Streamline SL-VI High Pressure Pump Offers New Choice of Configuration Possibilities
This summer, KMT Waterjet Systems launches a new series of high pressure pumps for waterjet cutting – the Streamline SL-VI. The new pump models are based on four frames in different sizes and grant KMT customers a wide range of configuration possibilities.
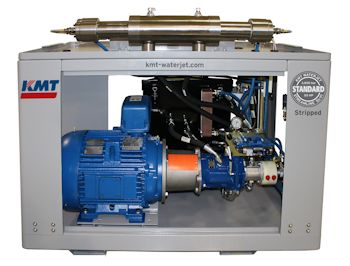
Electric Motor of the hydraulic pump (Image: KMT Waterjet Systems)
The SL-VI series offers various pressure ranges, motorizations and configuration features so that every pump can be tailored to the application it is needed for.
The new high pressure pump series Streamline SL-VI offers a broad range of configuration possibilities so that every machine operator can get the right solution for their respective application. To configure the pump, KMT customers can choose from different pressure ranges and motorizations, and they have a choice of various features to optimize the pump according to their particular demand.
Pressure Range
KMT offers the Streamline SL-VI pump at three pressure levels. The Pro intensifier enables waterjet cutting at 6,200 bar for maximum performance. The model type Plus operates at a pressure level of 4,100 bar, and the type STD allows for a maximum pressure of 3,800 bar.
Motorization
The Streamline SL-VI high pressure pump will be available with motor ratings from 15 to 200 HP (11 to 149 kW).
Configuration and features
The different configuration possibilities range from a model without electrical cabinet, doors and cover for complete integration into the centralized control unit of an entire turnkey system to basic stand-alone machines for occasional cutting needs to fully equipped pumps which enable the most demanding cutting applications.
Top performance and a harmonized PLC platform
The motor of the new high pressure pump series has been upgraded to IE3 according to the norm EC 640/2009 so the KMT Waterjet engineers were able to optimize the motor efficiency. This of course increases the flow rate and with it the maximum orifice size – a fact that allows for higher productivity: For example, the maximum possible orifice size for a 50 HP pump operating at 4,100 bar could be increased from 0.013” to 0.014” (0.33 to 0.35 mm).
Furthermore, KMT has globally harmonized the PLC and HMI platform used for the control of the intensifier pumps. This is especially beneficial for KMT’s business partners that operate internationally: With the SL-VI pump model, all KMT high pressure pumps worldwide will be equipped with the same controls using the same operating pattern. The new controls feature 11 operating languages, soft start to optimize the power consumption as well as a network cable and USB port next to the display. As an option, KMT offers the Stroke Control system for load balancing of multiple high pressure pumps feeding into a common network.
Source: KMT Waterjet Systems Inc.