Automobilzulieferer optimiert Kompressorstation mit Wärmerückgewinnung
In seine neue Kompressorstation hat der Metallbe- und -verarbeiter Prevent TWB in Hagen gleich mehrere Faktoren zur Wärmerückgewinnung eingebaut. Fünf öleingespritzte Schraubenkompressoren von Atlas Copco liefern nicht nur zuverlässig Druckluft an die Verbraucher, sondern heizen Produktionshalle sowie Räumlichkeiten und versorgen gleichzeitig mehrere Prozesse mit heißem Wasser.
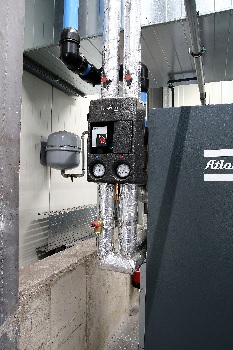
Die Pumpe hält den Kreislauf des zur Wärmerückgewinnung genutzten Kühlwassers in Gang. (Foto: Atlas Copco)
An einem Freitag im November 2016, um 9 Uhr morgens, brennt die Kompressorstation bei Prevent TWB in Hagen. Mitten in der Produktionshalle, oberhalb von Pressen und Schweißmaschinen, wird im Feuerwehreinsatz so schnell wie möglich gelöscht. Doch gegen 11 Uhr steht fest: Es müssen nicht nur ein paar Filter ausgetauscht werden, wie Rüdiger Schmidt, Leiter der Instandhaltung und der Produktion des Presswerks, zunächst gehofft hatte: „Alle Maschinen waren komplett unbrauchbar, ob Kompressoren oder Trockner.“ Der älteste Kompressor, der seit der Installation der Anlage 1996 hier stand, musste ebenso zum Alteisen gegeben werden wie die neueste Anschaffung, ein erst zwei Jahre alter Atlas-Copco-Kompressor. Jetzt galt es, so schnell wie möglich die Druckluftversorgung wieder herzustellen, damit die Produktion weiterlaufen konnte.
Die Prevent TWB stellt in Hagen Bodenplatten, Gitterroste und Schubkarrenmulden her. Vor allem aber Hintersitzlehnen für die Automobilindustrie: Dafür werden Blech-Coils geteilt, die Zuschnitte gepresst, geschweißt und tauchlackiert. Einige Endmontagetätigkeiten nimmt TWB ebenfalls am Standort vor. Polster, Bezüge und Kopfstützen ergänzt der Automobilhersteller selbst. Allein 42000 solche Metallteile nimmt der VW-Konzern pro Woche für seinen modularen Querbaukasten ab.
Druckluftversorgung sollte am selben Tag wieder stehen
Klar, dass bei solchen Abrufmengen regelrecht die Hütte brannte. Schmidt setzte daher sofort alle Hebel in Bewegung, um Druckluft für die Produktion heranzuschaffen. Möglichst noch am selben Tag. Er rief den Kompressorenhändler und Druckluftspezialisten Indrutec an, den Servicepartner, der die Station schon seit etwa zehn Jahren betreut. „Ich wurde aus einem Meeting gerufen, es musste also wirklich dringend sein“, erinnert sich Timo Möller, geschäftsführender Gesellschafter von Indrutec. „Ich fuhr sofort hin. Und Herr Schmidt schickte inzwischen einen 40-Tonner zu meinen Kollegen nach Dortmund, die ihn mit Kompressoren aus unserem Mietpark beluden.“ Binnen kürzester Zeit hatte TWB fünf Ersatzmaschinen mit Leistungen zwischen 55 und 132 Kilowatt (kW) auf dem Hof. „Während die aufgestellt und verrohrt wurden, waren weitere Kollegen mit Kernbohrern dabei, Löcher in die Wände zu bohren, damit wir provisorische Leitungen verlegen konnten“, erinnert sich Rüdiger Schmidt. Abends um 19 Uhr war alles installiert und die Druckluftversorgung zu 90 Prozent für die Noteinspeisung wieder hergestellt.
