Drehzahlgeregelter Kompressor rechnet sich für Sägewerk in gut drei Jahren
Das Sägewerk Künzel-Holz in Issigau hat seine Druckluftversorgung neu strukturiert: Leitungen wurden getrennt, andere zusammengelegt und zwei neue Kompressoren von Atlas Copco angeschafft. Einer arbeitet drehzahlgeregelt. Mit den Maßnahmen konnte das Unternehmen den Druck in zwei Netzen um jeweils 2 bar senken, ein drittes liefert jetzt den für die Werkstatt erforderlichen Druck von 13 statt 10 bar.
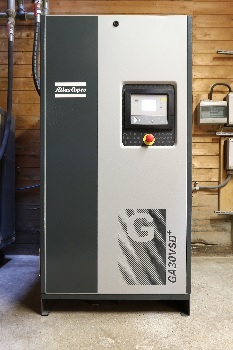
Daneben spart Künzel-Holz durch die modernere Technologie deutlich Energie ein, so dass sich die Investition in spätestens drei Jahren amortisiert.
Es kommt nicht oft vor, dass Atlas-Copco-Kundenberater Özkan Demir bei einer Kaltakquise so offene Türen einrennt wie beim Sägewerk Künzel-Holz im bayerischen Issigau. „Die Druckluftversorgung stand bei uns nicht unbedingt im Fokus, als uns Herr Demir ansprach“, gibt Geschäftsführer Jürgen Künzel zu. „Aber den Vorschlag, die damalige Druckluftsituation kostenlos unter die Lupe zu nehmen, fanden wir gut.“ Der Holzverarbeiter sei modern aufgestellt und neuen Ideen gegenüber grundsätzlich aufgeschlossen. Obwohl Künzel-Holz von der Technik her mit den ‚ganz Großen‘ mithalten könne, arbeite man im Gegensatz zum Wettbewerb mit nur einer Schicht – die im Sommer nach Bedarf verlängert wird. Das genüge an Flexibilität und sichere die Arbeitsplätze.
Das Sägewerk beliefert vor allem langjährige Stammkunden deutschlandweit, wie Zimmereien, Holzhändler, Verpacker oder KVH-Produzenten (KVH = Konstruktionsvollholz). Ein kleinerer Teil des Ausstoßes wird in das benachbarte Tschechien, nach Österreich und Großbritannien exportiert. Etwa 170000 Festmeter Holz werden jährlich geschnitten. „Statt großer Liefermengen setzen wir vor allem auf Qualität und Kundenzufriedenheit“, sagt Jürgen Künzel über die Firmenphilosophie des Familienunternehmens.
Zwei Kompressoren-Stationen versorgten drei Druckluftnetze
Dass die Entscheidungswege in dem mittelständischen Sägewerk grundsätzlich kurz sind, kam auch Özkan Demir entgegen. Schon kurz nach seinem Anruf in Issigau schritt der Atlas-Copco-Berater gemeinsam mit Produktionsleiter Thomas Helmbold die einzelnen Stationen der Druckluftversorgung im Werk ab. Er fand insgesamt drei Druckluftnetze vor, die von zwei Kompressoren-Stationen ausgingen und Hobelhalle, Werkstatt, die Sägelinie und die Lattenfertigung mit jeweiliger Paketierung versorgten.
Insbesondere beim Sägen der Baumstämme wird viel Luft verbraucht, etwa um die Lichtschranken freizublasen. Auch Kettenspanner, Umstapel- und Umreifungsmaschinen benötigen viel Druckluft. Ein Netz verband die Hobelhalle und die Werkstatt und wurde von einem Kompressor gespeist, der mit 11 Kilowatt (kW) Leistung einen Druck von 10 bar lieferte. Für die Hobelhalle mehr als ausreichend, für die Werkstatt zu wenig. „Diese Lösung war ein ständiger Kompromiss, denn die Reifenbefüllung für die zahlreichen Stapler und Bagger auf dem Hof sowie für die Schlagschrauber zum Radwechsel und andere Druckluftwerkzeuge in der Werkstatt brauchten idealerweise einen Fließdruck von bis zu 13 bar. Die Hobelhalle kommt dagegen mit weniger aus“, räumt Thomas Helmbold ein.
