Editorial: La optimización de bombas y expansores reduce los costos operativos y extiende la vida útil
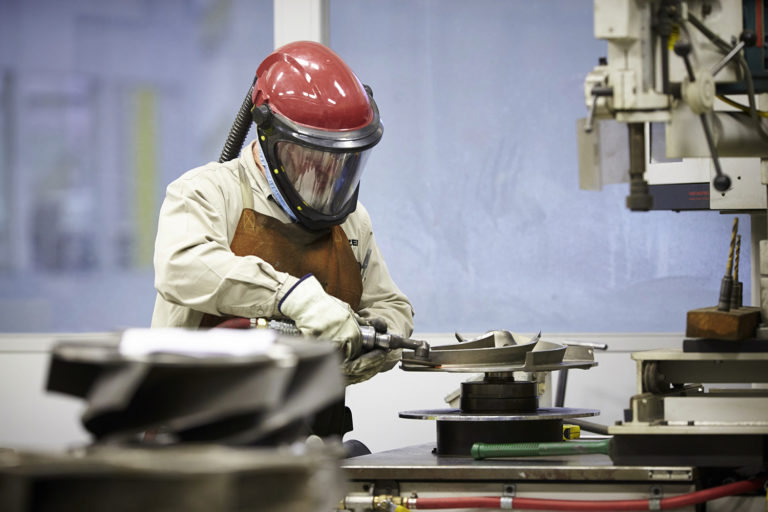
Las modificaciones del impulsor pueden mejorar la eficiencia cuando cambian las aplicaciones (Fuente de la imagen: Sulzer Ltd.)
Charles Soothill, director de tecnología de la división de servicios de Sulzer, analiza algunos de los avances recientes en la tecnología de equipos rotativos y cómo se pueden implementar para mejorar el rendimiento y minimizar los costos.
Todos los días utilizamos productos de la industria de los hidrocarburos; combustible para el viaje al trabajo, gas para cocinar la cena o los plásticos que se utilizan para hacer carcasas para nuestros dispositivos electrónicos. Esta industria está estrechamente vinculada a nuestras vidas y, por lo tanto, cualquier mejora que reduzca los costos operativos nos beneficiará a nosotros, los usuarios finales.
Las bombas y expansores de alta energía juegan un papel vital en el sector de los hidrocarburos y cada uno tiene sus propios desafíos. La eficiencia es esencial en ambas aplicaciones para garantizar el uso óptimo de la energía, que es uno de los mayores costos operativos de la industria. Con el funcionamiento continuo, los procesos perjudiciales, como la erosión y la corrosión, afectan significativamente las tolerancias de las paletas, los sellos y las holguras del impulsor. Sin una intervención oportuna, estos pueden provocar pérdidas considerables.
Bombas
Normalmente, las bombas grandes están diseñadas para una vida útil prolongada; sin embargo, cuando el rendimiento comienza a deteriorarse, a menudo es una señal de que la voluta o el impulsor se han desgastado o corroído. En muchos casos, habiendo brindado décadas de servicio confiable, encontrar piezas nuevas puede ser un desafío que, incluso si tiene éxito, puede significar un largo tiempo de espera antes de la entrega. Afortunadamente, lo último en tecnología de diseño y procesos de fabricación puede reducir significativamente el tiempo y el costo involucrados en la creación de piezas de repuesto.
En situaciones en las que los fabricantes de equipos originales (OEM) pueden crear piezas para máquinas heredadas, este servicio puede tener una demora ya que podría ser necesaria una construcción especial. La ventaja del OEM aquí es la disponibilidad de planos originales para las piezas; sin embargo, reasignar el equipo de producción a un proyecto único puede incurrir en costos adicionales y retrasos en la entrega, a menos que se disponga de un proceso alternativo.
