Installation de matériaux modernes et mise à niveau de la conception grâce à des projets de modernisation dans des usines chimiques
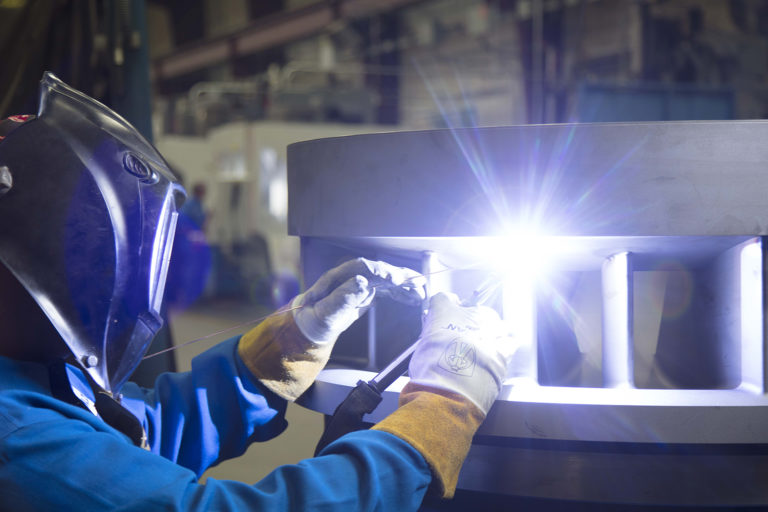
La fabrication sur mesure de nouveaux composants peut réduire les délais (Source de l'image: Sulzer)
Dans de nombreux cas, les équipements rotatifs, tels que les turbines à vapeur, les générateurs, les pompes, les compresseurs et les détendeurs, constituent une partie importante du processus de production. Grâce à une utilisation continue, l'usure des composants et les jeux augmentent, entraînant une efficacité réduite. Dans le même temps, les processus changent et on peut s'attendre à une plus grande productivité de l'équipement existant; relever ces défis avec succès peut réduire les coûts d'exploitation et améliorer la fiabilité.
Pharic Smith, responsable de l'ingénierie, Rénovation des pièces chez Sulzer, explique combien de zones d'une usine de fabrication de produits chimiques moderne peuvent bénéficier de projets de rénovation.
Optimiser la disponibilité
Le secteur de la fabrication de produits chimiques présente de nombreux défis, notamment l'environnement opérationnel, travailler avec des matériaux corrosifs ainsi que de la vapeur peut augmenter la pression sur l'équipe de maintenance. Travailler avec des équipements qui sont en service depuis de nombreuses années, en particulier lorsqu'il n'y a pas de support disponible auprès du fabricant d'équipement d'origine (OEM), signifie que des solutions alternatives doivent être trouvées lorsque des réparations et des mises à niveau sont nécessaires.
Des calendriers de production serrés signifient que les temps d'arrêt doivent être minimisés. L'utilisation d'un programme de maintenance planifiée est toujours préférable pour éviter les pannes imprévues qui peuvent entraîner une perte de revenus. Alors que les équipes de maintenance sur site sont souvent bien familiarisées avec le fonctionnement de l'équipement, l'assistance d'experts peut réduire les temps de réparation et fournir des solutions rentables pour des réparations plus complexes.
Pour maximiser l'investissement initial dans l'équipement, la durée de vie doit être prolongée autant que possible économiquement. Les projets de modernisation offrent la possibilité de mettre à niveau ou de remplacer des composants qui peuvent augmenter les performances grâce à une conception ou des matériaux améliorés.
Solutions rentables
Les pompes à grande échelle sont souvent citées pour les projets de modernisation car une durée de vie de fonctionnement continu peut conduire à l'usure des roues / rotors, ce qui réduit l'efficacité et augmente les coûts de fonctionnement. Les personnes opérant dans l'industrie de la fabrication de produits chimiques peuvent devoir endurer un environnement de travail difficile.
Par exemple, l'acide nitrique, qui est une matière première essentielle pour la fabrication d'engrais, est créé en utilisant des composants bon marché, de l'ammoniac, de l'eau et de l'air atmosphérique. Cependant, le processus de fabrication est très énergivore et capitalistique, utilisant plusieurs turbomachines telles que des compresseurs, des pompes, des turbines à détente de gaz de queue et plusieurs gros moteurs. Il est donc important que les fabricants maintiennent un haut niveau d'efficacité pour que le procédé reste rentable.
Plutôt que de remplacer des actifs complets lorsque leur productivité commence à baisser, il est beaucoup plus rentable de réparer le composant usé et même d'améliorer sa conception en même temps. La technologie moderne de numérisation laser tridimensionnelle (3D) signifie que les dessins OEM originaux ne sont pas nécessaires; les pièces peuvent être créées à partir du composant d'origine, même s'il a été endommagé.
