25 Mistakes that will Cost Money – Part 1
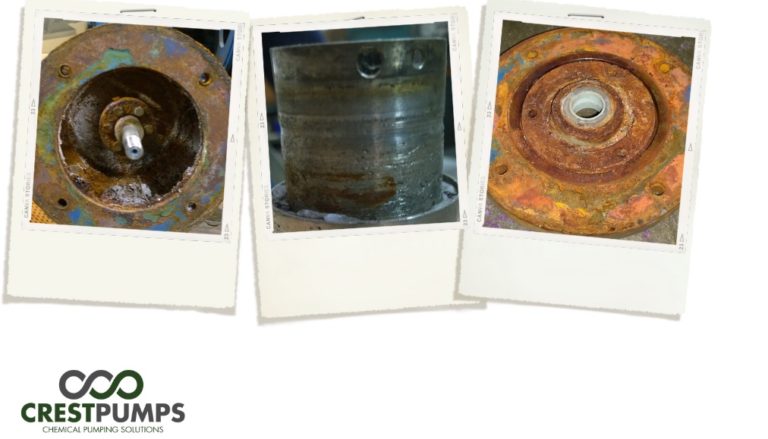
25 mistakes that will cost you money! (Image source: Crest Pumps Ltd.)
Relying on reactive maintenance rather than predictive measure
Too many times pump maintenance is overlooked or forgotten about within the maintenance procedures, leaning to only reactive maintenance if the pump fails, leading to longer process down time, pump instability and expensive repairs. Instead, schedule biannually or quarterly pump maintenance including inlet cleaning, corrosion inspection, vibration monitoring and heat maintenance at the very least to ensure that cavitation or bearing wear is avoided.
Improper bearing fitting
Every time a bearing is replaced, or the shaft is cleaned, just a tiny fraction of the material on the surface is removed. Over time, a little adds up to a lot and can really affect the bearing clearance on the shaft. When this happens, expect the bearings to spin within the housing, or on the shaft.
Wrong mechanical seal or seal material
Lack of knowledge accounts for the majority of mechanical seal failures. Incorrect mechanical seal installation can lead to seal face damage, heat escalation and ultimately pump failure. Make sure you discuss the type of chemical your are processing with the pump manufacturer and type of mechanical seal you need.
Hard-starting the pump
The Pump should be eased into pumping with a soft start. With a hard start, the pump tries to pump liquid as soon as it powers on. The pressure inside the pump caused the shaft to deflect towards the low pressure side causing the shaft to contact the casing. The misalignment will then cause seal failure. Remember to keep the suction valve wide open.
Not detecting vibration
Vibration can be a sign that the pump is seriously failing in its process. Vibration can damage wear rings, bushings, impellers and the bolts connecting the pump and motor. Vibration leads to the shortening of the life of the pump by over three quarters, so it is imperative that if excessive vibration occurs, your engineers take the necessary steps to find the root of the problem.
Mechanical Cause:
- A bent shaft
- Unbalanced rotating components
- Pump misalignment
- Pipe strain
- Loose bolts
Hydraulic Cause:
- Operation not near the best efficiency point of the pump
- Vaporization of the product
- Air in the system
- Turbulence in the system
Other:
- Vibration from other machinery
Not undertaking initial start up procedure
Improper starting up the pump can cause the motor to trip and the shaft to twist causing orbital movement directly related to internal parts contact, seal failure and shortening of the bearing life.
Pumping with a bent shaft
A bent shaft can be a result of either operating off of the best efficiency point or pumping solids in a pump that cannot deal with solids effectively. When operating off of the BEP - too much pressure is applied to the shaft from one angle over the other causing strain. Pumping solids can get caught in the pump, leading to vibration, internal parts contact, bearing damage and ultimately premature pump failure.
Solids trapped in seal housing
When the processed liquid and abrasives get stuck in the steal housing and isn't properly flushed out, expect to see a shortened seal life.
Pump imbalance
Pump imbalance can create issues such as structural problems, reduced bearing life, increased vibration and reduced machine life. Vibration is the second biggest cause of pump failure and the largest cause of vibration is pump imbalance.
Incorrect tools for installation or repair
Using a hammer to install couplings onto shafts or pipe wrenches for anything other than pipes. When it comes to pumps, they are delicate machines that can crack if struck with a hammer.
Plugged vanes
Plugged vanes or balance holes are caused by blockages from solids that have been pulled into the pump that are too large for the pump capacity. Plugged vanes lead to a decrease in performance, efficiency, priming issues, impeller imbalance and high vibration, resulting in seal damage.
Incorrect wear rings
A wear ring separates the high pressure zones of the pump from the low pressure zones. When clearances open up, the pump experiences increased slippage, and the high pressure liquid seeps back into the low pressure areas, causing a loss in efficiency. When clearance are too tight on the other hand, it will cause galling and seizing of the pump.
Entrained vapour in the pump
Entrained vapour can be caused by a number of factors. Vortex in the tank, insufficient water source, steam injection or incorrect NPSH conditions. Entrained vapour causes loss of performance, wear the to the impeller and cutwater, and dry running of the seal due to vapour between the faces.
Stay tuned for the second half of the guide of 25 ways to break a pump - and see the rest of the mistakes to avoid costing money!
Source: Crest Pumps Ltd