Energiesparende Pumpentechnik von Knoll Maschinenbau
Immer mehr Metallbearbeiter entdecken Energiesparpotenziale im Bereich Kühlschmierstoffe (KSS), insbesondere bei ungeregelten Hochdruckpumpen. Knoll Maschinenbau hat einen sogenannten E-Pass entwickelt, mit dem sich in weniger als einer Stunde die Einsparmöglichkeiten bei laufendem Betrieb ermitteln lassen.
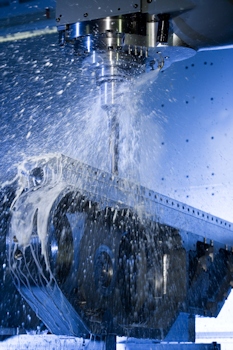
Immer mehr Unternehmen entscheiden sich, das Kühlschmierstoff-Management auf Energiesparmöglichkeiten untersuchen zu lassen. (Foto: Knoll Maschinenbau)
Verschiedene Unternehmen haben inzwischen diese Dienstleistung genutzt und daraufhin beschlossen, die Hochdruckpumpen ihrer Werkzeugmaschinen mit Frequenzregelung nachzurüsten. In nachfolgendem Beispiel liegt die Amortisationszeit unter zwei Jahren.
Umweltschutz spielt für viele Unternehmen eine wichtige Rolle, sei es hinsichtlich umweltfreundlicher Endprodukte, sei es innerhalb der eigenen Fertigung. Bei einem großen deutschen Automobilzulieferer zum Beispiel arbeiten die Produktionsverantwortlichen daran, den ökologischen Fußabdruck möglichst klein zu halten. So werden alle Prozesse ständig auf ihre Wirtschaftlichkeit, Energie- und Ressourceneffizienz sowie Umweltverträglichkeit überprüft und optimiert.
So wurde in der Zerspanung von Aludruckgussteilen bei den Pumpen zur KSS-Hochdruckversorgung ein wesentliches energetisches Einsparpotenzial erkannt. Da diese bisher mit einem Vario-Ventil mit unterschiedlichen Druckstufen ausgestattet waren, stellte sich die Frage, ob sich die Umrüstung auf frequenzgesteuerte Pumpen lohnen würde.
Schnelle Analyse mit Praxiswerten
Als Knoll Maschinenbau, Anbieter von Pumpen, Filtern und kompletten KSS-Systemen, Untersuchungen bezüglich des Energieverbrauchs vorschlug, stimmten die Bereichsverantwortlichen gerne zu. Zumal die Verbrauchsmessung keinen längeren Maschinenstillstand bedeutet und anschließend eindeutige Zahlen auf dem Tisch liegen.
Jochen Blersch, Fachmann für energieeffiziente Lösungen bei Knoll, erklärt den Hintergrund des Einsparpotenzials: „Die eingesetzten Pumpen mit Vario-Ventil sorgen zwar für unterschiedliche Druckstufen, erzeugen aber dennoch den vollen Volumenstrom, so dass der nicht benötigte Kühlschmierstoff abströmen muss. Damit ist ein vielfältiger Energieverlust verbunden, den ein Frequenzumrichter vermeiden hilft. Denn er sorgt für eine bedarfsorientierte Druckregelung über die Drehzahlanpassung der Pumpe.“
Für die Effizienzanalyse hat der KSS-Spezialist ein besonderes Messsystem entwickelt, den Knoll E-Pass. Damit lässt sich zum einen die Leistungsaufnahme einer Hochdruckpumpe im Prozess ermitteln, und zum anderen feststellen, welche Leistung effektiv für den Bearbeitungsprozess gebraucht wird. Beim Automobilzulieferer vor Ort überprüfte Jochen Blersch zwei Bearbeitungszentren, die typische Serienwerkstücke bearbeiten. Nur für etwa fünf Minuten mussten die Maschinen stillgesetzt werden, um jeweils die entsprechende Messtechnik zu installieren. Sie misst dann während eines kompletten Bearbeitungszyklus den tatsächlichen KSS-Durchfluss zur Maschine und den jeweiligen Druck. Zusätzlich werden in den Rechner noch erforderliche Daten, wie die Betriebsstunden, die Strom- sowie die Investitionskosten für die Nachrüstung eingegeben.
Nach dem Messvorgang startet die Berechnung. Aus der Differenz zwischen Festdrehzahl und der tatsächlich benötigten Drehzahl mit Frequenzumrichter ergibt sich der größte Anteil der Energieeinsparung. Durch den frequenzgeregelten Antrieb der Pumpe erfolgt außerdem ein geringerer Wärmeeintrag in den Kühlschmierstoff und in die Umgebungsluft. Zusätzlich wird die Pumpe durch den Teillastbetrieb geschont, wodurch sich ihre Standzeit erhöht. All diese Faktoren werden in der E-Pass-Auswertung berücksichtigt.
