Aqueous Washing Machines Are Highly Controllable and Compact
Concentric, a company focusing on the development and manufacture of oil, water and fuel pumps used in diesel engines for heavy vehicles and off-road plant, has invested in three Mafac Elba aqueous cleaning machines from Turbex.
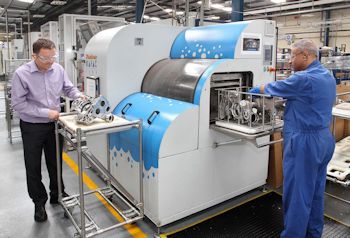
Aluminium pump housings entering the Turbex machine for cleaning. Mark McFall is pictured left inspecting a previously cleaned component.
It is in response to a sharp upturn in business, which has led to a rise in the number of pump housings and other components being machined at the firm’s factory in Erdington, Birmingham. All of the components need to be washed to remove swarf and cutting oil residue.
Mark McFall, Manufacturing Engineering Manager, said, “Our pump housings in particular tend to have complicated shapes, so swarf becomes trapped and can be difficult to remove.
“We operate around two dozen older washing machines, some of which have limited controllability when programming the movement of water jets that spray machined parts in the rotating basket. In other machines, the water jets are not able to move at all.
So we have to extend the length of the washing cycles to ensure efficient cleaning and make sure that there are no problems during subsequent pump assembly. This time we opted for Turbex machines due to the more efficient cleaning action, which can be programmed to suit exactly the type of component being processed. Cycles are therefore shorter to achieve a similar level of cleanliness.”
A further advantage of the machines is that they have a small footprint for their capacity, which is important to Concentric Birmingham as space is limited on the shop floor.
The generous size of the Turbex process chamber allows two recently-introduced large pump housings to be fixtured in a basket side by side for cleaning. It would be feasible to clean only one such component in the other types of machine unless larger, more space-hungry and costlier models had been purchased. Likewise, a larger number of smaller components can be processed in a single batch in the Turbex machines.
The reason behind the high degree of controllability is the patented design whereby the holding basket and spray jets, which are individually adjustable, rotate in either the same direction or opposite directions. Each program can be tailored, including other movement options such as rotation or oscillation of the basket, to clean efficiently even the most complex parts. Another notable advantage of the machines is that they have integral condensing systems, so there is no need to fit extraction equipment.
Pre-order trials carried out at the Turbex technical centre and showroom in Alton confirmed that the machines were indeed capable of processing aluminium pump bodies in shorter cycle times to the required degree of cleanliness. All three machines were installed at the Erdington factory during the course of 2013.
One supports oil pump manufacture and is installed in a cell with two Fanuc Robodrills. The other two Turbex machines are in the water pump production area, each of which cleans machined housings produced from aluminium castings in a number of DMG Mori machining centres. The wash and air-blast drying cycle in the Turbex machines is programmed to take less than four minutes, within Concentric Birmingham’s TAKT time for pump manufacture.
Source: Turbex Ltd