KSB Canada Completes Lake Huron High Lift Pump Replacement Project
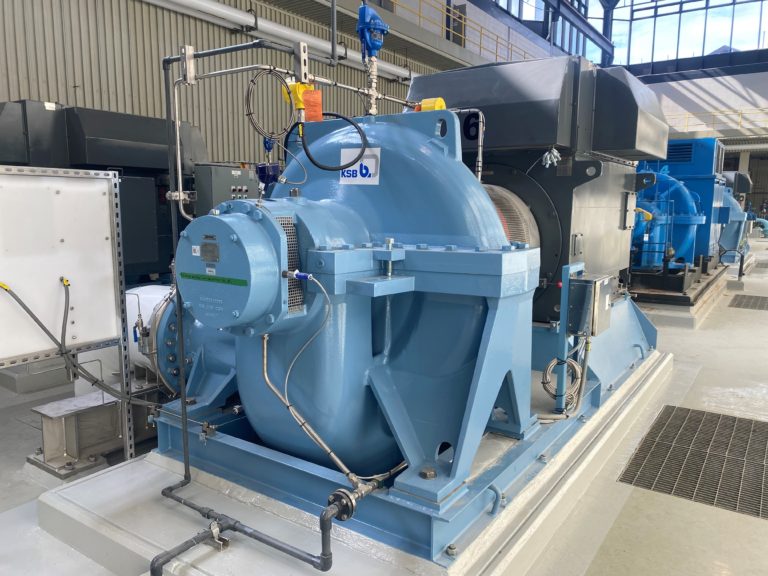
The RDLO pumps are rated for 1,300 L/s or 900 L/sec and each of the pumps’ discharge piping is equipped with a 600mm diameter tilting disk check & throttling valve and isolation ball valve each with a motorized actuator. (Image source: KSB SE & Co. KGaA)
However, in 2017 the Lake Huron Primary Water Supply System (LHPWSS) announced an Energy Audit and Pump Optimization study that identified a significant opportunity for energy savings and the optimization of pump operations for the pumping station.
The outcome of this study has been the modification of the original five pump configuration in the pump station and its replacement with a six pump configuration. This has involved removing three of the original 50-year old 3000hp (2237kW) pumps and replacing them with four high lift pumps from KSB. With the new pumps running on their operational curve, substantial energy savings can be made. As an electrical transmission-connected entity, the LHPWSS was eligible under the Independent Electricity Systems Operator’s (IESO) Industrial Accelerator Program (IEP) for financial incentives for eligible energy efficiency projects.
Four international pump manufacturers submitted bids, but KSB Canada’s submission stood out. Despite being the highest capital expenditure cost by a significant amount, KSB’s submission actually offered the lowest overall anticipated lifecycle cost over 25 years. This was possible due to KSB’s impressive energy efficiency and creative solution in offering a single type for all four pumps (large and small.) This reduced the spares requirement, in turn reducing the lifecycle cost and providing flexibility to easily increase pump capacity in the future as demand continues to increase. The contract was awarded to KSB Canada, who commenced design and consultation work in 2019. Pump manufacturing began in 2020 and the updated pumping station became fully operational August 2022.
Lake Huron Primary Water Supply System
Located in Southwestern Ontario, along the Quebec City-Winsor Corridor, London is an interesting City as it gets its water source from both Lake Huron and Lake Erie. The Regional Water Supply Division of the City of London (RWS) is seconded to the regional Water Boards and responsible for two major water supply systems, these being the LHPWSS and the Elgin Area Primary Water Supply System (EAPWSS). The LHPWSS services the municipalities of London, Lambton Shores, North Middlesex, South Huron, Bluewater, Middlesex Centre, Lucan-Biddulph and Strathroy-Caradoc from a water treatment plant located north of the village of Grand Bend in South Huron. The plant has a current treatment capacity of 340 million liters per day (75 million imperial gallons per day) and serves the city’s population of approximately 420,000 people in the eight municipalities, including 80% of the City of London.
