Séchage du gaz sous l’eau: injection sûre de glycol pour la production de gaz naturel
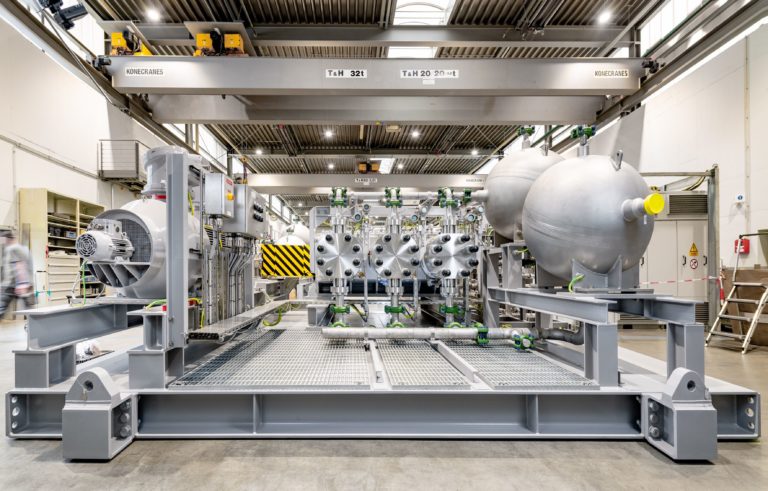
Au total, trois pompes seront installées par branche de production, une pompe restant disponible en tant qu'unité de secours. Il en résulte un débit d'environ 36 m³ / h MEG. (Source de l'image: LEWA GmbH)
Cela peut être perturbé par les dômes de sel souterrains dans les cavernes, ce qui peut entraîner une augmentation du taux d'humidité du gaz extrait, ce qui entrave la compression ultérieure. L'humidité doit être éliminée en injectant du glycol et en séchant ainsi le gaz. Ceci est nécessaire dans le projet actuel d'un groupe français d'huiles minérales. Après avoir acquis les droits de production au large de la côte nord du Mozambique, le groupe a entamé les préparatifs d'une production extensive de GNL. Les unités offshore par lesquelles le gaz naturel est produit ne sont pas situées sur une plate-forme mais sous l'eau, le glycol est pompé depuis la côte via des canalisations directement vers les sites de production. LEWA Nikkiso America Inc. a été chargé de fournir les pompes nécessaires à cet effet. Il s'agit d'une filiale de LEWA GmbH, reconnue pour son expertise et active dans ce domaine depuis plus de 60 ans. Pour le moment, deux des sept branches de production prévues devaient être équipées de pompes process à membrane.
«Le plus grand défi de ce projet est certainement la combinaison de la forte contre-pression du site de production et de la grande quantité de monoéthylène glycol nécessaire, qui doit être acheminée vers le puits 24 heures sur 24. Le MEG doit être injecté en continu malgré cette pression, "a déclaré Holger Henze, directeur régional des ventes chez LEWA GmbH, qui est responsable de la fabrication des pompes au siège de la société à Leonberg. «Dans le même temps, nous devons nous assurer que les pompes sont fiables à 100% afin que même la maintenance n'entraîne pas une interruption du processus de séchage du gaz et donc un retard coûteux de l'ensemble du processus de pompage. les agrégats devraient fonctionner aussi économiquement que possible. "
Débit de 18 m³ / h par pompe à 517 bar de contre-pression
Pour contrer ces problèmes, les responsables de LEWA ont décidé d'utiliser la pompe triplex éprouvée avec des têtes de pompe spécialement conçues pour cette application. «La variante G3U en combinaison avec la tête de pompe M800 permet un débit de 18 m³ / h par pompe, malgré la contre-pression élevée de 517 barg», a expliqué Henze. Au total, trois pompes seront installées par branche de production, une pompe restant disponible comme unité de secours. Il en résulte d'une part un débit d'environ 36 m³ / h MEG et d'autre part, la pompe de réserve peut intervenir si des travaux de maintenance doivent être effectués sur l'une des autres pompes. Une injection fiable et constante est ainsi assurée et l'interruption de la production de gaz naturel est largement exclue.
«Les têtes de pompe sont des modèles spéciaux qui peuvent également fonctionner avec un diaphragme sandwich en PTFE, grâce à un système de serrage de membrane conçu pour des pressions élevées», a déclaré Henze. «Les pompes comparables doivent sinon être équipées d'une membrane métallique pour résister à la haute pression. Cependant, pour des raisons de conception, de telles membranes sont difficilement réalisables dans la taille de l'unité d'entraînement utilisée dans cette classe de puissance.» Dans le même temps, la tête de pompe prend moins de place et est plus compacte que les modèles avec une membrane métallique plus rigide, ce qui nécessiterait un diamètre de membrane beaucoup plus grand pour le même degré de déplacement. Cela conduirait automatiquement à un diamètre de tête de pompe plus grand. Afin de réduire les pulsations et d'éviter les dommages induits par les vibrations, des résonateurs sont également utilisés pour garantir que le fluide s'écoule uniformément. Tout comme les plaques de base, elles sont fabriquées dans l'usine LEWA Nikkiso Middle East à Sharjah (Emirats Arabes Unis). L'assemblage final, y compris la tuyauterie, aura lieu à Leonberg.
«Les trois premières pompes ont déjà été acceptées avec succès par le client et l'opérateur après un test d'acceptation finale (FAT), nous prévoyons donc de les livrer à la mi-octobre», a déclaré Henze. "Les pompes restantes seront également testées de manière approfondie dans notre usine de Leonberg avant d'être expédiées au Mozambique. Ceci afin d'éviter toute surprise sur place. Nous sommes également convaincus que les autres branches de production pourront également être équipées de pompes LEWA."
Source: LEWA GmbH