Netzsch: A Robust, Low Wear Rotary Lobe Pump Successfully Extracts High Solids Content Slurry
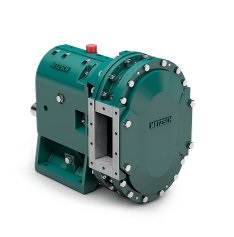
NETZSCH recommended a TORNADO T1 rotary lobe pump for pumping the slurry from the tank. (Image source:NETZSCH Pumpen & Systeme GmbH)
The experts at NETZSCH Pumpen und Systeme GmbH instead recommended a NETZSCH TORNADO T1 rotary lobe pump for pumping the slurry from the tank. This self-priming pump uses the positive displacement principle: Two intermeshing rotors continuously transport the medium from the intake side to the delivery side. The strong suction capability allows the pump to work with a high flow rate and handle a high solids content, while a geared motor with low speed reduces the level of wear. A double mechanical seal and a rotary lobe made of Nitrile rubber minimise the risk of abrasion damage. The TORNADO T1 in size XLB- 3/2 was installed on a mobile trolley and placed near the tank in March 2021. The staff were able to move the hose freely inside the tank and the sediment could be removed without any issues.
At the deposits on the South coast of Peru, around 530 km from the capital Lima, the Shougang Hierro Perú S.A. mining company mines iron ore and processes it into different products. In addition to an open pit of around 150 km², the complex comprises a processing area in the town of San Nicolás with a crushing plant that reduces the ore by 95 per cent as well as a magnetic separation plant, a filter plant and a pelleting plant. The separating plant further crushes and concentrates the ore with cyclones, magnetic separation and flotation. This process separates the sterile ore from the iron ore, which is then divided into two different product types: a high grade iron concentrate for sintering and another that is sent to the pelleting plant after a filtration process.
Reuse of process water affected by high slurry content
Water is required for many of the mine’s working steps. It comes from a 70 x 18 x 8.35 m (l × w × h) process tank which is fed with the medium from concentrate and tailing thickeners. In addition to the water, slurry with magnesium and iron deposits also accumulates in the tank. The liquid rich in solids is pumped over in the tank to then be used in different processes and locations, such as in the magnet plant. “A flocculant is used to recover the slurry from the underflow,” explains Monica Mitterstein, Global Manager Mining & Explosives at NETZSCH. “The water coming from the overflow carries along solids that have accumulated in the tank over the course of many years.” However, the water has to be as clean as possible to be reused in other processes.
Due to years of solids accumulation, there are too many coarse particles in the water that prevent using it in the downstream processes. This made pumping the fluid so difficulty,” continues Mitterstein.
The mine owner initially decided to resolve the issue with a plant stop. The water was drained from the tank and the employees tried to remove the slurry layer, which was already up to 5 m thick, with shovels. “This procedure turned out to be very unsatisfactory, though, because the slurry had become extremely compressed and we had to introduce water again to peel it from the surfaces,” explains Mitterstein. “When the deposits had not been removed after four days, those in charge decided to apply a different method.” They were now considering the option of using a submersible pump with an agitator to remove the slurry during ongoing operation without having to stop the plants and to drain the water again.
Submersible pump not an optimum solution
To procure the required pump, the mine owner contacted NETZSCH Pumpen & Systeme GmbH, but the experts there advised against a submersible pump: “Customer often consider a submersible pump to be the right solution for them. However, in this case such a unit would have had to be very big in order to achieve the required flow rate,” explains Mitterstein. In addition, centrifugal pumps usually run at 3500, 1800 or 1200 rpm – the high speed and the increased solids content would have caused damage to the internal parts of the pump very quickly. “If the speed has to be reduced even further, for example to an 8-pole motor with 950 rpm, then these pumps need to be even bigger to maintain the flow rate. And the motor gains in size as well,” continues Mitterstein. Because submersible pumps have to be made of stainless steel, the Peruvian mining company would have been faced with very high purchasing costs for this pump.
In addition to all this, this type of agitator pump requested by the mine owner is usually only designed for a solids content of up to 50 per cent. However, the solids content in the application in Peru is 60 to 70 per cent, which would have made operation difficult including frequent failures.
TORNADO T1 much better suited for water with a high solids content
After a detailed analysis of the problem and the liquid to be pumped, NETZSCH suggested using a TORNADO T1 pump of size XLB-3/2, which offers a number of advantages over the originally selected submersible pump. The key benefit is that this model is a self-priming displacement pump that can ensure continuous pumping due to its design: Two synchronised rotors inside the pump intermesh, generating negative pressure at the intake side that continuously pulls the medium towards the rotary lobes, which then transport it to the delivery side. This powerful negative suction allows the TORNADO T1 to pump almost any type of medium. This applies to low viscosity and high viscosity substances as well as to thixotropic or dilatant substances, lubricating, non-lubricating, shear-sensitive or abrasive media. “It is therefore ideal for the process water at the mine in Peru and can pump out the medium at a high flow rate despite the high solids content of up to 70 per cent,” says Mitterstein.
The material and design of the T1 are always adapted to the special requirements of the designated medium. For viscous and abrasive materials and those containing solids, NETZSCH offers different rotary lobes with suitable geometries in each case. Materials adapted to the medium additionally increase the durability of the rotary lobes as well as their service life. Tri-lobe helical rotors made of Nitrile are used for the application in Peru to minimise the risk of abrasion damage. In addition, double cartridge mechanical seals are installed which are not sensitive to the solids in the medium. The gear motor of the pump works at a lower speed, which also causes less wear. Overall, this lowers the maintenance costs for the pump significantly.
TORNADO T1 successfully pumps out slurry
To make handling easier for the mining company’s staff, the rotary lobe pump was installed on a mobile trolley and equipped with flexible hoses. This makes it easier to extract the slurry from the tank through the ten ventilation openings at the top of the tank as well as through the corners. The function and capacity of the pump was checked on site in April 2021: “For this first test, the customer used a six-inch hose for intake and delivery. However, they attached a 1.5 m long metal lance to the end of the intake hose which made the hose more difficult to handle,” explains Mitterstein. “The pump was started up and took about 7 minutes to transport the water to the agitators.”
While pumping the water with the solids, the pump maintained the required flow rate. The solids content was 20 per cent on average, with peaks at 30 per cent.
For the second test, the intake hose was replaced with a 4 inch model and a smaller lance was used. Another hose supplied water with a pressure of 6 bar to loosen the slurry that had settled fully. With the new hose and the improved handling of the smaller lance, it was possible to remove the required minimum volume of solids. “After the successful second test, the pump now runs without any problems,” says Mitterstein. “The hose can be moved through the tank easily extracting the solids. The TORNADO XLB-3/2 continuously provides the required flow rate without pressure loss.” After these measures, the process water from the tank still has the required quality for being used in the ore processing without any issues.
Source: NETZSCH Pumpen & Systeme GmbH