Qualität der Auslegungsdaten bestimmt Effizienz und Verfügbarkeit
Wie auf jeder ACHEMA, werden auch vom 15. bis 19. Mai 2006 die Hersteller von Pumpen, Armaturen und Dichtungen das zahlenmäßig bedeutendste Aussteller-Kontingent aufbieten. Das sind rund 850 der insgesamt 4.000 Aussteller. Und wie immer werden die Besucher den Herstellern vor allem eine zentrale Frage stellen: ...
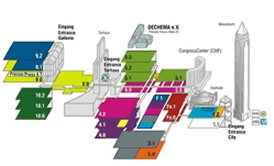
... Wie können wir als Betreiber einer verfahrenstechnischen Anlage die Stoffströme sicher und emissionsfrei fördern und lenken? Und vor allem: Wie ist diese Aufgabe am kostengünstigsten lösbar? Es werden annähernd 200.000 Besucher aus 100 Ländern erwartet, davon 40.000 aus der Entscheiderebene.
Das ist natürlich ein Extremfall: Der Pumpenhersteller KSB fertigt seine bisher größten Kühlwasserpumpen für das neue Kohlekraftwerk Yuhuan in China – jedes der acht 130-Tonnen- Aggregate fördert pro Sekunde bis zu 16.000 Liter Kühlwasser und holt sich zum Antrieb 4,6 MW Leistung aus dem Netz. Aber auch kleinere Industriepumpen benötigen eine Menge an Energie. Wer dies bislang nicht so recht wahrgenommen hat oder nicht wahrnehmen wollte, der wird mittlerweile durch die erheblichen Kostensteigerungen unsanft damit konfrontiert.
Der Strompreis für industrielle und gewerbliche Kunden stieg in Deutschland seit 2002 (trotz Liberalisierung) kräftig im hohen zweistelligen Bereich. Auch EU-weit kostet Strom immer mehr. Bei neuen Pumpensystemen schauen Betreiber deshalb stärker als zuvor auf den Gesamt-Wirkungsgrad von Pumpe und Motor.
Und auch bei Altsystemen lohnt der genaue Blick auf die Pumpe und deren Arbeitsumgebung, um die Kostensteigerungen beim Strom zu egalisieren: Der VDMA-Fachverband Pumpen + Systeme hält Energieeinsparpotentiale von 20 bis 30 % für möglich. Daher hat der Fachverband gemeinsam mit der Deutschen Energie Agentur (dena) die Kampagne ‚System- Effizienz’ initiiert.
Unter Beteiligung von Industriepartnern, darunter die Pumpenhersteller Grundfos, KSB, Sulzer und Wilo, wurde eine Struktur aufgebaut, um industriellen und gewerblichen Betreibern dabei zu helfen, ihre Pumpensysteme hinsichtlich des Energieverbrauchs zu analysieren und zu optimieren. Neben einem breiten Informationsangebot, das auf die Lifecycle- Kosten eingeht und zahlreiche Faktenblätter umfasst, werden Maßnahmenkataloge für Energieeinsparmaßnahmen erarbeitet und deren Wirtschaftlichkeit nachgewiesen. Auf der ACHEMA 2006 vom 15. bis 19. Mai in Frankfurt am Main werden die Pumpen-Hersteller darüber hinausgehende Ansätze und praxisgerechte Lösungen zum energiesparenden Betrieb von Industriepumpen aufzeigen.
Verfügbarkeit sicher stellen
Energie zu sparen ist wichtig. Doch müssen Pumpen und alle anderen ‚Hilfsaggregate’ für den Betrieb einer verfahrenstechnischen Anlage vor allem eines: Laufen, laufen, laufen. Aus Sicht des Betriebsingenieurs ist deren Verfügbarkeit entscheidend, dann erst schaut er auf andere Parameter.
