Canned Motor Pump Technology Has Multiple Advantages
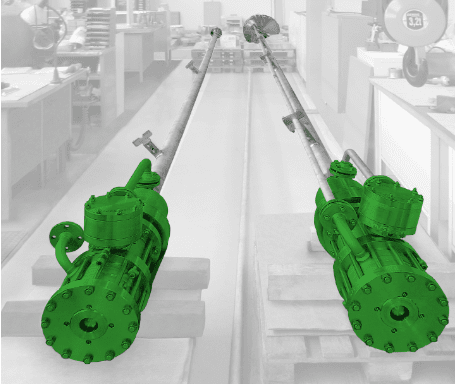
Immersion depth: 8 m; shaft lenght of pump: 1 m; slide bearing: 2 pce. (Image source: HERMETIC-Pumpen GmbH)
Environmental protection regulations and occupational safety provisions regarding the handling of toxic and explosive liquids increasingly call for pump installations which are immersed in tanks. Discharging at the bottom or lateral outlets are often no longer admissible. Since submersible pumps are harder to access, there are very demanding requirements regarding durability, availability, easy servicing and high MTBF (Mean Time Between Failures). In addition, operators want the pump to be monitored as extensively as possible to ensure that any upset conditions are detected early-on and preventive maintenance measures can be taken.
Canned motor pump technology provides significant advantages and often constitutes a low-priced alternative to conventionally sealed pumps and magnetically coupled installations with external drive, since there are no long shafts or complex cooling and lubrication systems of mechanical seals.
In conventionally sealed submersible pumps, i. e. equipped with mechanical seals, and also in magnetically coupled in-tank pumps, the motor is installed at the outside of the vessel. Depending on the immersion depth of the pump, this results in a correspondingly long shaft to connect the pump hydraulics to the drive motor. This kind of shaft is fixed for example using fluid-lubricated slide bearings. As a rule of thumb, these bearings are installed at distances of approx. 1.2 to 1.6 meters. Statistically speaking, however, the probability of failures increases with each bearing. In addition, each bearing must be maintained regularly and causes not only installation expenses but also maintenance costs.
The installation of a submersible canned motor pump provides a state-ofthe- art, cost-efficient and reliable alternative. Thanks to the hermetically sealed design of the drive unit, which consists of the hydraulic and the motor, it can be completely immersed in the tank. Only the discharge pipe and the electrical connection are routed through the tank cover via the manhole plate out of the vessel. This provides the operator with significant advantages:
Short shaft with only two slide bearings. The fluid- lubricated slide bearings of the canned motor hold a short shaft on which the rotating parts of the motor and of the hydraulic are combined. The stator liner separates the pumped medium securely from the dry electrical part of the pump. The slide bearings operate in a contact-less manner and are therefore maintenance-free. Some installations are in operation for many years without any servicing measures. Customer studies show that the MTBF times of this technology are many times longer than those of a conventional installation.
Two or four pole motors can be installed, independent from the immersion depth. The two pole motors provide high power density and a low-cost, compact design. Using four pole motors, extremely low NPSH3 values can be achieved.
Comprehensive monitoring devices can be installed on request. The condition monitoring of in-tank pumps is much more difficult than the condition monitoring of units which are located outside. The HERMETIC canned motor pump provides a monitoring concept which monitors the safe operation of the pump via installed sensors. In addition to operating temperature, liquid level and motor load, the specially developed MAP system can be integrated. It continuously monitors the position of the rotor and is therefore a reliable indicator for unintended operating states and wear.
Absence of shaft seals often results in a more cost-efficient and less complicated installation. Flushing and cooling systems and their monitoring can be omitted.
Cryogenic applications. Canned motor pumps excel in cryogenic applications. The efficiency of electric motors decreases with rising temperatures. The canned motor is cooled and kept at a low temperature by the pumped medium, which makes it particularly efficient. Since no dynamic seals and conventional bearings are used, the hermetic pumps provide enhanced reliability and durability in this application.
Exceptionally smooth operation. The motor of the canned motor pump is immersed in the tank and not installed at the outside. In combination with the hydrodynamic slide bearing, this results in extremely quiet operation with low vibration.
Simple installation. The installation of the submersible HERMETIC pumps is simple and a potential removal is also easy to achieve and does not require a complex disassembly of shaft or coupling. HERMETIC canned motor pumps can be designed as lock pumps. The advantage is that the pumped medium can be pushed back in the tank by inert gas and the pump can be removed easily and without leakage of the pumped medium.
In the past decades, the canned motor has proven its value as a low-maintenance and reliable drive for submersible pumps in the chemical and petrochemical industry. Equipped with state-of-the-art monitoring devices and thanks to its compact design, this technology often provides a simple, cost-effective and very operationally safe alternative to conventional shaft seals or magnetically coupled submersible pump versions.
Source: Hermetic-Pumpen GmbH