Atlas Copco Compressor System Upgrade Earns Major Savings for Sparta
Following a major move from Rossendale to its 42,000 sq ft new premises in Burnley, subcontract engineering company Sparta Ltd anticipate substantial energy savings and carbon reduction from their Atlas Copco compressor system upgrade.
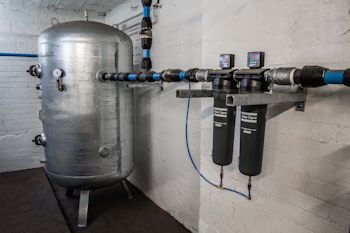
Atlas Copco / Sparta Ltd.
Sparta Ltd was founded in 1985 and is a specialist engineering company committed to achieving outstanding results in the field of investment castings, water jet cutting, CNC machining, laser cutting and powder coating. Output also includes the fabrication of products for the marine and architectural services markets. The company’s ability to perform is backed up by a number of recognised accreditations: - ISO9001/2000, AS9100 and NADCAP - while earning approvals from the aerospace, defence, RNLI, telecommunications, automotive, shipbuilding, and shop fitting sectors of industry.
Sparta attributes much of its well-earned reputation as one of the UK’s leading subcontract engineering companies to its policy of constantly reviewing and improving all aspects of its resources and manufacturing techniques. So, prior to the recent premises move, a comprehensive analysis of plant usage was carried out, including that of its reliable but ageing compressor installation.
As a starting point, Atlas Copco sales engineer John Green carried out an iiTrak data logging survey of the existing compressor system to establish just how well it was performing. This procedure was followed up with a full report which included the recommendation to upgrade Sparta’s air supply equipment with a more energy-efficient solution, one that was calculated to save approximately £14,000 per annum for the site’s electricity consumption and an annual carbon reduction of over 100 tons.
Three new full-feature GA30VSD+FF oil-injected rotary screw compressors were installed together with a central controller and ancillary equipment. The upgrade solution took on board the fact that the plant could run a back shift with reduced staff which would use just one of three machines; the two others would be allocated for day shift operation with the third compressor then made available for service and continuity duties.
The compressors and ancillaries are connected to the workplace processes via a completely new AIRnet ring main. AIRnet is Atlas Copco’s modular air piping system, made from robust, lightweight, powder-coated aluminium tube and designed for easy, low-cost installation with a large selection of engineered polymer fittings. No special tools are required in its assembly and the corrosion-free, low friction, seamless connections minimise pressure drop thus effectively contributing to compressed air energy efficiency, as well as reducing the cost of ownership of the piping system.
As Sparta’s managing director Stephen Davenport observes: “The use of the Atlas Copco pipework throughout the factory has given us a leak-free environment which is better for all concerned and the flexibility of the system with its 10-year guarantee against any damages resulting from material defects, is future proofing what we have done.”
Commenting on the compressor system purchase decision, Stephen Davenport said: “Our decision was made based upon the reliable service we had enjoyed from our original two Atlas Copco GA75 units. The potential annual cost savings of running this new system enabled us to purchase the machines on a finance lease basis. The monthly costs for power consumption being that much lower has meant that the overall costs have shown a saving right from month one.”