Atlas Copco Expands its Vacuum Range with DB Side Channel Blowers
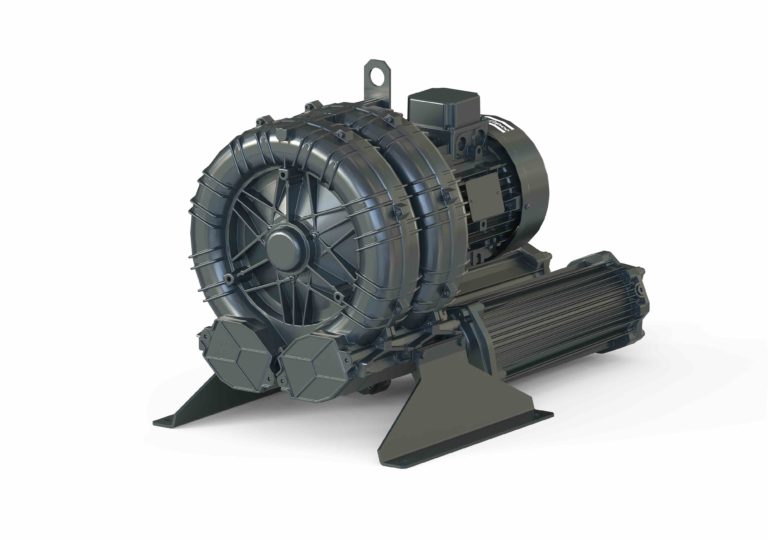
DBt - Twin impellers and single stage. (Image source: Atlas Copco AB)
The impellers are connected to the motor shaft and enable suction of the pumped medium, which is accelerated in the side channel.
Suitable for rough processes
Side channel blowers are designed for applications where high flow rates are required. This makes the dry rough vacuum of the DB models suitable for rough industrial processes - such as drying, pneumatic conveying or suction processes. The modular design ensures high efficiency, reliable performance and quiet operation.
No emissions or contamination
Thanks to the dry, non-contact pumping principle, the exhaust air of the DB vacuum pumps cannot be contaminated; the vacuum is completely free of oil and dust, without any emissions or impurities. The models are equipped as standard with IE3 motors in eco-design and comply with cURus standards. This certification meets all safety requirements for the Canadian and American markets.
Optional single- or two-stage design
Depending on the required vacuum performance, Atlas Copco offers the DB series in single-stage and two-stage versions, optionally with one impeller or twin impellers each. The single-stage version release the pumped medium after it has gone through just one stage, while in the two-stage version it enters the second stage after the first one. Operation with twin impellers increases the blower's capacity. The two-stage version achieves a higher vacuum level. The combination of both results in larger air flows and higher vacuum level with just one machine.
Regular maintenance reduces operating costs
Atlas Copco takes care of maintenance planning and regular servicing of the DB pumps, if required. "Our 'Preventive Care Plan' is tailored exactly to the pump's needs. Since the vacuum pumps are maintained using state-of-the-art technologies, we also achieve a high level of energy efficiency as a result," Carol Pignatelli, the responsible product manager at Atlas Copco, emphasises. Thus, regular maintenance ultimately helps to reduce operating costs and increase process productivity by minimising unplanned downtime.
The advantages of the DB series at a glance
- Non-contact, oil-free operating principle prevents oil and dust contamination
- Suitable for global installations
- Wide range of voltages and frequencies available from 50 and 60 Hz
- Housed in closed aluminium enclosure
- Virtually maintenance free
- Low noise thanks to effective blade design.
Source: Atlas Copco AB