Trennung von Hobelhalle und Werkstatt rechnet sich
Özkan Demir schlug vor, das Druckluftnetz in zwei aufzuteilen und einen zusätzlichen Kompressor anzuschaffen. Dieser G7 FF/270 von Atlas Copco versorgt nun die Werkstatt mit 13 bar. Die Kompaktanlage besteht aus dem Kompressor, einem Kältetrockner und einem Druckluftbehälter mit 270 Litern Fassungsvermögen, so dass immer ausreichend Luft zur Verfügung steht. Für die Hobelhalle fiel damit ein Verbraucher weg. „Hier hätten wir mit einem Kompressoraustausch zwar durchaus Energie einsparen können“, sagt der Atlas-Copco-Experte. „Aber das hätte die Investitionskosten nicht gerechtfertigt.“ Wirtschaftlicher sei die neue Lösung dennoch: „Den Druck für die Hobelhalle konnten wir von 10 auf 8 bar reduzieren und haben damit rund 14 Prozent Energie gespart“, freut sich Helmbold. Außerdem laufe der 11-kW-Kompressor jetzt nur bei Bedarf in der Hobelhalle. „Damit konnten wir die Laufzeiten dieser Maschine um 45 Prozent reduzieren“, sagt der Produktionsleiter.
Als nächstes nahmen sich Helmbold und Demir die anderen beiden Netze vor, die von einer gemeinsamen Kompressorstation ausgingen. Drei Kompressoren mit 15 kW, 18,5 kW und 37 kW Leistung und jeweils fester Drehzahl versorgten die großen Druckluftverbraucher im Unternehmen: Der 37- und der 18,5-kW-Kompressor übernahmen die Sägelinie, der 15-kW-Kompressor die Lattenfertigung, nebst Paketierung. „Zunächst haben wir die Lastzeiten des großen 37-kW-Kompressors ausgelesen“, sagt Demir, „und ihm gemeinsam zugehört.“ „Wenn man es weiß, hört man eigentlich direkt, wie er ständig vom Lastbetrieb in den Leerlauf wechselte und zurück – und dass das nicht effizient sein kann“, sagt Helmbold. „Da haben wir auch einiges dazugelernt.“
Zusammenlegung der Säge- und Lattenlinie brachte Einsparpotenzial zutage
Özkan Demir nahm zunächst Messungen an beiden Netzen separat vor. Über einen Bypass ließen diese sich leicht miteinander verbinden, um im Falle eines Kompressorausfalls jeweils das andere Netz zu unterstützen. Nach den Einzelmessungen schaltete er für eine weitere beide Netze zusammen. „Diese gründliche Bestandsaufnahme gehört für uns unbedingt dazu, um für unsere Kunden ein wirklich sinnvolles Angebot erstellen zu können“, betont der Atlas-Copco-Berater. „Wir ermitteln die spezifische Leistungsaufnahme der bestehenden Anlage und simulieren den Einsatz der neuesten Kompressorentypen und Leistungsklassen. Damit ergibt sich fast immer ein Einsparpotenzial. Auf dieser Grundlage können wir errechnen, welche Maschinenkombination am effizientesten ist und sich am schnellsten rechnet.“
Analyse und Simulation ergaben, dass die Auslastung der Kompressoren bei Künzel-Holz alles andere als ideal war. „Hier gab es viel Einsparpotenzial zu heben“, sagt Demir. „Schon das Zusammenfassen beider Netze brachte bei der Messung ein deutlich besseres Ergebnis als die vorgefundene Installation.“ Als Lösung wurden daher beide Netze standardmäßig miteinander verbunden und ein drehzahlgeregelter Schraubenkompressor des Typs GA 30 VSD+ von Atlas Copco angeschafft. „Der ersetzt mit seinen 30 Kilowatt Leistung den bisherigen 37-kW-Kompressor mit fester Drehzahl“, sagt Demir. „Er holt also aus weniger Strom mehr Luft heraus.“ „Der Clou: Die Investition macht sich allein durch die eingesparte Energie in gut drei Jahren bezahlt“, sagt Jürgen Künzel. Ersten Rechnungen zufolge spart das Sägewerk bei den Stromkosten nun etwa 3.400 Euro jährlich ein. Die 37-kW-Maschine eines anderen Herstellers soll nun verkauft werden.
