OptiFlo – the Air-Operated Double-Diaphragm Revolution
With the new OptiFlo design Johnson Pump has succeeded in reducing the drawbacks of conventional air-operated double-diaphragm pumps, like heavy pulsation, costly downtime, noisy operation and cost of spares.
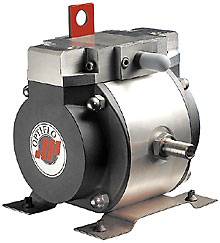
Johnson Pump s OptiFlo (source: Johnson Pump)
Improvements on many fronts
To minimise hydraulic loss, which has always been associated with air-operated double-diaphragm pumps, engineers at Johnson Pump in Sweden, started from scratch. Instead of the long peripheral flow path of existing air-operated double-diaphragm pump solutions, Johnson Pump radical new design has been built around a central flow path that increases the overall efficiency.
While conventional air-operated double-diaphragm pumps normally produce heavy pulsation, OptiFlo pumps generate a flow with reduced pulsation and vibration. This means better performance and lower costs.
The reduced pulsation, which characterises OptiFlo operation, is the result of a complete re-thinking of how twin diaphragms can interact to pump a liquid. Thanks to patented flexible diaphragm suspension (FDS) technology, the diaphragms no longer need to be locked in tandem, but can move slightly independently of each other at both ends of the shaft s stroke. This independent action provides an intake-discharge overlap that reduces pulsation. As an extra bonus of this FDS-design the diaphragms are not exposed to heavy load stress at the turning points and thus the life can be more than doubled compared to a conventional set up with diaphragms locked in tandem.
OptiFlo with FDS and FPV technology
To facilitate the overlapping motion of the two diaphragms, the incoming compressed air is redirected in milliseconds from one air chamber to the other. A conventional pneumatic valve could not be used and a completely new ‘air motor’ was devised and patented – the frictionless pivoting valve (FPV) technology.
The air motor is not only extremely rapid but also insensitive to the quality of air that is used – dry or damp, dirty or oily. It is self-cleaning and non-stalling which improves the operational reliability.
System design flexibility
The ball valves normally used in air-operated double-diaphragm pumps may be efficient, but they are also very noisy, and only operate properly when the pump is in an upright position. OptiFlo uses self closing flap valves instead, which are virtually silent, equally efficient and make it possible for this new pump to run in any mounting position – a dream for machine designers. Flap valves also allow bigger solid particles to pass through the pump more readily, are easier to replace and increase the hydraulic efficiency.
Can be opened in next to no time
Thanks to the extremely simple design the OptiFlo is serviced in minutes. The complete air motor is a separate unit and can be inspected and serviced leaving the pump in place. OptiFlo is a true on-line design and all wearing parts, like check valves and diaphragms, can be serviced or changed at site. No special tools are required and even inexperienced operators can do the job.
Source: SPX Flow Europe Ltd