Noch am selben Tag war allen Beteiligten klar: So konnte die Installation nicht bleiben, und am früheren Standort sollte keine neue Station gebaut werden. Eine komplett neue Druckluftstation musste her, musste geplant und an anderer Stelle auf dem Gelände errichtet werden. „Ein Brand mitten zwischen den Presswerken hätte auch später verheerende Auswirkungen haben können“, erklärt Rüdiger Schmidt. Ohnehin sei die frühere Lösung nicht ideal gewesen, weil die Kompressoren die Luft aus der Umgebung der Produktionsmaschinen angesaugt hatten. Staubpartikel und Ölnebel inklusive. „Auch wenn unsere Prozesse keine ölfreie Druckluft benötigen, so ist der Verschleiß der Kompressoren doch höher, und die Filter setzen sich schneller zu.“
Neue Station mit fünf Kompressoren in eigenem Gebäude
Die Hagener und ihr Druckluftberater überlegten sich etwas völlig Neues. Sie konzipierten eine Station aus fünf neuen Kompressoren, allesamt öleingespritzte GA-Schraubenkompressoren von Atlas Copco mit jeweils 90 kW Leistung, davon zwei drehzahlgeregelte. Diese brachten sie in einem separaten Gebäude unter freiem Himmel unter, im Abstand von etwa 50 Metern zur Produktion auf dem Gelände. TWB baute die ehemalige Maschinenhalle zum Kompressorenraum aus, verlegte auf dem Boden Stahlfliesen aus eigener Produktion und schloss die Produktion über isolierte Leitungen und Kabel an.
Die drei Volllast-Leerlauf-Kompressoren des Typs GA 90 FF laufen nahezu rund um die Uhr, denn das Presswerkt arbeitet im Dreischichtbetrieb an fünf bis sechs Tagen die Woche. Jeweils einer der drehzahlgeregelten Kompressoren – Typ GA 90 VSD FF – wird nach Bedarf über die übergeordnete Steuerung ES 16 zugeschaltet, der andere dient als Redundanz, sollte einmal einer gewartet werden oder ausfallen. In alle Kompressoren ist ein Kältetrockner ab Werk eingebaut, worauf das Kürzel FF (Full Feature) verweist.
„Mit den Atlas-Copco-Kompressoren und dem Service von Indrutec hatten wir in unserer vorherigen Station gute Erfahrungen gemacht“, sagt Schmidt. „Immerhin haben die Kompressoren jahrelang den schlechten Bedingungen ohne unvorhersehbare Ausfälle getrotzt. Und dass sie bei einem Brand versagen, kann man ihnen nun wirklich nicht anlasten.“ Daher wurde die neue Station wieder mit Indrutec und Atlas Copco geplant. Insgesamt habe man jetzt 35 kW mehr zur Verfügung als vorher, um die Laserschweißanlage, Lackiererei und Montage mit Druckluft zu versorgen. Trotzdem sind die monatlichen Stromrechnungen deutlich gesunken.
Wärmerückgewinnung versorgt KTL-Bad und demnächst Teilereinigung
Das liegt einerseits an der Effizienz der neuen Kompressoren und der ausgeklügelten Regelung, vor allem aber auch an der neuen und umfassenden Wärmerückgewinnung, mit der das Unternehmen jedes Grad Celsius an Verdichtungsenergie ausnutzt. So verwenden die Hagener die Wärme des Kompressoren-Kühlwassers einerseits in ihren Prozessen und beheizen andererseits mit der warmen Abluft die Produktionshalle. „Wir hatten schon in der alten Station die Kompressoren mit Systemen zur Wärmerückgewinnung ausgestattet“, erklärt Rüdiger Schmidt, „jetzt nutzen wir die Möglichkeiten noch konsequenter.“
Alle neuen GA-Kompressoren sind mit Systemen zur Wärmerückgewinnung ausgestattet, die Installation war daher sehr einfach. Das auf etwa 85 bis 90 °C erwärmte Kühlwasser verlässt die Kompressoren über isolierte Außenleitungen oberirdisch in Richtung Produktion, um in der Lackieranlage das KTL-Bad (kathodische Tauchlackierung) aufzuheizen. Über Wärmetauscher gibt es einen Teil seiner Energie ab, so dass das Wasser im Rücklauf nach dem KTL-Bad noch etwa 70 °C warm ist. Rüdiger Schmidts Ziel ist es nun, diese Wärme noch weiter zu nutzen, und zwar um Pressteile zu reinigen. Eine Teilewaschanlage soll demnächst angeschafft werden. Dafür wird etwa 50 bis 60 °C heißes Wasser benötigt. Das noch 70 °C warme Kühlwasser könnte hier also noch weitere Energie abgeben. „Vielleicht genug, damit wir das Teilereinigungsbad nicht über eine weitere Wärmequelle beheizen müssen“, hofft Schmidt. „Nach Aufheizung des Teilebads wollen wir das dann lauwarme Wasser den Kompressoren wieder als Kühlwasser zuführen, womit sich hier idealerweise ein Kreislauf schließt“, sagt er.