Wie aber können Hersteller und Betreiber den Betrieb von solchen Aggregaten gegen Ausfälle unterschiedlicher Art absichern? Redundanz lautet eine der möglichen Antworten, also beispielsweise einfach eine Reservepumpe beistellen. Heute wird das vielfach eleganter gelöst: durch den verstärkten Einsatz von Elektronik und Sensorik. Denn bei mechanisch bewegten Teilen wird es immer Verschleiß geben, egal wie gut und langlebig einzelne Komponenten auch ausgeführt werden. Wichtig ist es deshalb, dem Verschleiß früh genug auf die Spur zu kommen.
Und: Der Betreiber muss die prozess- und anlagebedingten Anforderungen möglichst früh mit dem Lieferanten diskutieren. Denn nur so können die daraus resultierenden Belastungen und Beanspruchungen für die Pumpe vom Hersteller berücksichtigt werden.
Es ist immer besser, kritische Betriebszustände durch gute Planung des ganzen Pumpensystems grundsätzlich zu vermeiden, und das ist auf jeden Fall besser als in einem ‚schlechten’ System Störungen immer nur rechtzeitig anzuzeigen. Denn dies zeigt die Praxis ja immer wieder: ‚Bad actors’ sind schlicht und ergreifend meist zu groß dimensionierte Pumpen. Dem wird grundsätzlich natürlich niemand widersprechen – wohl wissend, dass in der Praxis ‚gute Planung’ gar nicht so einfach zu realisieren ist, wenn grundlegende Daten zum Medium und zum Prozess zum Zeitpunkt der Pumpenauslegung noch nicht verfügbar sind.
Übrigens sollte eine Kreiselpumpe nicht nur unter energetischen Gesichtspunkten im oder nahe am Betriebspunkt arbeiten. Auch unter mechanischen Aspekten ist das von Bedeutung, denn weitab vom Betriebspunkt treten plötzlich Radialkräfte an den Lagern und Gleitringdichtungen auf und belasten diese. Auch kommt es verstärkt zu Kavitationserscheinungen. Deshalb:
Keine Sicherheitszuschläge bei der Auslegung einer Pumpe!
Ist eine Pumpe korrekt ausgelegt, wird sie nur durch untypische Früh- und Zufallsausfälle oder aufgrund unzulässiger Betriebweise ausfallen. Eine weitere Ausfallursache stellt das Erreichen der Grenzen des normalen Verschleißes, d. h. der Lebensdauer dar.
Überwachung und Störungsfrüherkennung
Das ist wohl der Wunsch aller Betriebsingenieure und Instandhalter: Störungen am technischen Equipment frühzeitig zu erkennen, bevor die Verfügbarkeit beeinträchtigt wird. Kurz gesagt, man will agieren, nicht reagieren. Das stetig wachsende Angebot auf dem Markt reicht von Schwingungs-, Druck-, Temperatur- und Körperschallsensoren (mit den zugehörigen Auswertegeräten), über Diagnosesysteme für Gleitringdichtungen und Lager bis hin zur Selbstüberwachung der Steuereinrichtungen.
Klassische Sensoren erfassen je einen Messwert und signalisieren dann etwas, was kein Betreiber sehen möchte: Eine Störmeldung nämlich. Die Störungsfrüherkennung tritt zuvor in Aktion, signalisiert ein Problem vor dem Ausfall der Pumpe bzw. vor Eintritt einer Schädigung. Bei den großen Pumpen bieten sich leistungsfähige Überwachungseinrichtungen an, die auf der Basis von Schwingungsanalysen, der Auswertung von Strom- und Spannungsschwankungen und Veränderungen bei den Prozessparametern (Temperatur, Druck, Förderstrom) frühzeitig und auch recht zuverlässig sich anbahnende Störungen aufgrund eines nicht bestimmungsgemäßen Betriebs bzw. aufgrund von Verschleiß erkennen.
