AODD Pump by Triark Pumps Supports Foam Concrete Application
Triark Pumps was approached by a national concrete supply company with a rather challenging landfill application. They had been called in to fill and make safe a large hole that had appeared in an established and otherwise stable landfill site.
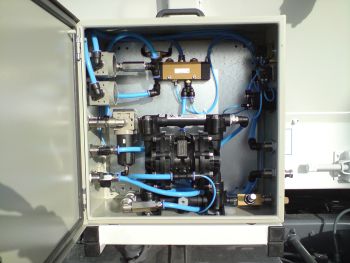
Triark Pumps
The dilemma however, was that in landfill and similar concrete pours, where the ground is susceptible to subsidence, the density and overall weight of the concrete being used can often compound the problem rather than provide the required infill solution.
In these types of applications, where there is the potential for further sinking and settlement, there is a need to keep the weight of the material being used to a minimum, whilst ensuring its overall integrity is maintained. The initial idea was to use a combination of both Celcon blocks (the lightweight industry standard building block) and concrete, but the numerous air locks and cavities this approach created could, in its self, harbour potential stability problems.
Triark’s engineers came up with a simple, yet novel solution.
By using an AODD pump at its heart, they designed a pneumatic foam generator that was able to produce the same sort of foam that Celcon use in the factory production of their building blocks, but in a more liquid form to aid remote onsite pouring. The equipment was small enough to be mounted on a standard concrete mixer, allowing the plant to arrive on site half full, with just 3m³ of concreate on board rather than the usual 6m³. The concrete would then be topped up with the foam, allowing the resulting lightweight foam concrete to be poured directly into the designated cavity. Through successful trials and testing, Triark Pumps were able to produce a foam mixture which allowed the concrete mixers to carry just 2.5m³ of concrete on to the site.
The customer was extremely pleased with the results, claiming exponential savings on more traditional concrete pours and as a direct result placed an order for a further five units.
The Production Process
Foamed Concrete is a lightweight, free flowing material, which is ideal for a wide range of applications. It is made by adding special foam to cement mortar slurry. This foam is made from a foaming agent, a highly concentrated, highly efficient, low dosage liquid.
Appropriate volumes of water and the foaming agent are drawn separately into the Foam Generator, via the integral AODD Pump, which mixes them in the correct ratio (see diagram below) to produce the pre-foaming solution.
This pre-foaming solution along with compressed air is then forced at high pressure through a lance, to produce uniform, stable foam which has a volume of 20-25 times that of the pre-foamed solution. The foam is then mixed into the mortar slurry in a suitable cement mixer to make the lightweight foamed concrete.
An automatic timer is built into the Foam Generator enabling easy production of identical consecutive batches. Totally safe, and with no electrical parts the Foam Generator is entirely air operated, and so is ideally suited to all manner of environments and remote locations.
Foam Generator - Key Features
- Produce good quality, consistent foam
- Require a compressed air supply to work - no electrical supply is needed
- Easily portable - hand-held versions can be carried or transported in a car
- They are small, light and durable
- Expansion rate of the pre-foaming solution can be adjusted if required
Foamed Concrete – Main Attributes
- No compaction or vibration needed
- Free flowing, spreads to fill all voids
- Non-hazardous
- Reliable quality control
- Properties can be varied to suit needs
- Highly cost effective
- Can be pumped
- Lightweight, reduces direct loading
- Excellent load spreading characteristics
- No maintenance required
- Excellent sound and thermal insulation
- Excellent resistance to freeze-thaw
- Does not impose lateral loads
- Low water absorption over time
- Excellent fire resistant property
Foamed Concreate – Applications
- Trench Reinstatement
- Bridge Abutment
- Void Filling
- Roof Structures
- Roofing Insulation
- Road Structures
Foamed Concrete can be placed easily, by pumping if necessary, and does not require compaction or levelling. It has excellent water and frost resistance and provides a high level of both sound and thermal insulation. The concrete formed is extremely stable and lightweight, and will not sink into soft ground or impose undue loading on roofs and other structures. It is uniquely versatile and with its huge range of dry densities and strengths, it can be tailored for optimum performance and minimum cost by choice of a suitable mix configuration.
Source: Triark Pumps Ltd