Geringer Aufwand – eindeutiges Ergebnis
Schon wenige Minuten nach dem Messvorgang liegt ein Ausdruck vor, der exakte Zahlen zur möglichen Energieeinsparung mit einer nachgerüsteten Frequenzregelung und der Amortisationszeit liefert. Jochen Blersch weist noch auf einen Zusatznutzen des Messvorgangs hin: „Über die erfassten Daten lässt sich auch der Verschleißzustand der Hochdruckpumpe bewerten, die gegebenenfalls beim Nachrüsten des Frequenzreglers ausgetauscht werden kann.“
Die ermittelten Werte waren – wie erwartet – überzeugend. Denn in der Zerspanung von Aludruckgussteilen lohnt sich die Umrüstung häufig. Grund dafür sind die vielerlei Werkzeuge, die zum Fräsen, Bohren und Gewinden benötigt werden und die auf Hochdruckinnenkühlung angewiesen sind. Der benötigte Druck und Volumenstrom wechselt jedoch in Abhängigkeit vom Werkzeug und Bearbeitung, während sich die Auslegung der Pumpe immer an dem Werkzeug orientiert, das die höchsten Werte fordert. Kleinere Werkzeuge, Bohrer zum Beispiel, kommen mit deutlich geringerer KSS-Pumpenleistung aus, können also mit niedrigerer Drehzahl optimal versorgt werden. Das spart bei einer frequenzgeregelten Pumpe Energie, denn es gilt die Faustregel: Halbe Drehzahl entspricht halbem Leistungsbedarf. Bei einem fest eingestellten Druckbegrenzungsventil geht diese Energie in Wärme über und verloren.
Auch bei der Anwendung des Automobilzulieferers wird das komplette Kennlinienfeld der Pumpe benötigt, mal ein hoher und dann wieder geringer Volumenstrom bis hin zu Pausenzeiten, in denen die Pumpe bis auf 0 Hz heruntergefahren werden kann. Die mit E-Pass ermittelten Energieeinsparpotentiale lagen bei 61 Prozent. Ein Ergebnis, das den Umbau und die entstehenden Kosten bei den Verantwortlichen rechtfertigte.
Sicherheit durch eine Referenzmaschine
Um die errechneten Werte zu verifizieren, ließen diese zunächst eine Maschine als Referenzanlage umbauen. Der Lieferumfang betraf nicht die komplette KSS-Anlage, sondern nur die Frequenzregelung. Knoll bietet hierfür die KTS-Schraubenspindelpumpe an, eine selbstansaugende Verdrängerpumpe, die sich durch geringe Pulsation, hohen Wirkungsgrad und lange Lebensdauer auszeichnet. Die dazu gehörende Frequenzregelung wird bei Knoll PQ-Tronic genannt, da sie für variablen Druck (P) und Durchfluss (Q) bei optimaler Drehzahleinstellung sorgt.
Knoll sieht sich keineswegs als reiner Komponentenlieferant, sondern vielmehr als Partner auf Prozessebene. Jochen Blersch erklärt: „Wir haben den Anspruch, ohne einen Eingriff an der Werkzeugmaschine mit der vorhandenen Technik und neuem Frequenzumrichter die gleichen Reaktionszeiten zu realisieren wie zuvor – auch wenn die Prozessansprüche sehr hoch sind. Bei erwähntem Automobilzulieferer haben wir die komplette Anbindung an eine bestehende Werkzeugmaschine ohne Knoll KSS-Anlage vorgenommen. Zudem legen wir großen Wert auf eine schlüssige Dokumentation nach CE-Norm, wie Zeichnungen, Elektroplan, Stückliste und Sicherheitsbetrachtung.“
Amortisationszeit unter zwei Jahren
Die Produktionsverantwortlichen begrüßten es, von Knoll alles aus einer Hand zu bekommen, und sie freuten sich über das Ergebnis: Die Referenzanlage bestätigte die theoretisch ermittelten Werte. Damit war der Weg frei, weitere Maschinen zu optimieren. Knoll baute zunächst eine Fertigungslinie mit acht Bearbeitungszentren um, bei denen sich auch wieder die prognostizierten Zahlen einstellten. In einem zweiten Schritt wurden weitere zwölf Maschinen umgebaut.
Inzwischen bekam Knoll das erfreuliche Feedback des Kunden, dass die Maßnahmen auch im Gesamtumfang sehr erfolgreich waren: Vor dem Umbau benötigte eine Maschine im Durchschnitt etwa 3 kW/h. Danach lag der Verbrauch nur mehr bei 1 kW/h. Das heißt, dass sich die Umrüstung insgesamt bei normalem 3-Schicht-Betrieb ohne Produktionsstillstand in weniger als zwei Jahren rechnet.
Jochen Blersch weist auf einen weiteren Vorteil hin, der noch nicht berechnet wurde, sich aber im Laufe des Betriebs nutzen lässt: „Wenn ich eine Pumpe mit Frequenzumrichter betreibe, kann ich damit auch den Prozess überwachen. Ich erkenne zum Beispiel frühzeitig, wenn die Pumpe verschleißt. Denn der Frequenzumrichter regelt dann die Drehzahl höher, um den Verschleiß zu kompensieren. Überwacht man die Drehzahl, lassen sich bei einem festgelegten Wert Ersatzteile bestellen und ein rechtzeitiger Austausch vorbereiten, was der Prozesssicherheit zugute kommt.“
Quelle: KNOLL Maschinenbau GmbH