Aber: Man legt niemanden auf die Intensivstation, nur weil er vielleicht einen Schnupfen bekommen könnte. Der Aufwand einer Überwachung muss in Relation zum Risiko und auch zum Wert der Pumpe stehen. Nicht alle Pumpen sind gleich wichtig; da darf schon mal ein weniger wichtiges Aggregat ungeplant ausfallen. Beim Rest, bei den prozessrelevanten Pumpen, sollte zunächst eine Bauteilüberwachung erfolgen – also eine Überwachung von Membranen, Ventilen, Spalttöpfen, Lagern. Erst im weiteren Schritt sei eine intelligente Störungsfrüherkennung sinnvoll, raten Fachleute.
Dabei ist es gefestigte Erkenntnis, dass Störungen bei rotierenden Teilen recht zuverlässig über den Körperschall detektierbar sind. Die dafür erforderlichen Sensoren sind – vom finanziellen Aufwand einmal abgesehen - kein Problem mehr. Entscheidend ist jedoch die Merkmals- Extraktion. Soll heißen: Wie und woran erkennt der Betreiber eine Störung? Ziel ist es, aus Körperschallanalysen jedem Fehler eine eindeutige Frequenz zuordnen zu können. Beispielsweise zur Überwachung der funktionsbestimmenden Bauteile des Pumpenkopfes oszillierender Membranpumpen funktioniert das bereits: Ein solches Condition Monitoring System erkennt den Großteil der möglichen Störungen, beispielsweise eine Lekkage der Fluidventile (ein sehr sensibles System durch zeitliche Zuordnung des Körperschallsignals zu Saug- und Druckhub). Es werden Leckagen ab 1 % zuverlässig erkannt. Durch die kombinierte Auswertung von Körperschall- und Drucksignalen werden 90 % der möglichen Störungen überwacht, so der Anbieter.
Was man beim Pro und Contra des Einsatzes einer intelligenten Störungsfrüherkennung hinsichtlich der Kostenüberlegungen auch beachten sollte: Überwachung verlängert auch immer die Serviceintervalle – schon deshalb ‚rechnet’ sich ein solches System meist in überschaubarer Zeit. Die oft geäußerte Aussage, ein Überwachungssystem dürfe maximal 10 % der Pumpe kosten, ist kritisch zu hinterfragen. Es kommt darauf an, welchen Wert die Verfügbarkeit der Anlage für den Kunden hat – nicht was die Überwachung in Bezug auf die Pumpe kostet.
Redundanz: B-Pumpen in der Diskussion
Aus Verfügbarkeitsgründen sind in der Chemie viele Pumpen redundant installiert (A- und B-Pumpen). Die dafür erforderlichen Mehrkosten führen jedoch zwangsläufig zur Frage: Wo und unter welchen Bedingungen kann der Betreiber auf den Einsatz redundanter Pumpen verzichten? Die Antwort darauf ist nicht einfach. Bei einer Entscheidung gegen die B-Pumpe sind insbesondere bei kontinuierlichem Betrieb der Anlage die Kosten eines An- und Abfahrens sowie gegebenenfalls der entstehende Produktionsausfall infolge einer Betriebsstörung zu den Mehrkosten für die Reservepumpe ins Verhältnis zu setzen.
Soll auf die redundante Pumpe verzichtet werden, stehen Betreiber und Lieferant gleichermaßen unter einem hohen Verantwortungsdruck. Nicht nur die Produktqualität muss dann höheren Standards entsprechen, auch die Auslegung der Pumpe muss wesentlich präziser sein; zudem ist eine geeignete messtechnische Überwachung und Störungsfrüherkennung (siehe oben) unverzichtbar. Praktiker raten, auf jeden Fall die zu erwartenden Prozessabläufe bei der Inbetriebnahme gezielt abzufahren – so könne überprüft werden, ob die Pumpe korrekt ausgelegt wurde. Das Verifizieren der Prozessfähigkeit bei der Inbetriebnahme der Pumpe gibt dem Betreiber die Chance zur Aufrüstung der Pumpe und dem Pumpenhersteller die Chance zur Nachbesserung.
