Revised Dosing and Dispensing Technology Saves Space and Cost
Rethinking entrenched design assumptions to create the space for improvements is a guiding principle that has already enabled Netzsch Pumpen & Systeme GmbH to implement significant improvements in rotary lobe and progressing cavity pumps.
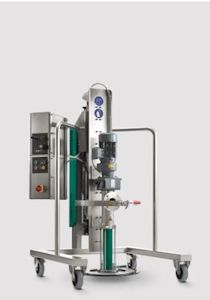
Just two frame types and three designs deliver barrel emptying from 0.5 to 200 litres using different pump sizes. Special requests can also be fulfilled quickly and simply. (Image: Netzsch)
Also considering the dispenser and barrel emptying systems and the, partly, very complex designs, large potential for improvement has been shown in reducing the large variety of components to a more suitable level. The revised designs do not affect the high dosing accuracy and low residues found in the existing Netzsch systems.
The sealing and bearing of the drive shaft in the Nemo dispenser has been re-designed. The design has been simplified and the number of parts reduced, reducing the length by more than 10 mm in all model sizes and bringing down the weight, on average, by 15 percent. The changes create new possibilities for the configuration of production machines, as the small light dispenser, for example, can be carried by a smaller robot, which in turn lowers investment and operating costs. Furthermore, the new technology increases the service life and the smaller quantity of components installed negates the costly storage of spare parts. For easier maintenance, the device can be easily installed and removed by a quick-release plug and socket connection.
Application by the dispenser is highly dynamic thanks to the installed servo drive, while the special rotor-stator geometry of the integrated progressing cavity pump ensures that even compacted, highly filled or shear-sensitive products or media with coarser solid content are transported sensitively. The volume conveyed is directly proportional to the speed of the pump with a volumetric dosing accuracy of ± 1 percent from 90° rotor rotation. A universally adjustable retraction system also prevents any dripping. Depending on requirements and model size, medium can be transported at between 0.2 and 9 ml per rotation irrespective of viscosity and temperature.
Quicker ability to supply due to a modular system
As part of dosing technology, the barrel emptying systems from Netzsch have also been revised and the broad range of different designs has been slimmed down: In future, all required volumes will be covered by just three model sizes. For this purpose, the company from Waldkraiburg has developed two new support frames in which pumps of all sizes up to NM063 can be installed. As a result, barrel emptying systems can be implemented more quickly and simply, even to custom specifications.
The entire system is based on a progressing cavity pump that sits on a follow plate. The plate size is determined by the diameter of the barrel to be emptied, so that the pump can generate a vacuum under the plate and then automatically provide suction towards the bottom of the barrel. As the plate also exerts gentle pressure on the medium, constant transportation is ensured up to a residual quantity of less than 1 percent. As standard, barrels from 20 to 200 litres can therefore be emptied reliably. Special solutions can also handle barrels with volumes of up to 1000 litres. A flow of 6 ml/min to 10 m³/h is possible. Thanks to the progressing cavity pump technology, the quantity conveyed can be regulated within the scope of each model size and accurate dosing directly from the barrel is available.
Smooth operation in the dosing system
On request, dispenser and barrel emptying systems are also available as a complete system with Start/Stop or 1K control units and buffer accumulators. A 1-litre accumulator delivers constant supply pressure, cancels out fluctuations and bridges barrel changes, ensuring that dosing remains accurate and that wear in the dispenser is reduced. For more comprehensive control demands, a touchpanel can be installed. The display or touchpanel provides a clear overview of all the parts of the system, including the relevant process parameters.