Afortunadamente, la tecnología moderna ofrece una solución que pueden implementar tanto los fabricantes de equipos originales como los reparadores y los proveedores de repuestos especializados. El advenimiento de la ingeniería inversa utilizando sofisticadas máquinas de medición de coordenadas, software de modelado de sólidos en 3D y escaneo láser hace posible recrear piezas complejas en plazos cortos.
Modernización y recalificación de bombas
Los avances en la tecnología de diseño han ido acompañados de desarrollos similares en la ciencia de los materiales que, en conjunto, permiten actualizar los diseños originales. Las bombas más antiguas fabricadas con materiales como el bronce y el hierro fundido, que no se pueden soldar, pueden alargar su vida útil utilizando acero inoxidable u otras aleaciones avanzadas.
En muchos casos, las condiciones de funcionamiento originales para las que se diseñó la bomba habrán evolucionado desde la primera puesta en servicio de la bomba. Dichos cambios pueden conducir a una reducción tanto en el rendimiento como en la eficiencia, pero pueden solucionarse durante una reparación o revisión importante.
Al crear un nuevo impulsor, el diseño hidráulico se puede volver a optimizar para las condiciones de funcionamiento; muy a menudo, esto reducirá los requisitos de energía y dará lugar a reducciones significativas en los costes operativos. Con el software de diseño más reciente y la dinámica de fluidos computacional (CFD), los componentes de ingeniería inversa se pueden ajustar para brindar un rendimiento hidráulico óptimo.
Desarrollos de fabricación
El tiempo necesario para crear nuevos componentes para activos de alto valor, como bombas de alta energía y expansores, se ha reducido significativamente recientemente con la llegada de los equipos de fabricación híbridos. Procesos como la deposición de metal por láser y el fresado de cinco ejes se pueden realizar en una sola máquina, lo que permite una producción rápida.
Por ejemplo, se puede crear un impulsor a partir de un núcleo forjado que se mecaniza utilizando métodos de 5 ejes para establecer la forma básica. Luego, un láser derrite una corriente de polvo y deposita una capa de metal nuevo en la superficie. Esto permite que se acumule rápidamente un gran volumen de material. Luego, la superficie dura se puede mecanizar a las dimensiones finales, todo en la misma máquina.
La flexibilidad de este método de fabricación también ofrece la posibilidad de crear componentes utilizando diferentes materiales, lo que permite utilizar aleaciones específicas en diferentes áreas del diseño. Esta es una extensión de las tecnologías existentes, como recubrimientos especializados y revestimientos duros, donde las propiedades optimizadas del material se pueden incorporar al diseño durante el proceso de fabricación, en lugar de como un proceso adicional.
Mejora del diseño de la bomba
En situaciones en las que se requiere un activo de bomba revisado, los operadores pueden aprovechar la última tecnología de diseño y fabricación para entregar una bomba optimizada para la aplicación. El consumo de energía, que es un componente clave en los costos operativos, se puede reducir enfocándose en la eficiencia de la bomba y minimizando todas las posibles pérdidas en el sistema.
Al obtener una comprensión completa de la aplicación, las características del fluido y las demandas de flujo, se puede seleccionar la tecnología de bomba más apropiada que brindará una eficiencia superior. Hacer coincidir la construcción de la bomba con el diseño óptimo del impulsor dará como resultado la solución más rentable, tanto en términos de inversión de capital inicial como de costos operativos a largo plazo.
Se pueden lograr más ganancias mediante el tamaño correcto de la bomba para evitar el desperdicio de energía. Esto puede parecer una afirmación obvia, pero el sobredimensionamiento a menudo ocurre como resultado de la adición de múltiples factores de seguridad a los valores requeridos de altura y flujo. Como resultado, la bomba sobredimensionada no funciona dentro de su curva de eficiencia óptima durante la producción normal.