Insbesondere bei großen Pumpen mit hohem Investitionswert und langen Lieferzeiten kommt der Qualitätssicherung eine große Bedeutung zu. Bezüglich der Qualität kann man zwischen der Qualität der Pumpe selbst, der Qualität der Prozessdaten und der Qualität der Maschinendiagnose/ Störungsfrüherkennung unterscheiden. Die Verfahrens- und Auslegungsdaten müssen reproduzierbar und innerhalb der Anlage abgesichert sein, um einen störungsfreien Betrieb der Pumpe gewährleisten zu können.
Hierbei muss ein besonderes Augenmerk auf den Fertigungsprozess des Pumpengehäuses innerhalb der Gießerei bzw. Schmiede gelegt werden. Nicht wenige Betreiber beklagen übrigens speziell beim Guss einen merklichen Qualitätsverlust – das Auslagern der Gussherstellung in Billiglohnländer war und ist offenbar nicht immer mit einer entsprechenden Qualifizierung des neuen Gusslieferanten begleitet worden. Tribut an die Globalisierung? Hier müssen die betroffenen Hersteller rasch reagieren.
Wellendichtungslose Pumpen: Ein 200-Millionen-Euro-Markt
Potentiell umweltgefährdende und / oder gefährliche Medien kann der Betreiber nur dann sicher und vor allem emissionsfrei fördern, wenn er entweder Pumpen mit aufwändig gestalteten Gleitringdichtungen oder wellendichtungslose Aggregate, also mit Magnetkupplung oder Spaltrohrmotor einsetzt.
Um Leckagefreiheit sicher zu stellen, hat der Betreiber die folgenden Möglichkeiten:
- Hermetische Pumpen mit Spaltrohrmotorantrieb (absolute Dichtheit dank doppelter
Dichthülle, kein Sperrmedium erforderlich)
- Magnetkupplungspumpen (einfache Dichthülle, Sekundär-GLRD muss überwacht werden;
Wiederaufbereitung von Sperrgas zwingend erforderlich)
- Mehrfach-GLRD-Pumpen mit Sperrmedium (Wiederaufbereitung der Sperrflüssigkeit
zwingend erforderlich)
- Mehrfach-GLRD-Pumpen mit trockenlaufender Dichtung (Wiederaufbereitung von Sperrgas
zwingend erforderlich)
Der entscheidende Unterschied zwischen Spaltrohrmotor und Magnetantrieb besteht darin, dass der Spaltrohrmotor eine zweite, zur Atmosphäre hin dichte Sicherheitshülle besitzt. Auch der Klemmenkasten und die Kabeldurchführungen sind gas- und flüssigkeitsdicht ausgeführt und auf den Nenndruck des Aggregates ausgelegt. Im Falle einer Zerstörung des Spaltrohres, etwa durch Lagerschaden oder Korrosion, kann es nicht zum Austritt von gefährlichen Stoffen in die Atmosphäre kommen. Im Gegensatz dazu besteht beim Magnetantrieb in einem solchen Störfall ein Sicherheitsrisiko. Durch die Verwendung eines doppelwandigen Spalttopfes kann dieses Risiko weitgehend minimiert werden, allerdings muss dazu der Spalttopfzwischenraum ständig überwacht werden.
Wie groß ist der Markt für wellendichtungslose Pumpen (Spaltrohrmotor- und Magnetkupplungspumpen)? Die Branche geht von rund 200 Mio. € weltweit aus, in Europa sind es schätzungsweise 60 Mio. €, in Deutschland allein noch rund 20 Mio. €. Dabei soll der Anteil Magnetkupplungs- zu Spaltrohrmotorpumpen im Bereich 2:1 liegen.
