Secado de gas bajo el agua: inyección segura de glicol para la producción de gas natural
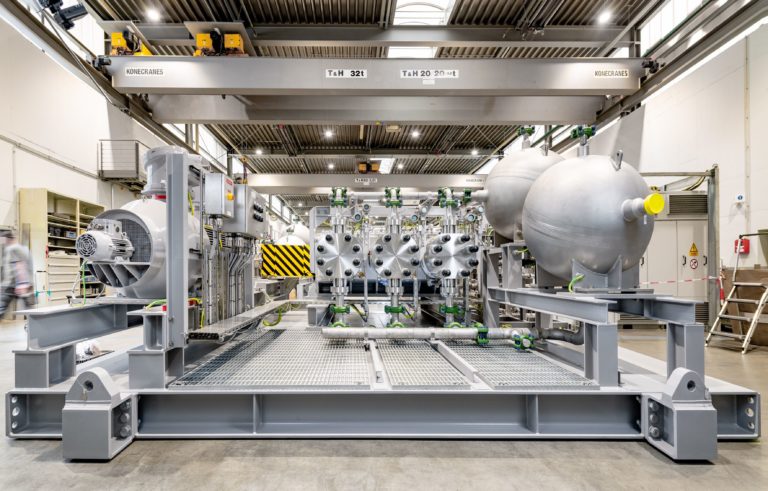
Se instalará un total de tres bombas por rama de producción, y una bomba se mantendrá disponible como unidad de reserva. Esto da como resultado una producción de aproximadamente 36 m³ / h MEG. (Fuente de la imagen: LEWA GmbH)
Esto puede verse afectado por los domos de sal subterráneos en las cavernas, que pueden hacer que el gas extraído tenga un mayor grado de humedad, lo que a su vez dificulta la compresión posterior. La humedad debe eliminarse inyectando glicol y secando así el gas. Esto es necesario en el proyecto actual de un grupo petrolero francés. Después de adquirir los derechos de producción frente a la costa norte de Mozambique, el grupo ha comenzado los preparativos para una producción extensiva de GNL. Dado que las unidades costa afuera a través de las cuales se produce el gas natural no están ubicadas en una plataforma sino bajo el agua, el glicol se bombea desde la costa a través de tuberías directamente a los sitios de producción. LEWA Nikkiso America Inc. recibió el encargo de proporcionar las bombas necesarias para este propósito. Es una subsidiaria de LEWA GmbH, que es conocida por su experiencia y ha estado activa en este campo durante más de 60 años. Por el momento, dos de un total de siete ramas de producción previstas debían equiparse con bombas de membrana de proceso.
"El mayor desafío en este proyecto es sin duda la combinación de la alta contrapresión del sitio de producción y la gran cantidad de monoetilenglicol necesaria, que debe transportarse al pozo durante todo el día. El MEG debe inyectarse continuamente a pesar de esta presión, ", dijo Holger Henze, gerente regional de ventas de LEWA GmbH, que es responsable de la fabricación de las bombas en la sede de la empresa en Leonberg. "Al mismo tiempo, tenemos que asegurarnos de que las bombas sean 100% fiables para que incluso el mantenimiento no provoque una interrupción en el proceso de secado del gas y, por tanto, un retraso costoso de todo el proceso de bombeo. Por último, pero no menos importante, el los agregados deben funcionar lo más económicamente posible ".
Caudal de 18 m³ / h por bomba a una contrapresión de 517 barg
Para contrarrestar estos problemas, las personas responsables de LEWA decidieron utilizar la probada bomba triplex con cabezales de bomba especialmente diseñados para esta aplicación. "La variante G3U en combinación con el cabezal de bomba M800 permite un caudal de 18 m³ / h por bomba, a pesar de la alta contrapresión de 517 barg", explicó Henze. Se instalarán un total de tres bombas por rama de producción, y una bomba se mantendrá disponible como unidad de reserva. Por un lado, esto da como resultado un caudal de aproximadamente 36 m³ / h MEG y, por otro lado, la bomba de reserva puede intervenir si hay que realizar trabajos de mantenimiento en una de las otras bombas. De este modo se garantiza una inyección fiable y constante y se excluye en gran medida la interrupción de la producción de gas natural.
"Los cabezales de la bomba son modelos especiales que también pueden funcionar con un diafragma sándwich de PTFE, gracias a un sistema de sujeción de diafragma diseñado para altas presiones", dijo Henze. "De lo contrario, las bombas comparables deben estar equipadas con un diafragma de metal para resistir la alta presión. Sin embargo, por razones de diseño, tales diafragmas son difícilmente factibles en el tamaño de la unidad de transmisión utilizada en esta clase de potencia". Al mismo tiempo, el cabezal de la bomba ocupa menos espacio y es más compacto que los modelos con el diafragma de metal más rígido, que requeriría un diámetro de diafragma mucho mayor para el mismo grado de desplazamiento. Esto conduciría automáticamente a un diámetro de cabezal de bomba mayor. Para reducir las pulsaciones y evitar daños inducidos por vibraciones, también se utilizan resonadores para garantizar que el medio fluya de manera uniforme. Al igual que las placas base, se fabrican en la planta de LEWA Nikkiso Middle East en Sharjah (Emiratos Árabes Unidos). El montaje final, incluida la tubería, se llevará a cabo en Leonberg.
"Las primeras tres bombas ya han sido aceptadas con éxito por el cliente y el operador después de una prueba de aceptación final (FAT), por lo que planeamos entregarlas a mediados de octubre", informó Henze. "Las bombas restantes también se probarán a fondo en nuestra planta de Leonberg antes de ser enviadas a Mozambique. Esto es para garantizar que no haya sorpresas en el sitio. También estamos seguros de que las otras ramas de producción también pueden equiparse con bombas de LEWA".
Fuente: LEWA GmbH