Pipeline Pressure Testing Standard Sets Precedent
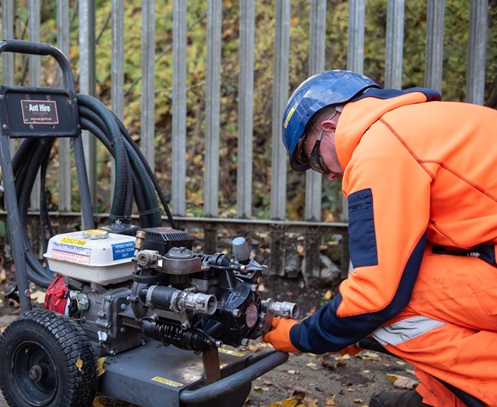
Pressure testing equipment from AHS Pipeline Innovation (Image source: AHS Pipeline Innovation)
Water companies and contractors are adjusting to the requirements of the new Water Industry Standard 4-01-03, released in March 2024, which outlines the required standards for the hydrostatic pressure testing of polyethylene (PE) and polyethylene barrier pipes. The standard replaces previous guidelines from Information Guidance Notice 4-01-03.
The transition from an Industry Guidance Notice (IGN) to a Water Industry Standard (WIS) marks a shift towards more stringent and enforceable standards that aim to improve the safety and effectiveness of the pressure testing process.
WIS 4-01-03 specifies detailed procedures for pressure testing below-ground water supply pipelines and sewer rising mains comprised of PE and PE barrier pipes. It includes guidelines for testing entire systems as well as replacement sections and service connections.
The specifications emphasise the importance of considering the viscoelastic properties of PE, which exhibits what is known as creep behaviour – deformation that occurs when subjected to pressure over time.
Understanding the difference
It is important to understand the distinctions between WIS and IGN:
- An Information Guidance Notice serves as a set of recommendations or guidelines that offer advice on best practice but does not mandate specific actions or procedures.
- A Water Industry Standard is a more formal document that sets out mandatory requirements for products, materials or operational procedures. WIS documents are intended to ensure uniformity and compliance across the water industry, leading to more standardised and reliable outcomes.
Improving safety
The new WIS is designed to improve both the accuracy and safety of pressure testing which means there is now a zero-tolerance policy on pre-pressurisation. Key points are:
- The pipe must be at ambient pressure prior to testing
- If a test has failed, the operator must leave the pipe for four times the length of the ramp-up time before reattempting the test
- The operators must wait for two to three hours between filling and pressurising the pipeline. This takes into consideration the effects of thermal conditioning and allows the temperature of the pipe to stabilise once it has been filled.
- The allowable air content has now been reduced from 8 to 4 per cent
- The air content must also be accurately calculated during the ‘ramp-up’ stage as the pipeline is brought to system test pressure (STP). This means that the test can be immediately abandoned if it is over the acceptable limit.
What WIS means for contractors
There is no question that the new standard represents a significant step towards leak-free networks, but the new requirements potentially impose a greater burden on contractors. The stringent rules around correct preparation prior to testing, including pre-pressurisation, thermal conditioning, and calculating air content prior to starting the test, making it crucial to get the test right first time, to prevent wasting time and resources in retesting.
A reduction in the allowable air content means less margin for error, which highlights, from a compliance and cost perspective, the importance of contractors carefully managing their own and subcontracted pipeline pressure testing.
Due to the increasing complexity of hydrostatic pressure testing and varying levels of expertise among technicians and operators, some pressure testing providers may not meet the standards outlined in the WIS and could lack the knowledge or skills to correctly prepare the pipe for testing.
Contractors must ensure that all pressure testing activity is fully compliant with the new WIS specifications. Substandard testing potentially creates dangerous situations, with risk to life and limb, if air is not properly removed from the pipeline.
It is crucial for contractors to select subcontractors with proven compliance to ensure the safety and reliability of their projects if they are to maintain both contractual obligations and a good reputation in the industry.
Proven expertise
AHS Pipeline Innovation is recognised as an industry leader in hydrostatic pressure testing with over 20 years of experience and almost 50,000 tests completed. The proven expertise of AHS allowed the company to play a key role in the development of the new WIS as part of a multidisciplinary panel which included pipe manufacturers, water company representatives and trade organisations.
Careful consideration was given to onsite implementation of the new requirements, and how contractors can be supported in meeting the standard.
Pressure testing services at AHS are already fully compliant with WIS 4-01-03 and incorporate the latest technology and real-time assistance from the company’s in-house analyst teams to give contractors unrivalled support throughout the testing process, ensuring that testing is right first-time.
AHS is equipped to guide and support teams in adopting these new standards so that their pipeline operations meet the necessary requirements. Should water companies and contractors be unsure about how WIS 4-01-03 affects their operations, or require support to ensure compliance, AHS is available to provide the knowledge and tools necessary to navigate this transition smoothly and effectively.
WIS 4-01-03 not only mandates stricter controls over variables like air content, ambient pressure and temperature, it also effectively identifies and removes any activities undertaken onsite that can affect test performance. Importantly, it reintroduces rules that had been relaxed in previous guidance, restoring rigorous standards that are essential for maintaining the integrity of water systems and creating more defined regulatory expectations.
In addition, pressure tests carried out in accordance with the WIS are measured using sophisticated algorithms that deliver definitive test outcomes, ensuring clarity and reliability.
At a time when the water sector is experiencing reputational challenges, WIS 4-01-03 represents an opportunity for water companies and contractors to get it right from the start. By carefully navigating these changes, and ensuring that every test not only meets but exceeds the latest standards for safety and efficiency, they can mitigate risk to the public and their own teams altogether.
Source: AHS Pipeline Innovation