Torque Sensor with Separate Sensing Head Can Probe Deep into Machinery
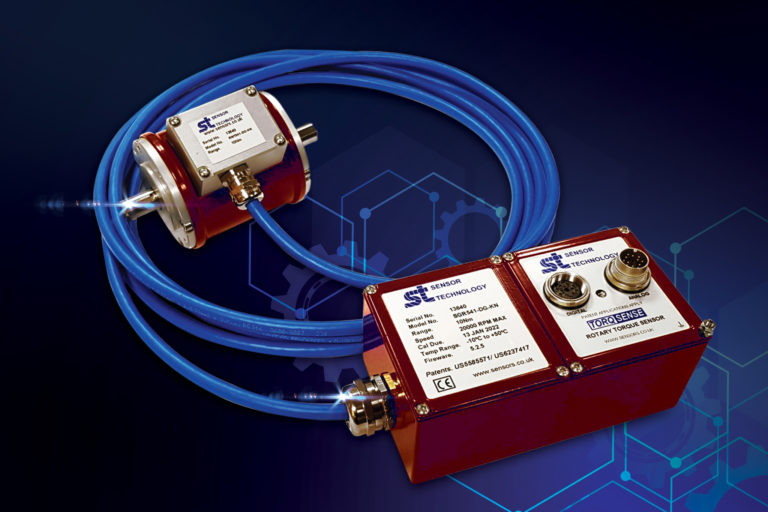
Torque sensor with separate sensing head can probe deep into machinery (Image source: Sensor Technology)
The new TorqSense SGR530/540 series operates on the same principle as all the other SGR510/520 units, namely a full four element strain gauge bridge. This uses four individual stain gauges affixed to the drive shaft; each measures the deflection of the shaft in a different direction as it rotates under load. The electronics collects readings from all four gauges and calculates the torque value.
Sensor Technology launched the TorqSense SGR510/520 range in 2020 as the successor to its RWT range which worked on surface acoustic wave (SAW) measurement and detection. It has specialised in real-time torque measurement for over forty years, and pioneered the development of wireless technologies that use radio frequency pickups rather than hard-wired solutions involving delicate and unreliable slip rings.
Initially launched in sizes up to 500Nm, interest in the SGR sensors was so high that the introduction of larger sizes up to 13,000Nm was brought forward 6-12 months to December 2020.
"Because of our experience with the RWT, we have been able to compress the development times for the new SGR models considerably,” says Sensor Technology’s Mark Ingham. “So, we have been able to react to specific enquiries from individual users and bring forward model launches. "
The new range is designed to meet emerging user requirements, notably accurately recording transient torque spikes. In the past transducers didn’t have the bandwidth to capture these spikes, so they were ignored. However, advances in automation, continuous operation and the increasing need for accurate track and trace data has led to the need for more detailed measurement and analysis, as Mark explains:
"A single spike could indicate say the wrong amount of an ingredient being added to a compound or an over-sized workpiece, both of which could affect product quality. A series of spikes would probably suggest the beginnings of a problem within the machinery, so their detection gives the plant engineers an early warning”.
In use, a rotor mounted ultra-miniature microcontroller, powered by an inductive coil, measures the differential values in each strain gauge and transmits them back to the stator digitally, via the same coil. The SGR510/520 series transducers then use state of the art strain gauge signal conditioning techniques to provide a high bandwidth, low cost torque measuring solution with high overrange and overload capabilities.
An advantage of the design of the SGR torque sensors is that they automatically compensate for any extraneous forces, such as bending moments, inadvertently applied to the sensor. They also offer high sensitivity and have a wide temperature tolerance, attributes that are required more and more and production machinery becomes more and more sophisticated and performance demands increase.
Other advantages of the SGR range include: elimination of noise pickup and signal corruption associated with slip rings and hard wired solutions, a 400% mechanical overload limit with accurate torque measurement even at these extremes, and multipoint calibration to eliminate linearity errors within the sensor.
All units are accurate to +/-0.1% and resolution to +/-0.01% of the transducer’s full scale. Other features include an adjustable moving average filter, power supply range from 12VDC to 32VDC, user settable analogue output voltages, and RS232, USB, CANbus and Ethernet comms options.
"Like the RWT sensors the new SGRs can integrate digitally with TorqView software and LabView virtual instruments," says Mark.
Source: Sensor Technology Ltd