The pumping station was originally designed for a single pipeline, but later in 1996 and 2014 the RWS partially twinned the 47km main transmission pipeline to a terminal reservoir resulting in the pumps no longer running on their curve. “After almost 50 years, the existing pumps were becoming inefficient, with the impellers showing signs of pitting. Keeping them operational required a lot of ongoing maintenance because they were running off curve,” reports Billy Haklander, Capital Program Manager, LH&EAPWSS.
Pump selection
To give the LHPWSS the most flexibility in selecting pumps, four pump suppliers were invited to submit separate bids for the small and large pumps and to identify a credit should the LH&EAPWSS decide to source both the small and large pumps from the same supplier. KSB’s bid offered a creative solution using just a single type for all four pumps, with only the impellers and motors being different in accordance with the size of the pump. The base plates for each pump were the same size. The flexibility offered by KSB enabled the capital cost of its bid to be adjusted to account for fewer spares and thereby create savings for the customer.
A significant benefit of the proposal made by KSB was that with the smaller pumps using the same size casings and base plates as the two larger pumps, they had engineered the opportunity to increase the pump size by fitting larger impellers and motors at a future date. This can be done on site without any civil works needing to be carried out. Thus, if demand grows for the water supply to be increased it can be accommodated with the minimum of cost and disruption to the plant.
Following a 25 year Life Cycle Cost analysis, taking into account the capital cost, energy consumption and maintenance costs made by AECOM Canada, consultants for LH&EAPWSS, the contract was awarded to KSB. Given that the pumps proposed by KSB met the technical requirements and offered the lowest overall anticipated lifecycle cost over 25 years, AECOM and RWS recommended that the proposal from KSB be accepted.
Installation challenges
“One of the constraints that we had to take into consideration when evaluating the bidders’ project was ability to conform to the available space in the existing pump hall “explains Marcus Henderson, KSB National Operations Manager. “With this being an existing installation there was only so much real estate to work with and a key constraint was that the existing pumps were of a bottom suction configuration. Usually, the installation configuration for horizontal split case pumps is in-line with the suction and discharge in the same direction. This meant that we had to find a solution to incorporate bottom suction. We had to undertake some pattern work to incorporate the existing pipework which enabled us to solve the problem.”
“The eventual scope of the project involved the supply of four bottom suction horizontal split case pumps, vibration monitoring system and flow straighteners (suction conditioning spools) for potable water distribution (water supply)”, reports Marcus Henderson. “Also, part of the contract was to supply two TECO make 1494kW/2000hp @ 1200rpm, 4160V / 3Ph/60Hz and two TECO make 2611Kw/3500hp @ 1200rpm, 4160V / 3Ph/60Hz electric motors. We were also responsible for torsional and lateral analysis for the pump sets, on site start-up and commissioning field services.”
The plant’s pumps are rated for 1,158 L/s, and each of the pumps’ discharge piping is equipped with a 500mm diameter tilting disk check valve, along with a 500mm diameter metal seated ball valve equipped with a motorized electric actuator. The WTP has two hydro pneumatic tanks, each with a capacity of 580m³, for transient protection of the 47km partially twinned 1200mm diameter water main distribution system.
The pumps specified were:
2 x RDLO 500-835 B SC G O BS
- Design Flow Capacity: 900 L/s (78 ML/D)
- Design Flow Pump Head: 125m TDH
- Low RPM
- Pump Starting: Soft Starter
2 x RDLO 500-835 A SC G O BS
- Design Flow Capacity: 1,300 L/s (112 ML/D)
- Design Flow Pump Head: 150m TDH
- Low RPM
- Pump Starting: Soft Starter
RDLO Pumps
Proven in many water applications around the world, the RDLO pumps were identified as being more than capable of meeting the customer’s specific demands. KSB’s RDLO axially split, single stage volute pumps have been developed specifically for handling raw water, clean water, service water and transport fluids with a minimum of flow resistance. As a result, they lower the energy and life cycle costs of the systems in which they are installed. They also meet the twin demands of reliability and high availability. Reliability results from the casing halves being sealed by solid casing split flanges at the upper and lower casing part, and high availability is attributable to the use of generously dimensioned bearings and high-quality shaft seals. Smooth running is ensured at all times thanks to the flow-optimised, vortex-free intake elbow and rigid shaft with short bearing span. Because the shaft is completely sealed without steps/threads in the wetted area the RDLO offers reliable power transmission.
