Éditorial: l’optimisation des pompes et des extenseurs réduit les coûts d’exploitation et prolonge la durée de vie
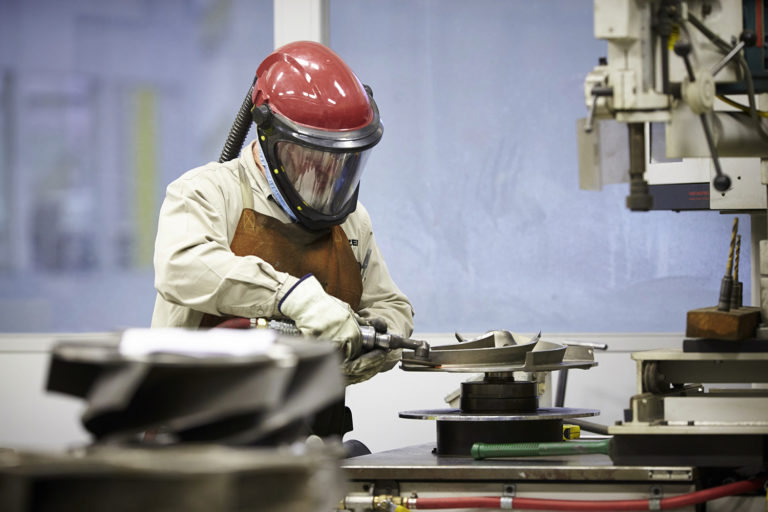
Les modifications de la turbine peuvent améliorer l'efficacité lorsque les applications changent (Source de l'image: Sulzer Ltd.)
Charles Soothill, responsable de la technologie pour la division des services de Sulzer, examine certaines des avancées récentes dans la technologie des équipements rotatifs et comment ils peuvent être mis en œuvre pour améliorer les performances et minimiser les coûts.
Chaque jour, nous utilisons tous des produits de l'industrie des hydrocarbures; le carburant pour se rendre au travail, le gaz pour préparer le dîner ou les plastiques utilisés pour fabriquer des boîtiers pour nos appareils électroniques. Cette industrie est étroitement liée à nos vies et donc toute amélioration qui réduira les coûts d'exploitation profitera en fin de compte à nous, les utilisateurs finaux.
Les pompes à haute énergie et les extenseurs jouent un rôle essentiel dans le secteur des hydrocarbures et chacun a ses propres défis. L'efficacité est essentielle dans les deux applications pour garantir une utilisation optimale de l'énergie, qui est l'un des coûts d'exploitation les plus importants de l'industrie. Avec un fonctionnement continu, les processus nuisibles, tels que l'érosion et la corrosion, pèsent considérablement sur les tolérances des aubes, les joints et les jeux de la roue. Sans intervention en temps opportun, ceux-ci peuvent entraîner des pertes considérables.
Pompes
En règle générale, les grosses pompes sont conçues pour une durée de vie prolongée, cependant, lorsque les performances commencent à se détériorer, c'est souvent le signe que la volute ou la turbine est usée ou corrodée. Ayant, dans de nombreux cas, fourni des décennies de service fiable, trouver de nouvelles pièces peut être un défi qui, même s'il réussit, peut signifier un long délai avant la livraison. Heureusement, les dernières technologies de conception et processus de fabrication peuvent réduire considérablement le temps et les coûts liés à la création de pièces de rechange.
Dans les situations où les fabricants d'équipement d'origine (OEM) sont en mesure de créer des pièces pour des machines héritées, ce service peut avoir un retard car une construction spéciale peut être nécessaire. L'avantage OEM ici est la disponibilité des dessins originaux pour les pièces, cependant, la réaffectation d'un équipement de production à un projet ponctuel peut entraîner des coûts supplémentaires ainsi qu'un retard de livraison, à moins qu'un autre processus ne soit disponible.
Heureusement, la technologie moderne offre une solution qui peut être mise en œuvre à la fois par les OEM, les réparateurs et les fournisseurs de pièces spécialisés. L'avènement de la rétro-ingénierie utilisant des machines de mesure tridimensionnelles sophistiquées, des logiciels de modélisation 3D solide et la numérisation laser permet de recréer des pièces complexes dans des délais courts.
