New Inliner Hose for Flexible, Effective Production
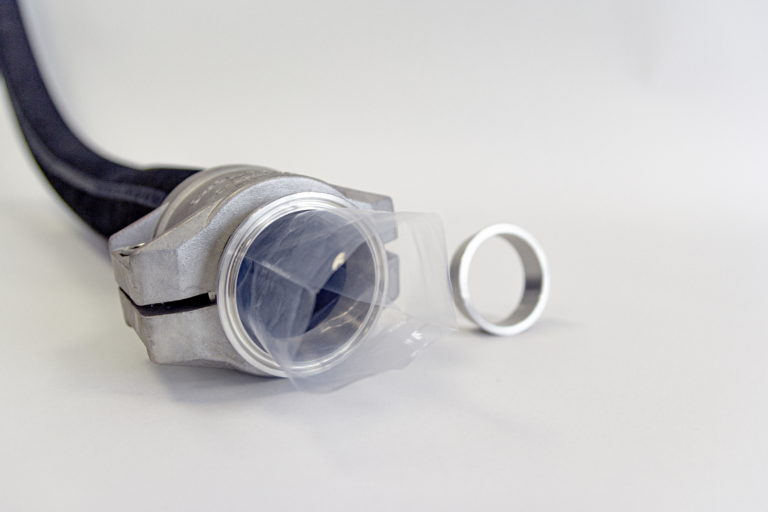
Advantage of the new inliner hose: The product does not come into contact with the actual hose – cleaning is completely unnecessary. (Image source: ViscoTec Pumpen- u. Dosiertechnik GmbH)
This is why customers increasingly approached ViscoTec and asked for a solution to simplify cleaning. The dosing technology specialist turned to Alfons Markert + Co. GmbH / marsoflex with this problem. The two companies have been working together on various projects since 2015.
Patrick Macenka, Technical Sales at ViscoTec, explains more about finding solutions:
- What problems do your customers have to overcome without the in-liners?
Patrick Macenka: To clean a hose containing highly viscous products such as mascara, you have to flush it turbulently and ideally push it out beforehand using a pigging system. The customer requires both systems otherwise such systems need to be obtained. Our task was to find a simple solution that we could providey directly to our customers. Simplified cleaning is particularly important when different materials run on one system.
- Please describe the jointly developed solution.
Patrick Macenka: The outer hose remains the same as many customers already know. We chose a PTFE material because we are convinced of the good sliding properties of this material. An in-liner made of food-safe film is fed through the inside of this hose. Markert has developed a special, innovative system for fastening the in-liner.
- What are the advantages for the customer?
Patrick Macenka: The product does not come into contact with the actual hose. At the end of production, the tube is removed, the special sealing device is released and the foil in-liner is simply pulled out. A new in-liner is fed through and attached and the hose is immediately available again – cleaning is completely unnecessary. This saves valuable working time.
- In which areas, or for which applications can the in-liners be used?
Patrick Macenka: We primarily developed the concept for the cosmetics sector. However, applications are conceivable in many areas in which hose cleaning is required. By using FDA compliant film, we can also serve the food and consumer goods sectors with this solution. Application in the pharmaceutical sector is also possible.