Pump Energy Reduction Breakthrough
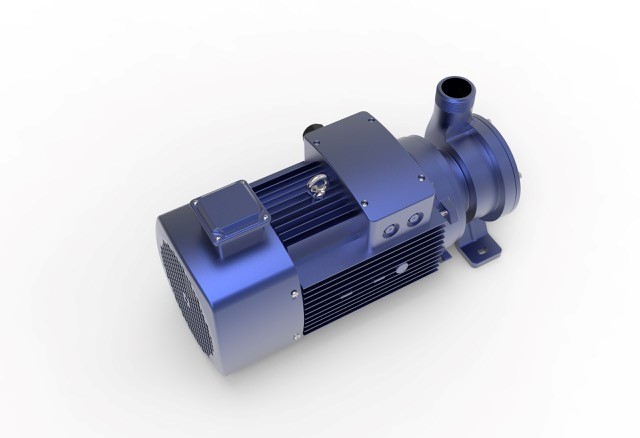
(Image source: New Fluid Technology Pty Ltd)
Certain industry segments eg the pool industry are happy to lower RPM to harness energy savings. These savings come about according to what are known as the “Affinity Rules” that is if the RPM is halved say from 3600RPM to 1800RPM the energy savings is eight times. However the down side is the pressure or head is reduced by four times and the volume is halved. Furthermore neither the Pump wet-end or its motor drive are operating at or near their BEP (best efficiency point). In addition a “suite” or series of pump motor sizes/wattages are required to fill even a small range of head/flow requirements for any given industry segment.
Enter the new “Supa-Stelth” (SS) pump design by NFT Australia. This particular design has recently demonstrated outstanding energy savings by increasing its RPM.
Background
Generally speaking, fixed speed pumps are “synchronised” to the mains frequency supplied by the power grids. In the USA the frequency is 60Hz which locks induction motored pumps to 3600Rpm In Europe and most other places it is 50Hz which locks the standard induction motored pumps to 3000RPM
- A variable speed pump break through that challenges known science
- A Super-Stelth concept pump was recently tested by Purity Pumps of China.
The test's main objective was to double the test pump RPM from 3000rpm to 6000RPM. The tests were done by utilising a frequency controller. This is a device that increases the Herz (or frequency) of a standard induction motor from 50 Hz to 100 Hz, thereby doubling its RPM.
The PUMP HAND BOOK (re as the bible for pump engineers) states:
There are three main Affinity rules as applied to pumps.
- RULE # 1/ when a pumps (speed) RPM is doubled, the volume pumped will double. This is true when applied to the SS test pump and is shown to be correct from the Purity test data increasing from 7.16 cubic metres per hour to 14.2 cubic metres per hour. (See accompanying chart)
- RULE # 2/ when a pumps (speed) RPM is doubled, the pressure (or head) will be squared. This is true for the SS test pump and is shown to be correct from the Purity test data rising from 4.34 metres head to 18.2 metres head.
- RULE # 3/ when a pumps (speed) RPM is doubled, the power consumption will increase by eight times. From the Purity test data, this did not occur with the Supa Stelth concept pump and does not apply because SS pumps operate on a different principle.
The simple explanation is that when the RPM is doubled, the efficiency of a Supa Stelth pump increases from 12.24% @3000rpm to 38.65% @6000RPM. This is a huge rise in efficiency... an increase of three hundred percent, which in turn means the power consumed rose from 691watts, to only 1.861Kwatts …or by just under three times.
If the Affinity rules were correct when applied to the test SS pump, then according to those rules 5.5 Kwatts of power should have been consumed. Another perspective is that up to five times the power was not consumed and was in effect “saved”. All of this resulted from the efficiency rising dramatically as RPM is increased. The provided test data proves that a SS pump does not follow the normal rules for pumps. This should be viewed as an important breakthrough and can be harnessed in future pump designs. For example, designing a Supa-Stelth pump to deliver a specified head/volume outcome by utilising a RPM far above what a conventional pump could ever normally operate at (due to cavitation) delivers large energy savings.
A) Ideal for solar pumps where renewable energy is available. Advantages of increasing the RPM means less solar panels which reduces initial costs
B) Ideal for making pumps much smaller in size for the same head/flow by again utilising higher RPM
C) Ideal for farmers and agriculturalists by allowing one model pump to replace several models …simply by varying RPM
Considering that approx 10% of all electricity on earth and up to 18% of all industrial energy is consumed by pumps, a pump that can increase pressure, flow and efficiency simply by increasing its rpm well beyond the capability of conventional pumps is a major breakthrough indeed.
Source: New Fluid Technology Pty Ltd