Tailor-Made Pump Monitoring Increases Safety
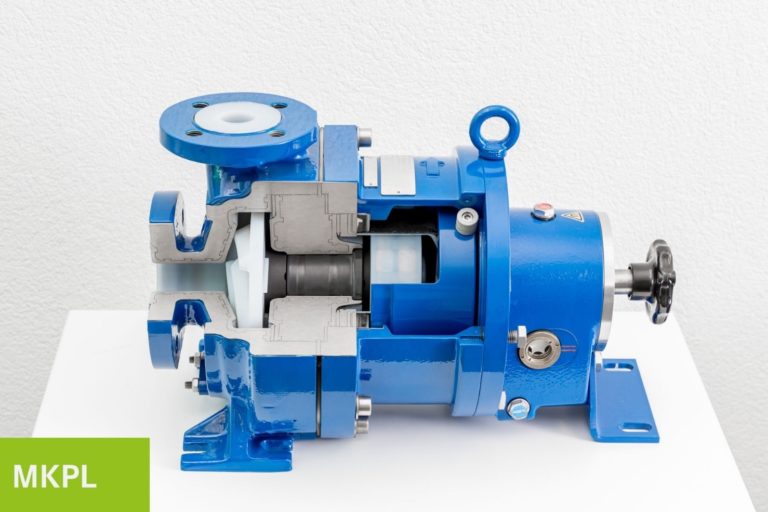
Magnetic drive chemical process pump with PFA lining. (Image source: CP Pumpen AG)
In conjunction with the safe, maintenance-free magnetic drive, this can be a great advantage for smooth, leakage-free production, especially with chemically highly aggressive media.
In pumps with a magnetic coupling, shrouds separate the medium-wetted inner rotor, which is connected to the pump impeller, from the outer rotor of the magnetic coupling, which is connected to the motor. The drive torque is transmitted from the motor to the impeller without contact via the acting magnetic forces. Shrouds must therefore be capable of withstanding the entire pump pressure. As they are in contact with the medium on the inside, they must also exhibit corresponding chemical resistance. Ultimately, they should have the thinnest possible wall and be made from a material that is permeable to the magnetic field lines of the magnetic coupling.
CP Pump Systems uses CFRP-reinforced shrouds made of modified PTFE in the MKPL pumps, which are lined with PFA plastic. The PTFE wall thickness is at least 2.5 mm. The modified PTFE has a particularly high chemical resistance and is leak-tight and safe, even against permeation. These shrouds are reinforced by a high-strength outer layer of carbon fibre reinforced plastic (CFRP). The PTFE liner and carbon fibre layer are one unit at CP and are manufactured in a single work step. This production method is unique, offers maximum strength and connection quality between PTFE and carbon fibres and is thus also a basis for the vacuum resistance of the pumps. PTFE and CFRP are fully permeable to the magnetic field lines of the magnetic coupling, so there are virtually no losses or heating during operation.
As pressure-bearing and medium-wetted casing parts in magnetic drive pumps, shrouds are very important for the leak-tightness and safety of the pumps. For that reason, CP offers various options for monitoring the state of these PTFE shrouds, flexibly adapted to the respective customer requirements.
The pressure monitoring of the intermediate space in a double-wall shroud has long since been established. Due to the necessary separation of the inner and outer wall, however, the advantage of the full connection of the two walls is lost, which can lead to a reduction in the vacuum resistance of plastic shrouds. In addition, such a system only raises the alarm in the case of complete perforation of one of the two walls, which in the case of damage to the PTFE inner wall can lead to contact of the CFRP outer wall (which has a lower chemical resistance) with the medium. If the CFRP reinforcement is damaged, the strength of the entire shroud is at risk.
CP Pump Systems has been offering this pressure monitoring for 25 years, in which case the shrouds are specially equipped for the purpose with a separator between PTFE and CFRP. Due to the restrictions mentioned above, however, CP has now developed a better alternative.
In the newly developed monitoring system, which has been patented by CP Pump Systems, a very thin electrical wire embedded in the layers of the shroud is used for monitoring. The wire runs continuously and covers the complete shroud like a safety net. In the case of an overload or damage to the shroud, this wire breaks and the flow of current through the wire is interrupted, which is detected by a suitable evaluation device. A standard head transmitter with sensor breakage detection, for example, can be connected for the evaluation. When using such a standard transmitter, only the circuit interruption detection of the transmitter is used; no signal is generated beyond that. The advantage of such a transmitter is its worldwide acceptance and familiarity on the market, its price/performance ratio, its explosion protection and its SIL capability.
This new monitoring system is capable of reliably detecting the following types of damage at an early stage:
- Mechanical damage in the interior of the shroud before all carbon fibre layers are severed.
- Mechanical damage on the outside of the shroud before all carbon fibre layers are severed.
- Overload/overpressure in the shroud that causes deformation and micro-cracks in the carbon fibre reinforcement and also destroys the wire in the process.
- Pumping medium that penetrates through the PTFE of the shroud by permeation and could attack the resin bonding of the carbon fibre layers. The wire is corroded and destroyed in the process before the carbon fibre reinforcement becomes too weak.
When using this new system, no gap or intermediate space is necessary between PTFE and carbon fibre (as would be the case with pressure monitoring). The shroud remains a one-piece, stable unit that is complete vacuum-resistant. CP Pump Systems offers both systems as well as a combination of the two.
Source: CP Pumpen AG