Hallenheizung mit ausgeklügelter Belüftung durch Kompressoren-Abluft
Für die Beheizung der Halle wiederum nutzen die Hagener die warme Abluft der Kompressoren. Dieses einfache System der Wärmerückgewinnung soll in der kalten Jahreszeit seine Vorteile ausspielen. Die warme Abluft der Kompressoren wird, statt sie nach draußen abzublasen, direkt in die Produktionshalle geleitet. Für diesen Zweck gibt es eine eigene Steuerung, die den Temperaturausgleich regelt. „Wenn die Temperatur im Kompressorraum einen vorgegebenen Wert überschreitet, werden normalerweise Abluftklappen geöffnet, um die erwärmte Luft nach draußen abzublasen. Dann wird nur Frischluft zugeführt. Wird die Temperatur unterschritten, schließen sich die Klappen“, erklärt Rüdiger Schmidt und demonstriert, wie die Lamellen zugehen, sobald er den Sollwert für den Kompressorraum hochsetzt. „Um im Winter die Produktion zu beheizen, wird die Abwärmeluft mit Frischluft gemischt und Richtung Halle geführt.“ Hierzu hat TWB zwei Ventilatoren im Kompressorraum installiert, die insgesamt 40000 Kubikmeter Luft pro Stunde umwälzen können. „Wir profitieren hier sehr von dem neuen Standort mit idealen Ansaugbedingungen, weil wir somit die Halle gleichzeitig heizen und belüften können.“
Airnet-Leitungssystem senkt den Druckverlust
Die Druckluft selbst strömt vom Kompressorraum aus durch Rohrleitungen in die Halle. „Wir verwenden hierfür das Airnet-System von Atlas Copco, 158-Millimeter-Aluminiumrohre, die etwa 180 Meter weit durch die halbe Halle führen. Von der Hauptleitung zweigen 30 Meter lange Leitungen ab, die die Luft an das vorhandene Druckluftnetz und die Verbraucher weitergeben“, erklärt Rüdiger Schmidt. Airnet ist leicht zu installieren, kann nach einer Demontage mit allen Fittings wiederverwendet werden und zeichnet sich durch einen nur sehr geringen Innenwiderstand aus, was den Druckverlust senkt.
Für den Druckausgleich stehen zudem drei Druckluftbehälter in der Produktionshalle, ein 6000-l-Druckluftkessel ist im Kompressorraum untergebracht. „Das Druckband ist sehr stabil und schwankt nur um etwa 0,15 bar“, freut sich Schmidt. Und Druckluftexperte Timo Möller ergänzt nach einem Blick in seine Zahlen, die Auslastung sei relativ gleichmäßig, die Volumenströme lägen bei etwa 1000 Litern pro Sekunde. Jetzt versuche man im nächsten Schritt noch den Druck insgesamt zu reduzieren, weil das neben der Wärmerückgewinnung die meisten Einsparungen bringe. Von derzeit 6,9 bar will man auf etwa 6,5 bar herunterkommen.