Modernisation et réévaluation des pompes
Les progrès de la technologie de conception ont été accompagnés de développements similaires dans la science des matériaux qui, ensemble, permettent de mettre à niveau les conceptions originales. Les pompes plus anciennes fabriquées avec des matériaux tels que le bronze et la fonte, qui ne peuvent pas être soudés, peuvent voir leur durée de vie prolongée en utilisant de l'acier inoxydable ou d'autres alliages avancés.
Dans de nombreux cas, les conditions de fonctionnement d'origine pour lesquelles la pompe a été conçue auront évolué depuis la première mise en service de la pompe. De tels changements peuvent entraîner une réduction des performances et de l'efficacité, mais ceux-ci peuvent être résolus lors d'une réparation ou d'une révision majeure.
Lors de la création d'une nouvelle roue, la conception hydraulique peut être ré-optimisée en fonction des conditions de fonctionnement - très souvent, cela réduira les besoins énergétiques et entraînera des réductions significatives des coûts d'exploitation. À l'aide des derniers logiciels de conception et de la dynamique des fluides computationnelle (CFD), les composants de rétro-ingénierie peuvent être affinés pour offrir des performances hydrauliques optimales.
Développements de fabrication
Le temps requis pour créer de nouveaux composants pour des actifs de grande valeur tels que les pompes à haute énergie et les extenseurs a été considérablement réduit récemment avec l'avènement des équipements de fabrication hybrides. Des processus tels que le dépôt de métal au laser et le fraisage à cinq axes peuvent être effectués sur une seule machine, ce qui permet une production rapide.
Par exemple, une roue à aubes peut être créée à partir d'un noyau forgé qui est usiné à l'aide de méthodes à 5 axes pour établir la forme de base. Ensuite, un laser fait fondre un flux de poudre et dépose une couche de nouveau métal sur la surface. Cela permet d'accumuler rapidement un grand volume de matériau. La surface dure peut ensuite être usinée aux dimensions finales, le tout sur la même machine.
La flexibilité de cette méthode de fabrication offre également la possibilité de créer des composants en utilisant différents matériaux, ce qui permet d'utiliser des alliages spécifiques dans différents domaines de la conception. Il s'agit d'une extension des technologies existantes telles que les revêtements spécialisés et les revêtements durs où les propriétés optimisées des matériaux peuvent être incorporées dans la conception pendant le processus de fabrication, plutôt que comme un processus supplémentaire.
Amélioration de la conception de la pompe
Dans les situations où un actif de pompe révisé est nécessaire, les opérateurs peuvent tirer parti de toutes les dernières technologies de conception et de fabrication pour fournir une pompe optimisée pour l'application. La consommation d'énergie, qui est un élément clé des coûts d'exploitation, peut être réduite en se concentrant sur l'efficacité de la pompe et en minimisant toutes les pertes possibles dans le système.
En acquérant une compréhension complète de l'application, des caractéristiques du fluide et des demandes de débit, la technologie de pompe la plus appropriée qui offrira une efficacité supérieure peut être sélectionnée. Associer la construction de la pompe à la conception optimale de la turbine aboutira à la solution la plus rentable, à la fois en termes d'investissement initial et de coûts d'exploitation à long terme.
Des gains supplémentaires peuvent être obtenus grâce au dimensionnement correct de la pompe pour éviter le gaspillage d'énergie. Cela peut sembler évident, mais le surdimensionnement se produit souvent en raison de l'ajout de plusieurs facteurs de sécurité aux valeurs de hauteur et de débit requises. En conséquence, la pompe surdimensionnée ne fonctionne pas dans sa courbe d'efficacité optimale pendant la production normale.
