Alfa Laval Introduces New Sensor and Control Unit for Diaphragm Valves
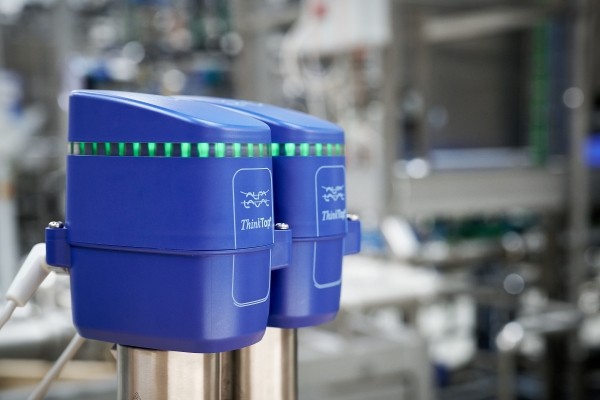
Introducing the highly efficient, space-saving Alfa Laval ThinkTop V55 sensing and control unit for diaphragm valves (Image source: ALFA LAVAL Corporate AB)
It is built on proven ThinkTop V series technology, which is trusted among dairy, food, and beverage manufacturers worldwide for its simplified setup, unparalleled reliability, advanced automation, live replacement capabilities, and real-time communication.
Maximum security
The ThinkTop V55 offers unmatched peace of mind to users. Its durable, maintenance-free design ensures reliable performance even in the most demanding environments. Tamperproof construction and built-in self-diagnostics maximize uptime, making it a dependable choice for critical operations.
“With its advanced features and compact design, the ThinkTop V55 sets a new standard for diaphragm valve monitoring and control, optimizing performance and efficiency,” says Paw Kramer, Portfolio Manager, Valves and Automation, Alfa Laval.
Simplified setup and live replacement
The ThinkTop V55 supports fast, reliable installation and quick commissioning. Onsite auto setup takes less than a minute, while live setup – enabling quick remote valve configuration – requires only a minute or two. Exchanging or hot-swapping control units can take place without disrupting production, ensuring operational and product safety.
Compact and flexible
The slim profile of the ThinkTop V55 optimizes space utilization, making integration into new or existing installations effortless. It is easy to mount in any position on the valve actuator to ensure ideal connection. Moreover, the ThinkTop provides 360° LED visual status indication, making the valve position clearly visible from the factory floor. It delivers highly reliable performance in demanding environments thanks to its self-diagnostic features that boost uptime and productivity.
Next-generation control for Industry 4.0
The ThinkTop V55 provides real-time diaphragm valve monitoring through digital, ASI 3.0, or IO-Link interfaces, ensuring accurate valve position readings. Its point-to-point IO-Link communication protocol integrates sensors and actuators into any automation system, regardless of fieldbus. This integration makes it easier to capture, store, analyze, and act upon meaningful real-time data thereby supporting Industry 4.0 initiatives, streamlining configurability and process control.
Source: ALFA LAVAL Corporate AB