Instalación de materiales modernos y actualizaciones de diseño mediante proyectos de modernización en plantas químicas.
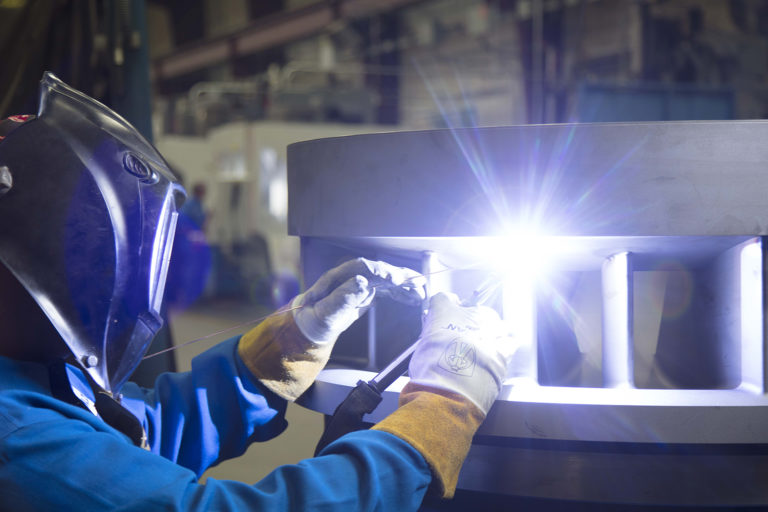
La fabricación personalizada de nuevos componentes puede reducir los plazos de entrega (Fuente de la imagen: Sulzer)
En muchos casos, los equipos rotativos, como turbinas de vapor, generadores, bombas, compresores y expansores, constituyen una parte importante del proceso de producción. A través del uso continuo, el desgaste de los componentes y las holguras aumentan, lo que reduce la eficiencia. Al mismo tiempo, los procesos cambian y se puede esperar una mayor productividad del equipo heredado; Abordar estos desafíos con éxito puede reducir los costos operativos y mejorar la confiabilidad.
Pharic Smith, director de ingeniería, reacondicionamiento de piezas de Sulzer, explica cuántas áreas de una planta de fabricación química moderna pueden beneficiarse de los proyectos de reacondicionamiento.
Optimización del tiempo de actividad
El sector de la fabricación de productos químicos ofrece muchos desafíos, entre ellos el entorno operativo; trabajar con materiales corrosivos y vapor puede aumentar la presión sobre el equipo de mantenimiento. Trabajar con equipos que han estado en servicio durante muchos años, especialmente cuando no hay soporte disponible del fabricante de equipos originales (OEM), significa que se deben encontrar soluciones alternativas cuando se requieren reparaciones y actualizaciones.
Los programas de producción ajustados significan que el tiempo de inactividad debe minimizarse, por lo que siempre se prefiere utilizar un programa de mantenimiento planificado para evitar fallas inesperadas que pueden causar la pérdida de ingresos. Si bien los equipos de mantenimiento en el sitio a menudo están bien versados en el funcionamiento del equipo, el soporte de expertos puede reducir los tiempos de reparación y brindar soluciones rentables para reparaciones más complejas.
Para maximizar la inversión original en equipo, la vida útil debe extenderse tanto como sea económicamente posible. Los proyectos de reacondicionamiento ofrecen la oportunidad de actualizar o reemplazar componentes que pueden aumentar el rendimiento a través de diseños o materiales mejorados.
Soluciones rentables
Las bombas a gran escala se suelen citar para proyectos de modernización porque una vida útil de funcionamiento continuo puede provocar el desgaste de los impulsores / rotores, lo que reduce la eficiencia y aumenta los costos de funcionamiento. Aquellos que operan en la industria de fabricación de productos químicos pueden tener que soportar un entorno de trabajo desafiante.
Por ejemplo, el ácido nítrico, que es una materia prima esencial para la fabricación de fertilizantes, se crea utilizando componentes económicos, amoníaco, agua y aire atmosférico. Sin embargo, el proceso de fabricación es muy intensivo en energía y capital, y utiliza varias turbomáquinas como compresores, bombas, turbinas de expansión de gas de cola y varios motores grandes. Por lo tanto, es importante que los fabricantes mantengan un alto nivel de eficiencia para que el proceso siga siendo rentable.
En lugar de reemplazar activos completos cuando su productividad comienza a caer, es mucho más rentable reparar el componente desgastado e incluso mejorar su diseño al mismo tiempo. La moderna tecnología de escaneo láser tridimensional (3D) significa que no se requieren los dibujos originales del OEM; Las piezas se pueden crear a partir del componente original, incluso si se ha dañado.