Aufgrund der neuen ATEX 100a, die auch für den nicht-elektrischen Pumpenteil gültig ist, verschiebt sich der Anteil zugunsten der Spaltrohrpumpen, wie ein Branchenvertreter berichtet. Denn die neue Vorschrift führe bei herkömmlichen Pumpen, auch bei den magnetgekuppelten Aggregaten, zu einem höheren Überwachungsaufwand bezüglich Trockenlauf und Temperatur. Eine Spaltrohrmotorpumpe als elektrisches Betriebsmittel besitze diese Sicherheitsvorkehrungen bereits, sie sei sozusagen inhärent ATEX 100-tauglich. Auf der ACHEMA 2006 werden die Pumpen-Hersteller eine Vielzahl neuer bzw. weiterentwickelter wellendichtungsloser Pumpen präsentieren.
Dosierpumpen: Systemlösungen im Trend
Es gibt nur wenige Einsatzfälle in der Industrie, wo die Kreiselpumpe von vornherein schlechte Karten hat. Das Dosieren ist solch ein Fall. Hier dominiert konstruktionsbedingt die Verdrängerpumpe. Auffallend ist, dass sich die Hersteller mehr und mehr auch um die Peripherie der Pumpe kümmern. Systemlösungen liegen im Trend, wie ein Blick auf das aktuelle Marktangebot zeigt. Die Hauptvorteile: Es gibt nur einen Lieferanten und Ansprechpartner, es treten keine Schnittstellenprobleme zwischen den einzelnen Komponenten auf und es sind keine eigenen Montageleistungen notwendig. Das gesamte System wird betriebsbereit vormontiert geliefert und auf Wunsch vor Ort durch den Lieferanten installiert und in Betrieb genommen.
Damit sind Fehlerquellen weitestgehend ausgeschlossen. Der Markt ist offenbar bereit für Individual-Module. Hintergrund: Relevant bei der Lösung einer spezifischen Aufgabenstellung sind vor allem die Eigenschaften des zu dosierenden Mediums und die im Prozess geforderte Genauigkeit. Auch in relativ einfach erscheinenden Anwendungsfällen hat Dosieren daher stets ganzheitlichen Charakter, ist ein Systemansatz der Installation von Einzelkomponenten überlegen.
Armaturen: Kostengünstiger automatisieren
Die deutschen Hersteller von Industriearmaturen erzielten im 1. Halbjahr 2005 ein Umsatzplus von 7 % (+ 13 % im Export). Interessant sind die Unterschiede bei den Bauarten: Die Hersteller von Absperrarmaturen erzielten im Vergleich zu anderen Armaturengruppen mit + 10 % den größten Umsatzanstieg (Inland: + 4 %; Ausland: + 18 %). Der Umsatz mit Sicherheits- und Überwachungsarmaturen stieg um 5 % an (Inland: - 5 %; Ausland: + 16 %). Dahingegen erhöhte sich der Umsatz mit Regelarmaturen im In- und Ausland lediglich um 2 %. Auch wenn die Regelarmaturen im betrachteten Zeitraum weniger nachgefragt wurden – der Anteil automatisierter Armaturen wächst beständig.
Zwei Anforderungsprofile einer Armaturen-Automation sind zu unterscheiden: Zum einen die reine Auf/Zu-Steuerung, bei der die Armatur nur in ihre jeweilige Endlage zu fahren ist; zum anderen der Regelbetrieb, wo mit einem Sollwert über die Veränderung der Armaturenstellung der Rohrleitungs-Durchfluss überwacht wird. Zu beachten ist, dass die Automatisierungskosten einer Armatur nicht nur von der Wahl der Industriearmatur selbst, sondern auch von den Betätigungsarten (manuell, elektrisch, pneumatisch, hydraulisch) abhängt. Je nach Kombination ergeben sich unterschiedliche Investitions-, Betriebs- und Energiekosten. Auf der ACHEMA 2006 kann der Besucher dazu die Angebote und Lösungsvorschläge aller relevanten Armaturen-Hersteller sichten.
Einen weiteren Aspekt gilt es zu beachten: 90°-Armaturen (Klappe, Hahn) benötigen im Vergleich zu den Linear-Armaturen (Ventil, Schieber) eine vergleichsweise geringe Stellkraft – der Antrieb fällt deshalb entsprechend kleiner und kostengünstiger aus. Zum Stichwort ‚kostengünstig’ dieser Praxisfall: Im Oktober 2005 kam es durch einen technischen Defekt zu einer Betriebsunterbrechung im Steamcracker eines großen Chemiekonzerns.
