Trelleborg Launches Low Friction Lightweight Thermoplastic Composite Bearing
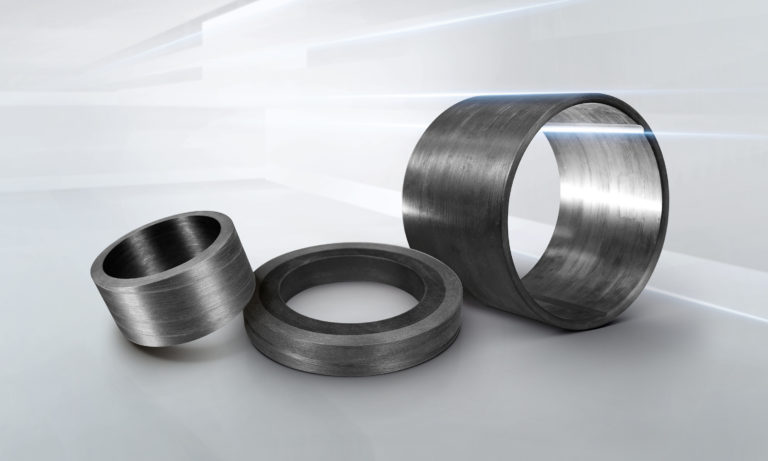
HiMod Advanced Composite Bearings. (Image source: Trelleborg Group)
Manufactured using Trelleborg’s patented Automated Fiber Placement (AFP) technology, a thin low friction liner is bonded to the inner diameters and can be added to the outer diameters of the bearing to create a high-quality solution for use in a wide range of industries. HiMod Advanced Composite Bearing Plus will not seize or gall, unlike metal bearings, to reduce the likelihood of pump damage in chemical processing applications, has a low coefficient of friction, and can withstand extreme temperature ranges.
Reid Hislop, Product Manager at Trelleborg Sealing Solutions, says: “Thermoplastic bearings offer high durability and toughness for demanding applications. The addition of a low-friction layer within our HiMod Advanced Composite Bearing Plus provides up to 50% less sliding friction than with standard bearings, to increase performance and prevent damage to hardware components.
“These unique bearings can operate from an extremely low temperature of -156 OC to +274 OC / -250 OF to +525 OF and are capable of continuous service even when wet, with nearly zero water absorption. Unlike other non-metal bearings, these do not crack or swell in extreme conditions making them a reliable choice for a wide range of applications.”
Trelleborg’s AFP technology is part of a special continuous-fiber thermoplastic composite manufacturing process, which uses pre-impregnated unidirectional composite tapes to produce strong, light-weight composite bearings and other components. The manufacturing process utilizes In-Situ Consolidated (ISC) technology that requires no autoclave or other post processes to eliminate fiber wrinkling and offer an unlimited choice of fiber angles. Components are rapidly formed by a melt-bond process, which removes the need for adhesives, fasteners, or welding. ISC technology enables the bonding of different materials which can result in the creation of new, hybrid structures.
Hislop, continues: “Our low-friction PEEK liner doubles as a highly impermeable sealing surface to provide wide chemical compatibility including solvents and environmental contaminants, and unlike traditional thermoset composites, thermoplastic composites can be recycled at the end-of-life.”
Source: Trelleborg AB