SPX ClydeUnion CUP-FT/FK Feed Pumps Delivers Reliability and High-Performance
With world energy demand continuing to grow, modern power plants are required to achieve higher loads and efficiencies. Crucial to achieving that goal is the performance of the many pumps throughout a plant. Within modern thermal, combined cycle, gas and solar plants a boiler-feed pump, the pump that feeds water or condensate into the boiler, is a pivotal application and crucial to meeting these challenges.
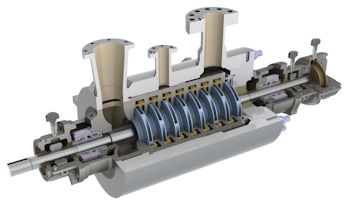
SPX ClydeUnion CUP-FT/FK Feed Pumps (Image: SPX ClydeUnion Pumps)
Since the turn of the century more than 500 pumps have been installed across multiple sites around the globe adding to the existing base of more than 1000, which puts SPX ClydeUnion Pumps at the heart of global power plants.
ClydeUnion Pumps’ experience in manufacturing boiler feed pumps dates back to 1893. The boiler feed pump design philosophy is underpinned by decades of experience of providing highly reliable boiler feed pumps that offer assured generating capacity. This design required a very reliable, incredibly robust, boiler feed pump that assured generating capacity.
The ClydeUnion Pumps CUP-FT/FK is a multi-stage, throughbolt and barrel case, radially-split pump designed for boiler feed applications, meeting the demands of modern thermal, combined cycle and solar power plants. It is a diffuser type pump with options for throughbolt (FT) or barrel case (FK), designed for low, intermediate and high pressure and high temperature applications. It incorporates features such as optimum hydraulic design, sustainable efficiency, and the inherent ability to withstand thermal shock.
With the growth of renewable energy, the demands on a pump are changing. In a traditional baseload scenario, fossil generation power plants would run continuously. But in the modern climate renewable energy is often first choice to supply the power grid meaning that fossil-fuel facilities are shut off when there are periods of sun or wind. Most equipment is designed to run at a constant pressure but can suffer problems when asked to work intermittently. The design of the CUP-FT/FK and its ability to accommodate thermal transients without the need for warm up and superior start-stop capability ensure a breadth of operational requirements can be serviced.
The mechanically-stiff shaft features large shaft to impeller diameter proportions with an optimal span between bearings meaning that it does not bow, wears less and requires less maintenance. The design has been optimised through the use of Computational Fluid Dynamics to deliver optimum NPSH (Net Positive Suction Head), thereby reducing cavitation. The rotor design achieves maximum sustainable efficiency, extended mean time between overhauls and reliability in operation. Designed to low-K factors, the resulting high critical speed margins and low static deflections reduce internal wear and increase reliability. The centreline mounting of the pump reduces thermal growth at elevated process temperatures and maintains pump to driver alignment at all operating temperatures. The high strength fabricated steel baseplate accommodates all static and dynamic loads and reduces noise transmission.
“ClydeUnion Pumps recognises the importance of cleaner energy and the significant impact a boiler feed pump can have on the overall plant output,” Colin Elcoate, VP-Business Development, Power, SPX Power & Energy, said. “This is demonstrated by supplying CUP-FT (2 Pole) boiler feed pumps to one of the world’s cleanest and most efficient integrated gasification combined-cycle (IGCC) facilities. Our efforts are focused on continuously improving and developing our technology to ensure we deliver the most reliable, efficient, and low life-cycle cost products.”
Source: ClydeUnion Pumps