Bombas de alimentación de calderas
Muchas plantas de fabricación utilizan vapor para generar su propio suministro de electricidad y estos sistemas dependen de bombas de alimentación de calderas para proporcionar un suministro de agua constante. En muchos casos, estos importantes activos pueden funcionar de manera confiable durante décadas, pero la reducción de la eficiencia afectará el costo de operación. Sin embargo, después de tantos años, es posible que el OEM no esté en condiciones de suministrar piezas nuevas, por lo que se necesita una solución alternativa.
En la actualidad, se pueden crear y fabricar mejoras de sellos y mejoras de eficiencia a través de piezas de desgaste no metálicas y diseños de rotor mejorados utilizando equipos de última generación. Los procesos de diseño modernos y las técnicas de fabricación aditiva pueden reducir en gran medida el tiempo de entrega de piezas nuevas.
Los programas de reacondicionamiento pueden ir mucho más allá y alterar la producción del activo donde la demanda de la bomba ha cambiado a lo largo de los años. Al cambiar los perfiles del impulsor o reducir el número de etapas, la bomba se puede optimizar para su aplicación actual, a menudo reduciendo los requisitos de energía y reduciendo los costos de funcionamiento.
Compresores
Los compresores grandes son habituales en el sector de la fabricación de productos químicos y, a menudo, funcionan las 24 horas. Como tal, la confiabilidad y la eficiencia son muy importantes, por lo que generalmente se implementan programas de mantenimiento rigurosos y equipos de monitoreo de condición.
En muchos casos, los operadores de compresores tienen rotores de repuesto que se pueden cambiar rápidamente, lo que minimiza el tiempo de inactividad y permite más tiempo para reacondicionar el rotor que ha estado en servicio. Sin embargo, este procedimiento no da tiempo para acceder a la sección estacionaria del compresor, que también puede necesitar atención durante una revisión o un proyecto de modernización.
Esto se puede mitigar utilizando tecnología de escaneo láser y creando un modelo CAD en 3D del rotor y la carcasa. Combinando los dos y utilizando tecnología de punta, se puede generar un gráfico de rendimiento para el modelo 3D. Esto puede compararse con los datos reales del propio compresor y usarse para refinar el modelo hasta que sea una representación verdadera.
Mejoras de modelado
Desde este punto, los diseñadores pueden introducir mejoras en el modelo y establecer su influencia en el rendimiento y la eficiencia. Los cambios en los perfiles del impulsor, las mejoras en los cojinetes y los sellos laberínticos se pueden simular y evaluar para establecer los diseños más beneficiosos.
Las tecnologías modernas de fabricación y mecanizado se pueden aplicar no solo para reducir los tiempos de entrega, sino también para crear componentes más eficientes, como impulsores con geometría de paleta 3D. Todos estos se pueden utilizar para mejorar el rendimiento y aumentar el caudal másico si es necesario.
La ventaja del CAD 3D teórico es que las mejoras sugeridas se pueden probar y evaluar para determinar su impacto en otros componentes, como los intercoolers. En algunos casos, la actualización de los auxiliares puede justificarse por el aumento de la producción. Además, todos los datos se pueden examinar para permitir una decisión más informada.
Expansores de gas caliente
Con cantidades tan enormes de energía involucradas en la fabricación de productos químicos, cualquier método de recuperación debe mantenerse adecuadamente para maximizar sus beneficios. El entorno operativo de los expansores de gas caliente significa que están sujetos a condiciones desafiantes con tensiones considerables sobre el rotor y sus cojinetes.
Al girar a velocidades de hasta 11 000 rpm, el rotor debe estar apoyado por cojinetes que puedan soportar las tensiones operativas y brindar confiabilidad a largo plazo. Un proyecto de modernización puede actualizar los cojinetes de manguito cilíndrico a los componentes de la almohadilla de inclinación. Los cojinetes de asiento esférico se pueden reemplazar con un diseño que utiliza rodillos cilíndricos, lo que ofrece un mejor rendimiento a largo plazo.
El rotor en sí tiene un diseño de múltiples etapas donde un eje hueco con conductos de enfriamiento internos mantiene los discos de la turbina y las palas en posición con un solo perno pasante. Este perno está sujeto a una tensión térmica considerable y, a menudo, se mecaniza en acero inoxidable en la especificación de construcción original.
La pieza se puede actualizar a una aleación de acero inoxidable 450 que permite un mayor estiramiento del perno y un mayor aplastamiento del paquete en el conjunto del rotor. Las dimensiones se mecanizan para que coincidan exactamente con el original utilizando los dibujos CAD en 3D y se pueden instalar como parte de una renovación del rotor.
Rendimiento mejorado de la hoja
Los expansores de gas caliente también pueden beneficiarse de una reducción en la fuga de la punta de la hoja, lo que representa pérdidas sustanciales de eficiencia en los equipos heredados. La instalación de un revestimiento abrasible en la superficie interior del estator proporciona un mejor control de holgura para las palas del rotor. Claramente, este tipo de actualización requiere que el expansor esté bajo mantenimiento durante un período prolongado, por lo que es más adecuado para un período de apagado planificado.