Utiliser les données pour optimiser les performances de la pompe
Après avoir réalisé la meilleure conception possible pour une application, il est important de maintenir les meilleures performances et de s'assurer que la maintenance est effectuée au moment le plus opportun. Aujourd'hui, des analyses avancées peuvent être utilisées pour capturer et traiter les données de pompe existantes afin de réaliser des économies considérables en termes de coûts d'exploitation et de maintenance.
En mettant en évidence les actifs sous-performants, il est possible de mettre en œuvre une stratégie de maintenance proactive et de justifier les recommandations d'investissement; chronométrez soigneusement ces derniers pour minimiser la perte de production. L'utilisation de données sur les performances, la fiabilité et l'efficacité permet aux opérateurs de déterminer la capacité du système à répondre aux indicateurs clés de performance (KPI).
Une plus grande disponibilité des pompes peut avoir un effet significatif sur les revenus en assurant un meilleur maintien de la productivité. D'autres avantages peuvent être obtenus grâce à la réduction des dépenses d'entretien en employant des ressources quand elles sont nécessaires plutôt que selon un calendrier prédéfini.
Affiner les données brutes
Un système numérique créé par Sulzer, appelé BLUE BOX, utilise des données de pression, de débit, de densité, de viscosité et de consommation d'énergie. Associés aux informations destinées au service de maintenance, y compris les relevés de vibrations et de température des actifs, les outils d'analyse génèrent des visualisations en temps quasi réel pour les parties prenantes dans la gestion et la maintenance du système.
Les données sont extraites directement de diverses sources telles que le contrôle de supervision et l'acquisition de données (SCADA), les contrôleurs logiques programmables (API), les historiques de processus, les bases de données, les capteurs et l'instrumentation. À ce stade, un ordinateur de qualité industrielle peut être installé pour traiter les données - appelé périphérique de périphérie, il est équipé de pare-feu qui fournissent une connexion sécurisée à Internet.
Les données des clients sont traitées dans un serveur cloud à l'aide d'un protocole de transfert de fichiers sécurisé (SFTP). À l'aide d'algorithmes éprouvés, les données sont analysées par rapport à des courbes de performances connues et affichées dans une interface personnalisée qui offre le plus grand avantage à l'opérateur. Cette solution basée sur le cloud simplifie la conformité réglementaire avec une empreinte informatique minimale et est conçue pour être facilement évolutive pour s'adapter à un large éventail d'opérations.
Expandeurs
Tout comme les pompes à haute énergie, les extenseurs sont des actifs de grande valeur sur lesquels on compte pour un fonctionnement continu et efficace. Tout temps d'arrêt a des conséquences opérationnelles importantes, il doit donc être réduit au strict minimum. Par conséquent, l'amélioration de l'efficacité et de la fiabilité ainsi que la réduction des réparations imprévues sont des objectifs importants pour l'équipe de maintenance.
Chaque détendeur contient un rotor qui fonctionne à des vitesses de rotation et des pressions élevées, il peut également être nécessaire de supporter des températures élevées et des milieux corrosifs. Pour maintenir un actif aussi important opérationnel et fiable, l'utilisation des données de performance provenant de l'instrumentation de maintenance prédictive peut faire une différence décisive en termes de disponibilité et de coût total de possession (TCO) sur sa durée de vie.
Pendant les périodes d'arrêt planifiées, des rapports d'inspection détaillés peuvent mettre en évidence les améliorations apportées à un extenseur qui améliorera les coûts du cycle de vie (LCC), l'efficacité des processus et la productivité. En fonction des résultats, plusieurs techniques modernes de maintenance et de réparation peuvent être utilisées pour résoudre des problèmes spécifiques.
La technologie de revêtement moderne peut maintenant être appliquée à des équipements existants qui n'ont pas été conçus pour prendre en compte les flux de gaz chargés de particules, par exemple. De cette manière, les surfaces d'origine peuvent être restaurées et améliorées pour offrir une résistance anti-salissure et à la corrosion considérablement améliorée.
Efficacité optimisée
La section stationnaire d'un extenseur se compose de nombreuses pièces de précision qui se trouvent à proximité des pièces rotatives pour atteindre des niveaux d'efficacité élevés. Certains de ces composants gagneront à être améliorés et fabriqués à partir d'alliages robustes, tels que Hastelloy X, qui offrent une durabilité améliorée dans des environnements à haute température.