The combination of solid bearing brackets, a short and rigid shaft and pre-loaded bearings guarantees low vibration and extended operating life for the bearings, seals and coupling. Being axially split case pumps simplifies maintenance procedures, enabling ready access to all parts for thorough inspection. The drive may be positioned on both the left and right of the pump without additional parts or modifications to the casing being necessary. ”Two of the pumps are connected up to 3500 hp motors and the other two to 2500 hp motors. These are the main pumps supplying drinking water to the entire LHPWSS with many customers over 50km away, so they consume a great amount of energy. It is marginal improvements such as these that can improve efficiency by one or two percent, but they work out to big dollars when you consider the overall size of the plant,” comments Marcus Henderson.
Installation
“Because the pumps were being retrofitted into the original premises, it was necessary to run the plant at half capacity on one transmission side during installation,” explains Billy Haklander. “As there was a spare bay already in the plant it was possible to utilize this for the installation of the first pump. The procedure involved running pumps 1, 2 and 3 while pumps 5 and 6 were being installed. Once these pumps were tested and we were comfortable with their performance the procedure switched to running pumps 4, 5 and 6 while pumps 1, 2, and 3 were being installed.”
The introduction of the new pumps provided the opportunity to retrofit isolation valves. Historically the lack of the isolation valves on the existing pumps required the complete isolation of half of the discharge header board (three pumps) in order to facilitate the repair to one pump, effectively limiting the pump capacity of the plant to half of its rated capacity. The selection of a combined control/check valve to replace two valves on each pump discharge meant that each pump would have a dedicated isolation valve for each pump discharge. Isolation valves on each pump discharge will enable the complete isolation of the combination valve and the high lift pump for maintenance and repair purposes.
Pump efficiency
A significant element of the project was the issue of the pumps delivering energy savings, which involved factory acceptance testing at KSB’s Halle facility in Germany. Henderson explains: “Factory testing involved shipping one motor of each size to our factory and coupling them up to the pumps for string testing and recording the overall pump performance. The motors also underwent type testing under full load in accordance with the IEEE Standard so that they could determine motor efficiency.” He continues: “We took the factory overall power and the data from the motor factory to determine pump efficiency. There were strict penalties on performance guarantees on this project, so if we failed to meet the efficiency guarantees given, KSB would be required to pay LHPWSS the difference in energy costs delivered and those which were guaranteed over the performance lifetime.”
“It is worth noting that when the pump tests were carried out, they had to be on bare internals. The coatings were only applied after testing, so it was a true test of the raw efficiency of the pumps. Given that coating can improve efficiency by one to two percent we faced some tough conditions.”
Conclusion
“The replacement of fifty-year-old high lift pumps at the Lake Huron Water Treatment Plant will result in significant energy savings and optimization of pump operations. The complexities of this large infrastructure project include the installation of two 2,000hp/1494kW and two 3,500hp/2611kW pumps and associated combination control and isolation valves as well as a medium voltage motor control centre, all while maintaining supply to the utility’s regional customers,” says Billy Haklander.
“Working with KSB and the other vendors throughout a global pandemic provided unforeseen challenges, but I was amazed at how well the project went. The people at KSB in Canada were able to set up and accommodate the virtual site acceptance testing program and their engineers at the Halle plant in Germany were great in providing information when it was requested. KSB was at the front in making it a successful project and their collaboration with the key players, in particular Kenaidan Contracting the general contractor responsible for installing the pumps and the mechanical aspects of the project and overseeing the installation of the electrical components by their electrical sub-contractor Selectra, was greatly appreciated,” comments Billy Haklander.
Marcus Henderson explains: “One of the positives to come from this project was that we were able to go ahead with a planned role for a permanent commissioning team. As projects get more complex and extend over longer periods, there is a need for greater consistency, and with this new development we are able to deliver an integrated resource constantly available to our customers.”
Source: KSB SE & Co. KGaA