Uso de datos para optimizar el rendimiento de la bomba
Una vez logrado el mejor diseño posible para una aplicación, es importante mantener el mejor rendimiento y garantizar que el mantenimiento se lleve a cabo en el momento más oportuno. Hoy en día, la analítica avanzada se puede utilizar para capturar y procesar los datos existentes de la bomba para generar ahorros considerables en los costos de operación y mantenimiento.
Al resaltar los activos de bajo rendimiento, es posible implementar una estrategia de mantenimiento proactivo y justificar las recomendaciones de inversión; sincronizarlos cuidadosamente para minimizar la pérdida de producción. El uso de datos sobre rendimiento, confiabilidad y eficiencia permite a los operadores determinar la capacidad del sistema para cumplir con los indicadores clave de rendimiento (KPI).
La mayor disponibilidad de la bomba puede tener un efecto significativo en los ingresos al garantizar que se mantenga mejor la productividad. Se pueden lograr más beneficios mediante la reducción de los gastos de mantenimiento mediante el empleo de recursos cuando se necesitan en lugar de en un horario preestablecido.
Refinando datos sin procesar
Un sistema digital creado por Sulzer, llamado BLUE BOX, utiliza datos de presión, flujo, densidad, viscosidad y consumo de energía. Junto con la información para el departamento de mantenimiento, incluidas las lecturas de vibración y temperatura de los activos, las herramientas analíticas generan visualizaciones casi en tiempo real para las partes interesadas en la gestión y el mantenimiento del sistema.
Los datos se extraen directamente de una variedad de fuentes, como el control de supervisión y la adquisición de datos (SCADA), controladores lógicos programables (PLC), historiadores de procesos, bases de datos, sensores e instrumentación. En este punto, se puede instalar una computadora de grado industrial para procesar los datos, conocido como dispositivo de borde, está equipado con firewalls que brindan una conexión segura a Internet.
Los datos del cliente se procesan en un servidor en la nube mediante un protocolo seguro de transferencia de archivos (SFTP). Utilizando algoritmos probados, los datos se analizan contra curvas de rendimiento conocidas y se muestran en una interfaz personalizada que ofrece al operador el mayor beneficio. Esta solución basada en la nube simplifica el cumplimiento normativo con una huella de TI mínima y está diseñada para ser fácilmente escalable para adaptarse a una amplia gama de operaciones.
Expansores
Al igual que las bombas de alta energía, los expansores son activos de alto valor en los que se confía para un funcionamiento continuo y eficiente. Cualquier tiempo de inactividad tiene consecuencias operativas importantes, por lo que debe reducirse al mínimo. Por lo tanto, mejorar la eficiencia y la confiabilidad, así como reducir las reparaciones no programadas, son objetivos importantes para el equipo de mantenimiento.
Cada expansor contiene un rotor que opera a altas velocidades y presiones de rotación, también puede ser necesario para soportar altas temperaturas y medios corrosivos. Para mantener operativo y confiable un activo tan importante, el uso de datos de rendimiento de la instrumentación de mantenimiento predictivo puede marcar una diferencia decisiva en la disponibilidad y el costo total de propiedad (TCO) durante su vida útil.
Durante los períodos de parada planificados, los informes de inspección detallados pueden resaltar las mejoras de un expansor que mejorarán los costos del ciclo de vida (LCC), la eficiencia del proceso y la productividad. Dependiendo de los hallazgos, se pueden utilizar varias técnicas modernas de mantenimiento y reparación para abordar problemas específicos.
La tecnología de recubrimiento moderna ahora se puede aplicar a equipos heredados que no fueron diseñados para tener en cuenta, por ejemplo, corrientes de gas cargadas de partículas. De esta manera, las superficies originales se pueden restaurar y actualizar para ofrecer una resistencia antiincrustante y a la corrosión muy mejorada.
Eficiencia optimizada
La sección estacionaria de un expansor consta de muchas piezas de precisión que se colocan muy cerca de las piezas giratorias para lograr altos niveles de eficiencia. Algunos de estos componentes se beneficiarán si se actualizan y fabrican a partir de aleaciones robustas, como Hastelloy X, que ofrecen una mayor durabilidad en entornos de alta temperatura.
