Choosing the Right Dewatering Pump
Applications for dewatering pumps vary from clearing floodwater or draining reservoirs, to sewage bypass or ground water dewatering. So, when building a pump portfolio, it’s essential to choose equipment that is versatile, productive, safe and trouble-free.
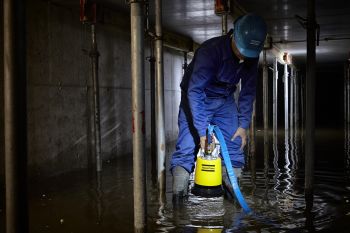
Dewatering pumps should be suitable for use on multiple sites (Image: Atlas Copco)
Here, a pump specialist at a portable energy manufacturer shares the five things he considers most important.
1. Efficiency
When users have to choose a pump, they usually opt for larger sizes on the basis that they can cover a multitude of jobs, but bigger is not always better and by choosing this option, energy efficiency is often sacrificed. Buyers can avoid this by considering new types of technology, rather than simply replicating orders they have always placed in the past.
Developments in technology are helping to reduce fuel usage and operating costs. In recent years, newer types of pump have been introduced that are specifically designed to reduce fuel consumption at times of low load and cope with fluctuating application demands without running up high-fuel costs or risking burnout.
2. Size and movement
Smaller and lighter pumps are now being developed, as well as those that are easier to move and transport both on and between work sites. Consequently, buyers should take time to ensure they select a pump that is suitable for use on multiple sites where the pumps could potentially be working, and that the pump has built-in features that enhance movement and safety. Many larger pumps have integrated trailer options, as well as integrated lifting beams and/or forklift slots. It’s important to find out what options the manufacturer has added to aid the safe movement of the pump from site to site, or within the working location where it is needed.
3. Versatility
Those who work with pumps know that no two jobs are ever the same, so it makes sense to choose a pump that is suitable for multiple applications. It should also be a priority to look closely at the design of the pump’s components and how they work together. So users should consider pumps that come with:
- A range of accessories to enhance performance for changing applications.
- A performance that covers multiple applications and offers different options.
- A modular design that enables upgrades or changes to the existing pump, without the need to replace it with a completely new one.
4. Durability
Pumps need to perform reliably in extreme environments so it’s important that the selected pump has been thoroughly tested and is capable of withstanding tough and changeable working conditions from the moment it is turned on.
In addition, pumps shouldn’t get clogged up. If a pump becomes clogged, then it will reduce the flow of water being pumped. When clogging occurs, it affects performance, and if allowed to continue for an extended period of time, the pump could ultimately burn out.
It’s not very often that users are pumping perfectly clean water, so some elements of clogging are a hazard of the task. To protect against problems, leading manufacturers are continually looking at the positioning of parts and specifically, at the inlet holes and passing areas. Before choosing a pump, users should ask what steps the manufacturer has taken to avoid clogging and so guarantee consistent performance.
5. Ease of service
Anyone in the industry knows that downtime is lost time. When it comes to pumping fluids, any time lost for maintenance and repairs can be catastrophic. So it’s important to choose pumps with a combination of long-service intervals and simple service when one is required. Furthermore, as every second counts in terms of operational time, users should seek pumps that can be serviced in minutes, not hours, with easy access to all parts and consumables. Often, service needs to be completed remotely or at a job site, so the availability and simplicity of a service package is a major consideration.
This is a general overview of some of the key things to look for when considering a pump portfolio or building a rental fleet of pumps. However, when it comes to specific applications, buyers are advised to discuss their needs directly with the manufacturer. With their in-depth knowledge of pump design and use, OEMs will be able to recommend the optimum product based on the maximum head height, required flow and how far the water needs to travel during pumping. They are also ideally positioned to help specify the right type of pump to match the hoses and power source being used. In addition, manufacturers can advise how to address environmental factors such as site accessibility, the size and depth of the pit, type of solids that may be encountered; plus, steps required to meet noise or engine tier regulations. All the above will ensure an end user chooses the right pump for their application, which will ultimately help to increase their productivity.