Neue Anlage senkt Bedarf an elektrischer Energie um 12 Prozent
Je GA-90-Kompressor könne Prevent TWB 70 kW für die Wärmegewinnung zurückgewinnen, so dass sich insgesamt 350 kW an Wärmeenergie ergeben, rechnet Druckluftexperte Timo Möller vor. 80 bis 90 Prozent davon würden in der Lackieranlage genutzt. Die Wärmerückgewinnung mache die neue Anlage noch wirtschaftlicher, als sie es aufgrund der hocheffizienten GA-Schraubenkompressoren ohnehin schon sei. „Für die Finanzierung der neuen Anlage konnte TWB aufgrund der Energieeffizienz die Maximalförderung der BAFA in Anspruch nehmen“, sagt Möller. „Wir konnten zwar nur mit Schätzwerten operieren, aber Atlas Copco hat uns einen spezifischen Energiebedarf genannt, der auf jeden Fall eingehalten wird.“ Demnach spart die neue Anlage 7600 kWh pro Woche ein – 395000 kWh pro Jahr. Gegenüber der früheren Station, die gut 3,3 Millionen kWh im Jahr verschlang, macht das 12 Prozent aus. Hinzu kommen Einsparungen in Höhe von 2,2 Millionen kWh an Wärmeenergie im Jahr durch die Wärmerückgewinnung, so dass auch die Rechnung des Gasversorgers deutlich niedriger ausfällt. „Wobei man festhalten muss, dass wir auch vorher schon einen Teil der Verdichtungswärme zurückgewonnen und genutzt haben“, schränkt Rüdiger Schmidt ein. Das ändere aber nichts an den großen betriebswirtschaftlichen Vorteilen an sich.
Zentrale Steuerung gibt Energiebericht für ISO-50001-Dokumentation aus
Auch von der neuen übergeordneten Steuerung, die TWB mit den Kompressoren angeschafft hat, versprechen sich die Hagener einiges. Denn die ES 16, ein Energiesparsystem von Atlas Copco, schaltet nicht nur die Kompressoren nach Bedarf zu oder ab, sondern sie misst auch alle relevanten Verbrauchs- und Regelungsdaten und speichert diese für spätere Auswertungen. Der Instandhaltungsleiter kann daher erstmals etwa den täglichen Energiebedarf und andere Leistungsdaten der Kompressoren direkt an seinem PC ablesen. „Über die Smartlink-Software von Atlas Copco schickt mir die Steuerung alle wichtigen Daten auf mein Tablet und meldet auch Ungereimtheiten“, sagt Schmidt. Hierdurch ist er jederzeit über den Status der Druckluftversorgung informiert. Zudem laufen alle Meldungen auch in der Servicezentrale von Indrutec auf, die schnell reagieren können, so dass Ausfälle vermieden werden. „Auch, wenn es am Wochenende Störungen geben sollte, erhalte ich dazu eine Meldung“, lobt Schmidt. „Und am Jahresende ziehe ich mir einen Energiebericht über das gesamte Jahr aus der Software, womit wir unseren Dokumentationspflichten gemäß der ISO 50001 nachkommen und die geforderten Einsparungen auch nachweisen können.“
Brandschutz-Vorkehrungen für den Ernstfall
Als gebranntes Kind hat TWB übrigens Vorkehrungen für den Ernstfall getroffen: In der Station sind zwei externe Rauchmelder angebracht; jeder Kompressor hat zudem seinen eigenen Rauchmelder, und im Brandfall kann die komplette Station lüftungstechnisch von der Produktion getrennt werden. „Vor allem muss die Luftversorgung der Halle unterbrochen werden, damit kein Rauch in die Produktion geleitet wird“, betont Schmidt. Als Reservekompressor steht ein ungeregelter, älterer GA 90 von Atlas Copco im Keller unter der Produktion. Der kann bei einem Ausfall der Druckluftstation erst mal ans Netz gehen, damit die Fertigung nicht komplett ausfällt. Aber dieser Ernstfall dürfte kaum eintreten, schließlich hat TWB mit Atlas Copcos Handelspartner Indrutec einen fünfjährigen, umfassenden Wartungsvertrag abgeschlossen. „Rundum sorglos“ nennt sich diese Vereinbarung. Auch die kann im Zweifel zwar nicht vor einem Brand schützen. Aber sonst deckt sie alles Erwartbare und erwartbar Unerwartbare ab. Und zwar zum Festpreis.
Autorin: Ulrike Preuß, Journalistin in Hennef
Quelle: Atlas Copco Holding GmbH