El grosor de la carcasa en sí se puede aumentar, lo que hace que el componente sea más robusto y menos propenso a la distorsión por calor con el tiempo. Esta mejora a menudo se puede combinar con un revestimiento abrasible en la superficie interior del estator que proporciona un mayor control de holgura con las palas del rotor. Esta área es crucial para optimizar la eficiencia del expansor, ya que las fugas en la punta representan pérdidas sustanciales de eficiencia en los equipos heredados.
Al mismo tiempo, las palas del rotor también se pueden actualizar para aprovechar las aleaciones modernas que están diseñadas para aplicaciones donde se requiere una alta resistencia y buena resistencia a la corrosión a temperaturas de hasta 700 ° C (1'300 ° F). Junto con los segmentos de estator revisados que ofrecen un control dimensional mejorado, es posible implementar una serie de mejoras que aumentan la eficiencia y, por lo tanto, la productividad.
Además de los expansores axiales de gas caliente utilizados en aplicaciones de ácido nítrico y FCC (craqueo catalítico de fluidos), Sulzer también utiliza estas tecnologías de reparación para expansores radiales de flujo utilizados en diversas aplicaciones criogénicas, como la producción de gas natural licuado (GNL), líquidos de gas natural ( Recuperación de LGN), Control del punto de rocío (DPC), Recuperación de etileno y Gases industriales.
Actualizaciones de componentes
Algunos cambios específicos aplicables a los expansores axiales de gas caliente incluyen el reemplazo de los pernos de retención del disco expansor con un grado de acero diferente. Se pueden actualizar varios discos expansores, cuando se mantienen juntos en el rotor mediante un perno que pasa a través de sus centros. El perno original suele estar mecanizado a partir de acero inoxidable 422 y está sometido a un estrés térmico considerable. Este componente se puede actualizar a una aleación de acero inoxidable 450 personalizada que permite un mayor estiramiento de los pernos, lo que resulta en un mayor aplastamiento en el conjunto del rotor.
El mismo principio de actualización se puede aplicar a los cojinetes de soporte del rotor. Al funcionar a velocidades tan altas, es importante que los rodamientos puedan soportar tensiones operativas para brindar confiabilidad a largo plazo. Los cojinetes de manguito cilíndrico se pueden actualizar a cojinetes de almohadilla de inclinación, mientras que los cojinetes con asiento esférico se pueden reemplazar por cojinetes con asiento cilíndrico, que proporcionan un mejor rendimiento y ayudarán a reducir los costos de mantenimiento en el futuro.
Los expansores FCC experimentan con frecuencia desgaste en las palas causado por partículas de catalizador en los gases de combustión. El catalizador tiende a acumular depósitos sólidos en los bordes de ataque y las puntas de las palas, lo que puede causar problemas de vibración y exacerbar el problema. Normalmente, las cuchillas gastadas simplemente se reemplazan; sin embargo, con su experiencia en la reparación de álabes de turbinas de gas (que operan a temperaturas de hasta 1100dgrC), Sulzer puede reducir costos reparando álabes expansores FCC (que normalmente operan a temperaturas más bajas, hasta 700dgrC).
Estas mejoras han sido posibles gracias a nuevos materiales y tecnologías de reparación. Al trabajar con un proveedor de mantenimiento independiente con experiencia, o un OEM equipado de manera similar (Sulzer resulta ser ambos) para evaluar la condición de activos importantes, es posible priorizar cualquier proyecto de actualización y justificar las decisiones de inversión de respaldo. Al aprovechar las nuevas tecnologías, los operadores del sector de los hidrocarburos pueden reducir los costos operativos mejorando la confiabilidad, la eficiencia y el desempeño.
Fuente: Sulzer Ltd.