L'épaisseur du boîtier lui-même peut être augmentée, ce qui rend le composant plus robuste et moins sujet à la déformation thermique au fil du temps. Cette amélioration peut souvent être couplée à un revêtement abradable sur la surface intérieure du stator qui fournit un contrôle accru du jeu avec les pales du rotor. Ce domaine est crucial pour optimiser l'efficacité de l'expanseur car les fuites de pointe sont responsables de pertes d'efficacité substantielles dans les équipements existants.
Dans le même temps, les pales du rotor peuvent également être améliorées pour tirer parti des alliages modernes conçus pour les applications nécessitant une résistance élevée et une bonne résistance à la corrosion à des températures allant jusqu'à 700 ° C (1’300 ° F). Avec des segments de stator révisés qui offrent un contrôle dimensionnel amélioré, il est possible de mettre en œuvre une gamme d'améliorations qui augmentent l'efficacité et donc la productivité.
En plus des détendeurs axiaux de gaz chauds utilisés dans les applications d'acide nitrique et de FCC (Fluid Catalytic Cracking), Sulzer utilise également ces technologies de réparation pour les détendeurs radiaux utilisés dans diverses applications cryogéniques telles que la production de gaz naturel liquéfié (GNL), les liquides de gaz naturel ( NGL), contrôle du point de rosée (DPC), récupération de l'éthylène et gaz industriels.
Mises à niveau des composants
Certaines modifications spécifiques applicables aux expanseurs axiaux à gaz chauds incluent le remplacement des boulons de rétention du disque d'expansion par une nuance d'acier différente. Plusieurs disques d'extension, lorsqu'ils sont maintenus ensemble sur le rotor par un boulon qui passe par leurs centres, peuvent être améliorés. Le boulon d'origine est généralement usiné en acier inoxydable 422 et est soumis à une contrainte thermique considérable. Ce composant peut être mis à niveau vers un alliage d'acier inoxydable 450 personnalisé qui permet un allongement accru du boulon, ce qui entraîne un plus grand écrasement du «faisceau» sur l'ensemble du rotor.
Le même principe de mise à niveau peut être appliqué aux roulements de support du rotor. Fonctionnant à des vitesses aussi élevées, il est important que les roulements puissent résister aux contraintes opérationnelles pour offrir une fiabilité à long terme. Les paliers à douille cylindrique peuvent être améliorés en paliers à coussinets inclinables, tandis que les paliers à siège sphérique peuvent être remplacés par des paliers à siège cylindrique, qui offrent de meilleures performances et aideront à réduire les coûts d'entretien à l'avenir.
Les détendeurs FCC subissent fréquemment une usure des pales causée par des particules de catalyseur dans les gaz de combustion. Le catalyseur a tendance à accumuler des dépôts solides sur les bords d'attaque et les pointes des aubes, ce qui peut provoquer des problèmes de vibration et aggraver le problème. En règle générale, les lames usées sont simplement remplacées; Cependant, grâce à son expérience dans la réparation des aubes de turbine à gaz (qui fonctionnent à des températures allant jusqu'à 1100dgrC), Sulzer peut réduire les coûts en réparant les aubes d'expansion FCC (qui fonctionnent généralement à des températures plus basses - jusqu'à 700dgrC).
Ces améliorations ont été rendues possibles grâce à de nouveaux matériaux et technologies de réparation. En travaillant avec un fournisseur de maintenance indépendant expérimenté, ou un OEM équipé de manière similaire (Sulzer se trouve être les deux) pour évaluer l'état des actifs importants, il est possible de hiérarchiser les projets de mise à niveau et de justifier les décisions d'investissement à l'appui. En tirant parti des nouvelles technologies, les opérateurs du secteur des hydrocarbures peuvent réduire leurs coûts d'exploitation grâce à une fiabilité, une efficacité et des performances améliorées.
Source: Sulzer Ltd.