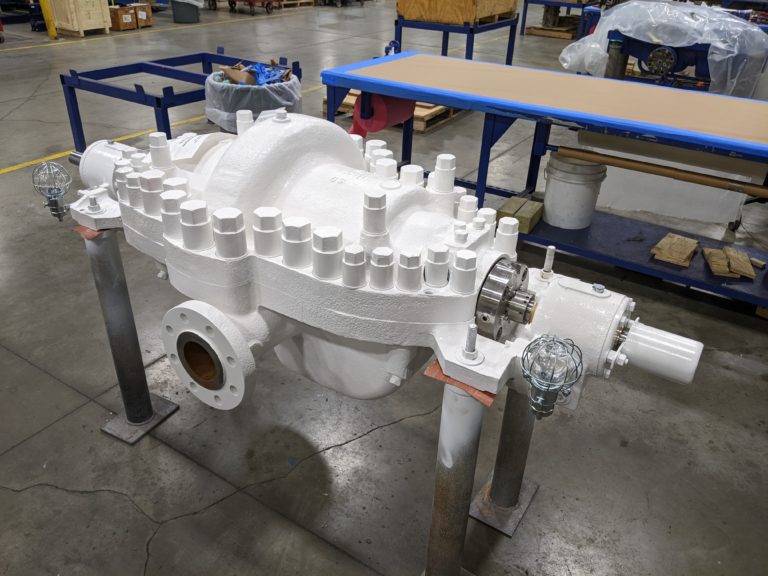
Once all parts were received, they underwent a preassembly process to allow the technicians to verify the fit and design of the new component, before the pump was prepared for shipment back to the customer. (Image source: Sulzer Ltd.)
Of course, the worst-case scenario of a catastrophic pump failure can be amplified if the original equipment manufacturer (OEM) is no longer in business; operators can feel in a difficult position. Sourcing a new pump can, depending on the application, have a long lead-time and high investment requirement. In addition, the new pump will most often have a different design, which will necessitate significant alterations to the surrounding infrastructure.
An effective solution
Sulzer’s alternative is its OEM-X Line service, which offers pump engineering expertise that has both the design capabilities and the manufacturing technology to refurbish an original pump from any brand. This approach has several benefits, not least the opportunity to incorporate modern materials into the original pump, which can be reinstalled quickly and returned to normal operation. This is usually the most cost-effective solution, keeping downtime to a minimum and can, in some cases, even lead to efficiency gains.
As a pump OEM, Sulzer has developed cutting-edge design and manufacturing techniques that can also be applied to the maintenance and repair of equipment from any manufacturer, including those that are no longer in the market. This service is exemplified by a recent project that went through the company’s service center in Pasadena, TX.
The pump in question was a between-bearing, six-stage type working with propylene carbonate. The failure happened when the rotating assembly spun contrary to its designed direction for a considerable period of time, leaving behind damage to all the stationary and rotating elements contained in the pump.
Design complexity is no object
The design of the pump was a mix of an axially split and double casing barrel, containing both an outer shell and diffuser stages; the outer case didn't suffer any damage from the failure. The cost of a newly designed current API edition pump was prohibitive due to the requirements to change the foundations and existing piping configurations.
Initial investigations found many diffuser guiding vanes bent or broken, as well as diffuser walls that had cracks and wear damage due to the contact with the impellers to the point where they could not be repaired. There was substantial damage to all internal parts as well as rubbing marks present on all elements. Most of the wear rings had become stuck between the stationary and rotating elements or were worn
out of shape altogether. Some stationary rings were absent from their locations and several impeller walls were cracked or broken and couldn't be used again.
The challenge for Sulzer was to recreate all of the damaged internal components, maintain the hydraulic design from the third-party OEM and upgrade various aspects with the latest advances in technology.
Reverse engineering
The first step was for the design engineering team to reverse engineer the complex items, such as impellers, and diffuser passageways, using 3D laser scanning. This can render a component's geometry with an accuracy of 0.0005" (0.013 mm), allowing the design engineer to capture an accurate, digital mesh of the part.
The mesh enables complex measurements and sketch geometry details to be obtained. A solid 3D CAD model was then translated into a 2D sketch to perform the quality audit (QA) and control processes on the scanned parts. Once the QA process was complete, the parts manufacturing department was tasked with producing the components by translating the model into a CAD-appropriate file to create molds and patterns for casting. These were machined according to the final specifications and dimensions requested by the repair engineer and returned to the service center.
Working in parallel with the parts manufacturing department, the pump service center in Pasadena redesigned and created the remaining components needed for the repair. These were less complex and consisted mainly of sleeves, wear parts, shafts, and rings. The parts were redesigned using 3D CAD software and manufactured according to specifications derived from Sulzer’s expertise as a pump OEM.
Material upgrades
In addition, the customer requested an upgrade to the pump's wear elements to a high-temperature, high-friction-resistant polyimide thermoplastic material. This technology has been used in aerospace applications for many decades and has been adapted to centrifugal pumps to achieve better results while preserving the component's lifespan.
These high-performing polyimide thermoplastics allow the pump to run at tighter clearances than metallic wear elements, resulting in less internal recirculation and increased pump performance. The modifications were discussed with the engineering and repair engineering departments for approval to ensure all parties and the customer were agreed.
Once all parts were received, they underwent a preassembly process to allow the technicians to verify the fit and design of the new components. Finally, the pump was assembled and hydraulically pressurized to 1.5 times maximum allowable working pressure (MAWP) to ensure no leak paths were present and overlooked during the repair, before the pump was prepared for shipment back to the customer.
The result of all this effort was the restoration of a complex, third-party pump to its full capabilities with the same if not better performance than before, using the latest technology and materials. The other positive outcome for the customer was the capability of Sulzer’s OEM-X Line service to fully support the pump in the future, thanks to all the completed engineering work. Going forward, the equipment's service life will continue, even though its original manufacturer is no longer present in the market.
Source: Sulzer Ltd.