Remote Monitoring Ensures Process Reliability
Planning, predictability and process safety are concepts that are integral parts of an effective production environment. To achieve these objectives, a systematic approach is needed. Since 2013, Oerlikon Leybold Vacuum, a manufacturer of vacuum components and systems, uses a monitoring solution in order to support its customer to achieve these objectives.
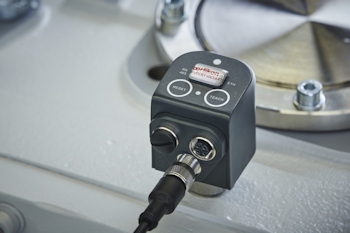
Measuring Data (Image: Oerlikon Leybold Vacuum)
The modern vacuum solutions of the world s leading manufacturer are used in a wide array of technological applications. In rough industrial processes such as steel degassing and also in other industrial high-tech methods such as the production of displays, vacuum pumps and systems are a core component of the manufacturing process and therefore require intelligent maintenance strategies. Based on the monitoring solution, Oerlikon Leybold provides its customers with customized service level agreements (SLA) and guarantees the availability of service experts and warrants fast response times. The condition-based, predictive maintenance strategy offers a maximum plant availability and minimizes unplanned costly production downtimes.
In the field of heat treatment processes, vibration monitoring systems for dry compressed pumps offer enormous potential. Increased wear on the pump is detected as well as influencing process conditions, such as deposit formation or particle entry. Maintenance measures can be initiated when the state of the pump actually requires intervention. Run times are maximized and maintenance staff can be deployed more efficiently. With regard to failure costs, preventive maintenance provides a high return on investment (ROI) and additionally supports a continuous improvement process for the entire maintenance management as well as for production.
In most cases, companies may not even need any additional installation of an expensive sensors. "In a first step, we use the data that our pumps produce anyway" explains Thomas Knecht, Senior Manager Global Field & Remote Service, at Oerlikon Leybold Vacuum. "However, an additional sensor can be used to increase the predictability in more complex tasks."
The condition-based maintenance conducts maintenance measures only when triggered by actual wear. The monitoring solution enables not only the display of trend curves, critical states, and the storage of historical data, but also the calculation of cumulated consumption values. Necessary maintenance work can be displayed on a maintenance plan panel, offering a related maintenance manual while showing the required tools and necessary spare parts.
"In the future, monitoring will be further integrated into our service processes," says Knecht. In the simplest case, a service technician gets the information of a service request directly to his Smartphone. In the next step, a service order is automatically created in SAP and mobilizes a technician or triggers the supply of spare parts on the basis of the stored monitoring data. "Our customers want one thing: system availability! The monitoring solution helps us to help our customers very fast on the basis of the analysis of the monitored data," says Knecht. The service organization will continue to enhance performance in this area and further invest in the training of service technicians to use this system.
Therefore, the monitoring tool increases customer plant availability with a ready-made service solution whilst optimizing the service which Oerlikon Leybold can offer customers. "Here the entire service organization grows - the strategic direction for these measures were already set by the transferring services to the Dresden competence center and also internationally we strengthen our proximity to the customer. The expansion of our customer service locally, as well as the possibilities offered by remote services are crucial points for further success, "says Dr. Martin Füllenbach, CEO Oerlikon Leybold Vacuum.
Source: OC Oerlikon Management AG