Pompes d'alimentation de chaudière
De nombreuses usines de fabrication utilisent la vapeur pour produire leur propre approvisionnement en électricité et ces systèmes reposent sur des pompes d'alimentation de chaudière pour fournir un approvisionnement en eau constant. Dans de nombreux cas, ces actifs importants peuvent fonctionner de manière fiable pendant des décennies, mais une efficacité réduite aura des conséquences néfastes sur les coûts d'exploitation. Cependant, après tant d'années, l'OEM peut ne pas être en mesure de fournir de nouvelles pièces, une solution alternative est donc nécessaire.
Aujourd'hui, des améliorations des joints et des améliorations d'efficacité grâce à des pièces d'usure non métalliques et à des conceptions de rotor améliorées peuvent être créées et fabriquées à l'aide d'équipements de pointe. Les processus de conception modernes et les techniques de fabrication additive peuvent réduire considérablement le délai de livraison de nouvelles pièces.
Les programmes de modernisation peuvent aller beaucoup plus loin et modifier le rendement de l'actif là où la demande de la pompe a changé au fil des ans. En modifiant les profils de roue ou en réduisant le nombre d'étages, la pompe peut être optimisée pour son application actuelle, ce qui réduit souvent les besoins en énergie et les coûts de fonctionnement.
Compresseurs
Les gros compresseurs sont monnaie courante dans le secteur de la fabrication de produits chimiques et ils fonctionnent souvent 24 heures sur 24. En tant que tels, la fiabilité et l'efficacité sont très importantes, de sorte que des calendriers d'entretien rigoureux et des équipements de surveillance de l'état sont généralement en place.
Dans de nombreux cas, les opérateurs de compresseurs détiennent des rotors de rechange qui peuvent être remplacés rapidement, ce qui minimise les temps d'arrêt et laisse plus de temps pour remettre à neuf le rotor qui a été en service. Cependant, cette procédure ne donne pas le temps d'accéder à la section fixe du compresseur, qui peut également nécessiter une attention lors d'une révision ou d'un projet de modernisation.
Cela peut être atténué en utilisant la technologie de balayage laser et en créant un modèle CAO 3D du rotor et du boîtier. En combinant les deux et en utilisant une technologie de pointe, un graphique de performances pour le modèle 3D peut être généré. Cela peut être comparé aux données réelles du compresseur lui-même et utilisé pour affiner le modèle jusqu'à ce qu'il soit une vraie représentation.
Améliorations de la modélisation
À partir de là, les concepteurs peuvent apporter des améliorations au modèle et établir leur influence sur le rendement et l'efficacité. Les changements dans les profils des roues, les améliorations apportées aux roulements et aux joints à labyrinthe peuvent tous être simulés et évalués pour établir les conceptions les plus avantageuses.
Les technologies modernes de fabrication et d'usinage peuvent être appliquées non seulement pour réduire les délais, mais également pour créer des composants plus efficaces, tels que des roues à géométrie 3D. Ceux-ci peuvent tous être utilisés pour améliorer les performances et augmenter le débit massique si nécessaire.
L'avantage de la CAO 3D théorique est que les améliorations suggérées peuvent être testées et évaluées pour leur impact sur d'autres composants, tels que les refroidisseurs intermédiaires. Dans certains cas, la modernisation des auxiliaires peut être justifiée par l'augmentation de la production. En outre, les données peuvent toutes être examinées pour permettre une décision plus éclairée.
Détendeurs à gaz chaud
Avec ces énormes quantités d'énergie impliquées dans la fabrication de produits chimiques, toute méthode de récupération doit être correctement entretenue pour maximiser ses avantages. L'environnement de fonctionnement des détendeurs à gaz chauds signifie qu'ils sont soumis à des conditions difficiles avec des contraintes considérables sur le rotor et ses roulements.
Tournant à des vitesses allant jusqu'à 11 000 tr / min, le rotor doit être soutenu par des roulements capables de résister aux contraintes opérationnelles et d’assurer une fiabilité à long terme. Un projet de modernisation peut mettre à niveau les paliers à manchon cylindrique pour faire basculer les composants du coussin. Les roulements à siège sphérique peuvent être remplacés par une conception utilisant des rouleaux cylindriques, offrant de meilleures performances à long terme.
Le rotor lui-même a une conception à plusieurs étages où un arbre creux avec des passages de refroidissement internes maintient les disques et les aubes de la turbine en position avec un seul boulon traversant. Ce boulon est soumis à une contrainte thermique considérable et est souvent usiné en acier inoxydable dans les spécifications de construction d'origine.
La pièce peut être mise à niveau vers un alliage d'acier inoxydable 450 qui permet une augmentation de l'étirement du boulon et un plus grand écrasement du faisceau sur l'ensemble du rotor. Les dimensions sont usinées pour correspondre exactement à l'original à l'aide des dessins CAO 3D et peuvent être installées dans le cadre d'une rénovation du rotor.
Amélioration des performances de la lame
Les détendeurs à gaz chaud peuvent également bénéficier d'une réduction des fuites au bout des pales, ce qui entraîne des pertes d'efficacité substantielles dans les équipements existants. L'installation d'un revêtement abradable sur la surface intérieure du stator offre un meilleur contrôle du jeu pour les pales du rotor. De toute évidence, ce type de mise à niveau nécessite que le module d'extension soit en maintenance pendant une période prolongée, il est donc le mieux adapté à une période d'arrêt planifiée.
