Grundfos Launches Largest CR Pump
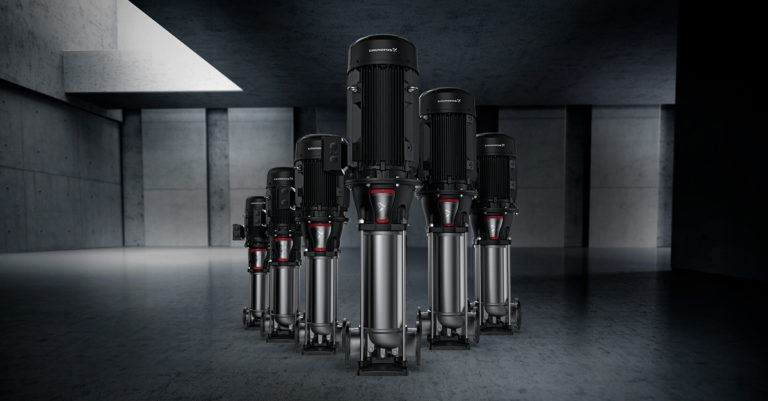
The new CR 255 model achieves maximum water flow at a game changing rate of 320m³/h. (Image source: Grundfos)
As Grundfos’ largest vertical multistage inline pump to date, this latest addition to the CR portfolio will take current energy efficiency and performance standards for vertical multistage inline pumps to the next level.
Grundfos’ range of CR pumps are the world’s first vertical multistage centrifugal inline pumps, and are used predominantly for water supply, water treatment and almost all industrial solutions – including those for high-pressure, hot, dangerous, flammable, and aggressive liquids. Since its inception, over 3.5 million CR pumps now serve industries around the globe.
Industrial operations across different sectors – from semi-conductor manufacturing to food and beverage processing – can be water and energy-intensive. Currently, industrial processes account for 19% of worldwide water consumption. With the need for a constant flow of large quantities of water, Grundfos CR range is an efficient way of handling the production process.
Grundfos’ largest vertical multistage inline pump, the new CR 255 model delivers water pressure of up to 400m and achieves a maximum water flow of up to 320m³/h, the equivalent of supplying water to 9,500 people. For industrial processes such as water booster supply, similar large Grundfos CR pumps have demonstrated improved performance by up to 30% compared to regular pumps .
Key benefits of the Grundfos CR pump range include:
- More energy-efficient. With its optimised hydraulic design - from impeller and guide vanes to inlet, discharge port, sleeve, and diffuser - the new generation of Grundfos CR offers world-class energy efficiency.
- More cost-efficient. With power consumption responsible for 90% of a product’s life cycle cost, greater energy efficiency means greater cost savings. Due to its small footprint, the CR pumps are also much easier and less costly to install than other pump designs.
- More reliable. The new generation of large CR pumps has been made even more robust than its forerunners through use of state-of-the-art technology in simulation-design, materials, testing and production. CR pumps are also equipped with predictive monitoring, tracking pump health 24/7 and effectively alerts users to possible process failures, reducing unnecessary and costly downtime and also eliminating the need for regular servicing.
- More options. The new generation adds even more options to what was already the most modular pump programme in the world. With millions of possible variants in the CR range alone, users can always build a Grundfos CR pump to match their exact specification – whatever the application.
Commenting on this latest milestone and launch, Eric Lai, Grundfos’ Regional Sales Director, Industry – APAC & Country Director for Singapore, said “As industrialisation in the region continues to advance at a rapid pace, it is crucial for industrial solutions to stay ahead of the game in terms of performance, efficiency, and ultimately support any business in achieving global competitiveness.”
Eric Lai added, “This new generation of CR pumps is testament to five decades of continuous innovation and refinement since its initial launch in the 1970s, ensuring that its reliability is unsurpassed and meets the evolving needs of industries. To ensure every single component is perfected, we developed this latest extension with over 10,000 simulations during the design process, followed by rigorous real-world testing before going into production. We believe this new addition will make our CR pump range a strong offering for industries who are looking to optimise their performance by achieving more with less in their operations.”
Source: Grundfos Holding A/S