10 Signs It’s Time to Upgrade Your Compressed Air Piping System
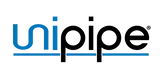
Image source: Unipipe Solutions
How Long Does Compressed Air Piping Last?
The service life of a compressed air piping system can vary widely based on several factors, including the material of the pipes, the quality of the installation, the operating conditions, and the maintenance practices. Generally, here’s what you can expect for different types of materials.
- Black iron or galvanized steel: Typically, these pipes can last anywhere from 15 to 20 years under normal operating conditions. However, they are prone to corrosion, which can significantly shorten their lifespan, especially if moisture is present in the compressed air. Galvanized steel will last a bit longer than black iron or mild steel, but it is also prone to corrosion as the zinc layer wears away.
- Stainless steel: Stainless steel piping can last 50 years or more under normal operating conditions. Its longevity is primarily due to its high strength and corrosion resistance. However, these systems are very expensive to install, making them relatively rare in the compressed air world.
- Copper: Known for its corrosion resistance and high durability, copper piping can last 20 to 50 years. The exact lifespan will depend on the environment, installation and maintenance practices. Copper is prone to pitting when exposed to certain chemicals and can become brittle under certain kinds of tensile stress, leading to potential cracking. Joints and fittings can fail earlier than the overall piping system itself, leading to excessive leaks.
- Plastic: While plastic pipe is sometimes used for compressed air delivery, its use is not recommended due to safety and longevity concerns. (Note: PVC, CPVC, and PEX should never be used for compressed air delivery.) Over time, plastic tends to become brittle, leading to a risk of bursting or shattering at high pressures. Plastic is also vulnerable to damage from chemicals and lubricants in compressed air or the external environment. A plastic pipe system rated for compressed air may last anywhere from 10-20 years with proper care, but it should be inspected regularly for signs of early failure.
- Aluminum: Modern aluminum piping systems are designed for longevity and typically last 30 to 50 years or more. Aluminum is highly resistant to corrosion, lightweight and easy to install, making it a preferred choice for many contemporary compressed air systems.
When Is It Time to Upgrade?
Compressed air distribution systems, like all mechanical systems, are subject to wear and tear over time. If problems with the piping system go unaddressed, this will lead to increased costs and reduced efficiency for the system. If you are seeing any of these signs, it may be time to evaluate your distribution system and consider a replacement.
1. Excessive Pressure Drop
A noticeable drop in pressure can indicate blockages or restrictions within the piping, leading to inefficiency and increased energy consumption. If the pressure drop is consistent, it might be due to an undersized piping network that cannot handle your current requirements. Pressure drop may also be caused by corrosion or other blockages within the lines.
2. High Leak Rate
Frequent leaks not only waste valuable compressed air but also lead to higher energy bills. Regularly detecting and fixing leaks can be costly and time-consuming. If you find yourself constantly repairing leaks, it’s a clear sign that your system needs an overhaul.
3. Visible Corrosion
Rust and corrosion weaken the piping structure, leading to potential failures and leaks. Corrosion is especially common in older iron piping systems and can severely impact air quality. If you are seeing corrosion or pitting on the outside of the pipes, or if you can see corrosion buildup inside pipes during inspection or repair, consider a replacement.
4. Blocked Filters
If you find yourself replacing inline filters more often, it may be a sign that you have internal corrosion or flaking in your compressed air pipes. Rust particles or flaking from iron or galvanized steel pipes will quickly foul inline point of use filters, reducing energy efficiency and driving up operating costs.
5. Contamination in Air Supply
Corrosion inside the piping system, in addition to restricting airflow, will cause contamination in the air stream. Poor air quality can affect the performance of pneumatic tools and equipment, leading to higher maintenance costs. It also can lead to product quality issues. Contamination originating inside the piping system itself can be difficult to control if it enters the airstream after the inline filters.
6. Inefficient System Design
Older compressed air piping systems have often undergone several rounds of changes and additions, resulting in a rats’ nest of piping throughout the facility. Long pipe runs, dead ends, and poorly placed or designed drops can all sap system efficiency. Often, you’ll notice excess pressure drop at the end of long runs or inconsistent pressure at different points in the system. Sometimes these issues can be corrected, but often the best solution is to start over with a modern loop-style system that efficiently transports air to all the places it needs to go.
7. Undersized Piping
As your business grows, your compressed air needs may increase. Older piping systems designed for lower compressed air capacity may not be sized adequately for the increased airflow. Undersized pipes lead to excess pressure drop and system inefficiencies. If your current system can’t keep up with demand, it’s time to consider an upgrade.
8. Safety Concerns
Cracks, leaks or bursts in compressed piping can pose serious safety risks to your employees. Look for signs of excess stress or wear on pipes that could indicate a potential failure. Be especially cautious of older plastic piping systems. If the piping is made out of PVC or another material not approved for use in compressed air distribution, the system is out of compliance with OSHA regulations and should be replaced immediately. Ensuring the safety of your compressed air system is crucial to preventing accidents and maintaining a safe workplace.
9. High Energy Costs
If you notice that your energy bills are consistently rising without a corresponding increase in production, it might be due to an inefficient compressed air system. Older systems can consume more energy due to leaks, pressure drops and other inefficiencies. Upgrading to a more modern and efficient system can significantly reduce energy consumption and lower your operating costs.
10. Frequent Repairs
When maintenance and repair costs are mounting, and you find yourself constantly fixing the same issues, it’s a strong indicator that the system is nearing the end of its useful life. Frequent repairs not only increase downtime but also add up in terms of labor and replacement parts.
The ROI of a New Aluminum Compressed Air Piping System
When it’s time to upgrade, consider the benefits of aluminum piping systems. Aluminum pipes are lightweight, resistant to corrosion and easy to install, making them an ideal choice for modern compressed air systems. They offer superior flow characteristics, reducing pressure drops and energy consumption. Aluminum systems also ensure high air quality, free from rust and contaminants, which helps maintain the integrity of your tools and machinery. The Unipipe® aluminum piping system features fittings with an innovative grip-ring for fast, easy installation and a secure, leak-free connection that holds up well over time. A high quality aluminum piping system can provide trouble-free performance for decades to come.
Upgrading to an aluminum piping system can lead to long-term savings, enhanced efficiency and improved overall performance of your compressed air system. It’s an investment that will quickly pay for itself through reduced energy costs and improved system performance.
Source: Unipipe Solutions