D'autres améliorations peuvent être obtenues en améliorant les matériaux utilisés pour fabriquer les lames elles-mêmes. Dans les applications nécessitant une résistance élevée et une bonne résistance à la corrosion jusqu'à 1’300 ° F (700 ° C), l’utilisation d’un super alliage, tel que le A286, dans les lames peut être bénéfique.
Bien entendu, avec des aubes de turbine fonctionnant dans des environnements à haute température, les turbines à gaz ont plusieurs caractéristiques en commun avec les détendeurs à gaz, et en tant que telles, des technologies similaires peuvent être appliquées aux deux. Les développements dans les revêtements de lame peuvent réduire l'encrassement et l'oxydation dans les sections rotatives et stationnaires.
Turbines à gaz
Les équipements importants, tels que les turbines à gaz, peuvent fournir à la fois des alimentations primaires et de secours. Leur fiabilité est donc primordiale. Au fil du temps, des améliorations de conception ont été développées à la fois par les équipementiers et les fournisseurs de maintenance indépendants et celles-ci peuvent être appliquées à l'équipement installé par le biais de projets de rénovation.
Par exemple, dans les turbines à gaz Siemens de la série V, l'anneau en F du tube à flamme a tendance à s'oxyder et à produire du tartre qui peut être ingéré par la turbine dans des conditions de fonctionnement normales. Pour améliorer cette situation, le composant peut être usiné pour exposer de la matière fraîche et permettre à un revêtement en Inconel d'être soudé à la nouvelle surface avant d'être réusiné au diamètre requis. L'Inconel 82 est un alliage de nickel-chrome avec une résistance élevée et une résistance à la corrosion exceptionnelle qui améliorera la durabilité du composant.
De même, la section de combustion de la turbine à gaz peut être protégée avec un revêtement de barrière thermique (TBC) appliqué à tous les tubes de flamme et autres composants du chemin de gaz chaud. Un TBC en céramique appliqué sur les anneaux de lunette et les plaques de segment, mélangeant les coudes et le boîtier intérieur, augmente la résistance à la détresse thermique dans les zones les plus chaudes de l'unité.
D'autres améliorations peuvent être apportées aux performances de refroidissement de certaines pièces, telles que le tube à flamme, pour augmenter la durabilité des pièces en réduisant l'oxydation et l'érosion. Ensemble, toutes ces améliorations peuvent accroître la fiabilité et assurer une efficacité continue de la turbine à gaz.
Répondre aux nouvelles normes
À mesure que les équipements hérités continuent de fournir un service fiable, les normes modernes évoluent au profit de l'environnement et de l'amélioration du fonctionnement et de l'efficacité. Bon nombre de ceux-ci peuvent être appliqués rétrospectivement, et il est souvent plus rapide et plus rentable de modifier les machines existantes, plutôt que de les remplacer par de nouveaux équipements.
Comprendre ce qui peut être réalisé par un projet de modernisation et la meilleure façon de l'appliquer sont des compétences importantes acquises grâce à l'expérience à la fois dans l'industrie en question et dans le développement de solutions de pointe. En développant des modèles théoriques et en affinant la conception, les ingénieurs peuvent mettre en évidence les avantages et s'assurer que l'équipement est adapté à la rénovation.
La capacité d'améliorer l'efficacité et de réduire la consommation d'énergie grâce à une ingénierie moderne offre également la possibilité de réduire l'empreinte environnementale de l'entreprise. Au fur et à mesure que la pression est exercée sur les installations industrielles pour améliorer l'impact environnemental de leurs opérations, le projet de rénovation a le potentiel de fournir à la fois une réduction des coûts et des émissions de CO2.
Récolter les avantages
Chaque équipement de l'usine présente ses propres défis, mais il est possible de relever bon nombre d'entre eux en travaillant avec des ingénieurs expérimentés qui comprennent les exigences du processus ainsi que la conception de l'équipement impliqué. L'utilisation d'un programme de mise à niveau bien défini et intégré peut apporter des améliorations significatives à la durée de vie prévue de l'équipement ainsi qu'une amélioration de la productivité.
Les projets de modernisation représentent une opportunité pour l'introduction rentable et efficace de nouveaux composants qui utilisent des matériaux et des techniques de fabrication modernes. La possibilité de créer rapidement des pièces uniques, sans dessins OEM, minimise les temps d'arrêt et garantit un délai d'exécution réussi lors d'une panne planifiée.
En améliorant considérablement l'efficacité et la fiabilité, les usines chimiques peuvent réduire leurs émissions de CO2 en faisant une meilleure utilisation de l'énergie provenant des gaz résiduaires, ce qui réduit à son tour la quantité d'énergie requise pour les générateurs à vapeur. Les fournisseurs de services indépendants peuvent offrir une expertise dans la réduction des pertes, l'amélioration des performances des turbines et la mise à niveau des équipements rotatifs, permettant aux fabricants de produits chimiques de voir des performances améliorées et des coûts de cycle de vie améliorés.
Source: Sulzer Ltd.