Drehzahlgeregelter Kompressor spart mindestens 3.400 Euro im Jahr
Für die Wirtschaftlichkeit entscheidend sei vor allem die variable Drehzahl des VSD-Kompressors, betont Özkan Demir. VSD heißt „Variable Speed Drive“. „Durch die automatische Regulierung der Motordrehzahl wird die Drucklufterzeugung auf den jeweiligen Bedarf aller ans Netz angeschlossenen Verbraucher angepasst“, erklärt der Atlas-Copco-Vertriebsmann. Durch den einen drehzahlgeregelten Kompressor in der Station, der jetzt beide Netze versorge, würden die Laufzeiten und Lastspiele der anderen beiden Kompressoren deutlich verringert. Sie schalten nur noch bei hohem Bedarf zu. „Mit der neuen GA-VSD+-Baureihe sind im Vergleich zu schlecht ausgelasteten Maschinen mit Volllast-Leerlauf-Regelung Einsparungen von bis zu 50 Prozent möglich“, sagt Demir. Neue Konstruktionsmerkmale wie integrierte Permanentmagnetmotoren und neuartige Verdichtungselemente steigerten die Effizienz im Vergleich zu den Drehzahlregelungen der ersten Generation noch einmal erheblich.
In der Regel stellt der GA 30 VSD+ die Versorgung allein sicher. Bei sehr hohen Lastspitzen kann einer der beiden kleinen Kompressoren die Grundlast übernehmen. Dann liefert der VSD-Kompressor von Atlas Copco die benötigte Differenz. Durch das bessere Anlaufverhalten des Kompressors konnte Künzel-Holz außerdem den Luftdruck für Sägelinie und Lattenfertigung von 10 bar auf etwa 7,8 bar senken. „Wenn man rechnet, dass man pro eingespartem Bar sieben bis acht Prozent Energie gewinnt, ist das sehr okay“, findet Jürgen Künzel.
Umstellung war „beste Investition des Jahres“
„Mittlerweile fallen Energie- und Personalkosten bei der Kalkulation des Holz-Endpreises für unsere Kunden viel mehr ins Gewicht als früher“, sagt Künzel. Der Rohstoffpreis sei nicht mehr allein ausschlaggebend. Er ist in letzter Zeit durch zahlreiche Kalamitäten starken Schwankungen ausgesetzt. Aber die anderen Belastungen und Kosten nehmen zu. Daher ist der Unternehmer froh, dass er die Druckluft für seine Maschinen jetzt viel günstiger erzeugen kann. „Wir hatten uns bisher über die Druckluft keine großen Gedanken gemacht. Die Kompressoren funktionierten ja. Die Wirtschaftlichkeit hatten wir nicht im Blick.“
Wenn man nachrechne, ergebe sich aber schlicht die betriebswirtschaftliche Notwendigkeit, einen Kompressor auszutauschen, auch wenn die alte Maschine technisch noch einwandfrei funktioniere. „Unser Berater von Atlas Copco hat sich viel Arbeit gemacht und sich intensiv gekümmert. Das hat uns davon überzeugt, dass wir Geld verdienen können, wenn wir etwas ändern“, sagt Künzel. Für ihn seien die neuen Kompressoren und die Umstellung der Druckluftversorgung daher „die beste Investition des Jahres“ (2018).
Autorin: Ulrike Preuß, Journalistin in Hennef
Bild: Der drehzahlgeregelte Schraubenkompressor des Typs GA 30 VSD+ von Atlas Copco ersetzt mit seinen 30 kW Leistung den bisherigen 37-kW-Kompressor mit fester Drehzahl. Er holt aus weniger Strom mehr Luft heraus. Künzel spart mit dieser Maßnahme über 3.400 Euro im Jahr. (Foto: Atlas Copco)
Quelle: Atlas Copco Holding GmbH