Pueden lograrse mejoras adicionales mejorando los materiales utilizados para fabricar las propias hojas. En aplicaciones que requieren alta resistencia y buena resistencia a la corrosión hasta 1'300 ° F (700 ° C), el uso de una súper aleación, como A286, en las hojas puede ser beneficioso.
Por supuesto, con los álabes de las turbinas que operan en entornos de alta temperatura, las turbinas de gas tienen varias características en común con los expansores de gas y, como tales, se pueden aplicar tecnologías similares a ambos. Los avances en los recubrimientos de las palas pueden reducir el ensuciamiento y la oxidación tanto en las secciones giratorias como estacionarias.
Turbinas de gas
Los equipos importantes, como las turbinas de gas, pueden proporcionar fuentes de alimentación tanto primarias como de respaldo, por lo que su confiabilidad es primordial. Con el tiempo, tanto los fabricantes de equipos originales como los proveedores de mantenimiento independientes han desarrollado mejoras de diseño que pueden aplicarse al equipo instalado mediante proyectos de modernización.
Por ejemplo, en las turbinas de gas de la serie V de Siemens, el anillo F del tubo de llama tiene una tendencia a oxidarse y producir incrustaciones que pueden ser ingeridas por la turbina durante las condiciones normales de funcionamiento. Para mejorar esta situación, el componente se puede mecanizar para exponer material fresco y permitir que se suelde una capa de Inconel a la nueva superficie antes de volver a mecanizar al diámetro requerido. Inconel 82 es una aleación de níquel-cromo con alta resistencia y una excelente resistencia a la corrosión que mejorará la durabilidad del componente.
De manera similar, la sección de combustión de la turbina de gas se puede proteger con un revestimiento de barrera térmica (TBC) aplicado a todos los tubos de llama y otros componentes de la trayectoria del gas caliente. Un TBC de cerámica aplicado a los anillos del bisel y las placas de segmento, los codos de mezcla y la carcasa interior, aumenta la resistencia al estrés térmico en las áreas más calientes de la unidad.
Se pueden realizar otras mejoras en el rendimiento de enfriamiento de ciertas piezas, como el tubo de llama, para aumentar la durabilidad de las piezas al reducir la oxidación y la erosión. Juntas, todas estas mejoras pueden extender la confiabilidad y asegurar la eficiencia continua de la turbina de gas.
Cumpliendo con nuevos estándares
A medida que los equipos heredados continúan brindando un servicio confiable, los estándares modernos evolucionan en beneficio del medio ambiente y la mejora de la operación y la eficiencia. Muchos de estos se pueden aplicar retrospectivamente y, a menudo, es más rápido y más rentable modificar la maquinaria existente, en lugar de reemplazarla con equipo nuevo.
Comprender lo que se puede lograr con un proyecto de modernización y la mejor manera de aplicarlo son habilidades importantes que se adquieren a través de la experiencia tanto en la industria en cuestión como en el desarrollo de soluciones de vanguardia. Al desarrollar modelos teóricos y afinar el diseño, los ingenieros pueden resaltar los beneficios y asegurarse de que el equipo sea adecuado para la renovación.
La capacidad de mejorar la eficiencia y reducir el consumo de energía mediante la ingeniería moderna también ofrece la oportunidad de reducir la huella ambiental de la empresa. A medida que se ejerce más presión sobre las plantas industriales para mejorar el impacto ambiental de sus operaciones, el proyecto de modernización tiene el potencial de generar una reducción de costos y de emisiones de CO2.
Cosechando los beneficios
Cada pieza de equipo de la planta presenta sus propios desafíos, pero es posible abordar muchos de ellos trabajando con ingenieros experimentados que comprendan las demandas del proceso, así como el diseño del equipo involucrado. El uso de un programa de actualización bien definido e integrado puede generar mejoras significativas en la vida útil esperada del equipo, así como mejorar la productividad.
Los proyectos de modernización representan una oportunidad para la introducción rentable y eficiente de nuevos componentes que utilizan materiales y técnicas de fabricación modernas. La capacidad de crear piezas únicas rápidamente, sin dibujos de OEM, minimiza el tiempo de inactividad y garantiza una respuesta exitosa durante una interrupción planificada.
Al realizar mejoras significativas en la eficiencia y confiabilidad, las plantas químicas pueden reducir su emisión de CO2 al hacer un mejor uso de la energía de los gases residuales, lo que a su vez reduce la cantidad de energía que se requiere de los generadores de vapor. Los proveedores de servicios independientes pueden ofrecer experiencia en la reducción de pérdidas, la mejora del rendimiento de la turbina y la actualización de los equipos rotativos, lo que permite a los fabricantes de productos químicos ver un rendimiento mejorado y unos costes de ciclo de vida mejorados.
Fuente: Sulzer Ltd.