Dispensing Pumps: Continuous Application of Sealant Beads
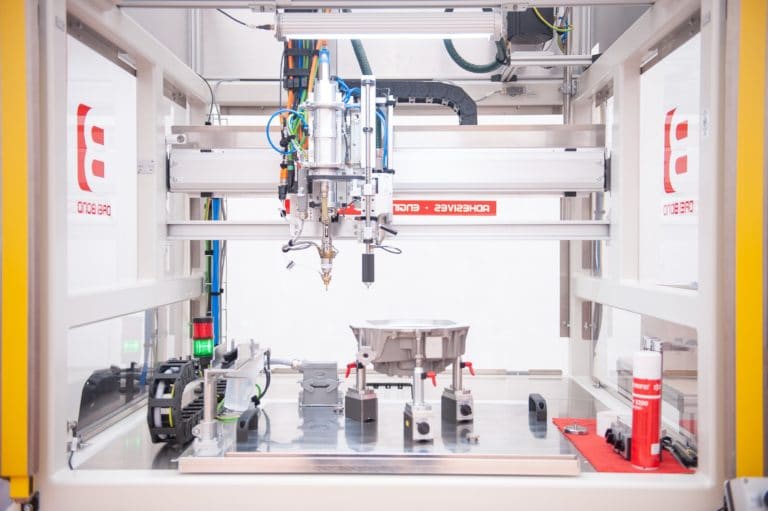
Drei Bond relies on ViscoTec dispensers for high-precision dispensing technology (Image source: ViscoTec Pumpen- u. Dosiertechnik GmbH)
When the system provider, Drei Bond, designs production systems for the volumetric processing of high-performance adhesives and sealants for OEMs, a wide range of dispensing systems such as pressure/time, piston dispensing units, gear pumps or progressive cavity pumps are used. The company has chosen the latter for the technical implementation of a complete cell for dispensing closed sealing beads. The focus: In addition to gentle dispensing, the dosing technology should be easy and not complicated to implement in the existing process. Further requirements: In addition to the exact quantity, sealants and adhesives should be able to be dispensed with particularly low shear rates in order to guarantee the stability of the sealing beads. The pumps, which are installed in the production cells, should also be able to convey continuously.
All in all, these are parameters that speak in favour of using a progressive cavity pump. The dispensing pumps implemented should have little or no influence on the material to be dispensed. The production cells of the system provider Drei Bond are used, among other things, to apply a liquid sealing bead to flat components such as oil pan casings, in a continuous process. Axis systems or robots to which the pumps are attached can be used. The progressive cavity pump technology is also ideal for three-dimensional sealing contours and in the case of more complex casing geometries. Here, the dispensing speed can be variably adapted to the robot's traversing motion during the ongoing process.
Rotor and stator: It all depends on the ingredients
The component is applied by true contour traversing, e.g. using silicones or adhesives between 1 mm and 4 mm thick. The material, which is then precisely dispensed on the component and is now "standing", is pressed flat by pressing an opposite side onto it. Also known colloquially as liquid sealing, this technology is used in the automotive industry, for example, and now replaces the classic paper or rubber seals in many places. For this type of production cell, Drei Bond relies primarily on ViscoTec's progressive cavity pump technology because of the freedom in terms of bead length and profile. For the end customer - e.g. for customers from the automotive sector - maximum flexibility is achieved with regard to the size and type of components to be machined. In the majority of cases, the rotors and stators installed in the pumps, and the sealants or adhesives to be applied, are 100 % compatible. In the event that seldom used materials are to be applied, the companies are in close dialogue and carry out laboratory tests if necessary. This can be the case, for example, if new ingredients are used in the sealants as part of the development of electromobility, which must be tested for compatibility with the rotor and stator. The aim: To ensure that the rotor and stator materials are the best suited for each dispensing material.