Die Sicherheitssysteme reagierten wie vorgesehen; das Rohgas wurde über die Hochfackel verbrannt. Ursache der Betriebsunterbrechung waren „untypische mechanische Schäden am Antriebsteil“ einer Spezialarmatur – der Schaden verursachte enorme Kosten: Jede Stunde, die die Fackel des Steamcrackers brannte, kostete den Konzern mehrere zehntausend €. Und wie man beobachten konnte, brannte die Fackel viele Stunden. Das Beispiel zeigt in klassischer Weise, wie eine vergleichsweise ‚billige’ Komponente enorme Schäden verursachen kann.
Was die Hersteller und Anwender auf der ACHEMA 2006 in besonderer Weise beschäftigen wird: Bis zum Jahr 2007 müssen alle Industrieanlagen in Deutschland den europäischen Vorschriften (IPPC-Direktive 96/61/EC) bzw. den nationalen Gesetzgebungen wie z. B. der TA Luft 2002 entsprechen. Bei Armaturen geht es um die Spindelabdichtung sowie die Gehäusedichtungen.
Für eine erfolgreiche Umsetzung der Vorschriften ist aber nicht nur die Qualität der Dichtungskomponenten entscheidend, sondern auch der Zustand der Alt- Armatur (eventuell sind Nacharbeiten erforderlich). Daneben ist zudem der sachgerechte Einbau der Dichtungen wichtig. Weitergehende Maßnahmen, wie z. B. die Tellerbefederung der Brille, geben zusätzliche Sicherheit für eine problemlose Spindelabdichtung. Der Zusatz- Nutzen: Zwar ist zum Erfüllen der gesetzlichen Vorschriften ein gewisser Kostenaufwand erforderlich, doch verlängern sich bei korrekter Planung und Umsetzung die Standzeiten und Wartungsintervalle.
Der Trend zu Units hält auch in der Armaturenbranche Einzug – praktische Beispiele sind Druckreduzier- oder Temperaturregelstationen. Der Vorteil aus Sicht des Betreibers bzw. Anlagenplaners: In großen Anlagen reduziert sich die Zahl der einzeln zu beschaffenden Komponenten erheblich, wenn Teilanlagen komplett geliefert werden. Der Lieferant übernimmt dabei die Details der Komponentenauslegung für die in der Unit installierten Armaturen, Rohrleitungen etc. unter Beachtung von Vorschriften und Regelwerken, er sorgt zudem für eine ordnungsgemäße Zertifizierung und stellt die komplette Dokumentation zusammen.
Ob bei Pumpen oder bei Armaturen: Wer als Betreiber vor der Investitionsentscheidung konsequent die Frage nach den ‚Lebenszykluskosten’ abklopft, liegt nicht nur unter energetischen Gesichtspunkten auf der sicheren Seite. Geringere LCC-Kosten liefern auch einen Hinweis darauf, dass die Pumpe oder die Armatur gut zur Anlage und zum Prozess passt und deshalb das Ausfallrisiko geringer ist. Dazu müssen unter Umständen auch einmal eingefahrene Wege verlassen werden. Dass sich das im Einzelfall lohnen kann, zeigt diese kürzlich veröffentlichte Einschätzung: Eine LCC-Betrachtung lohne besonders beim Vergleich unterschiedlicher Pumpenkonzepte – da fänden sich oft signifikante Unterschiede. Deutlich geringer seien Einsparungen bei den LCC-Kosten beim Vergleich von Pumpen gleicher Bauart, nur unterschiedlicher Hersteller.
Zur ACHEMA präsentieren sich in den Hallen 8 und 9 mehr als 850 Firmen mit neuesten und bewährten technologischen Konzepten.
Quelle: DECHEMA Ausstellungs-GmbH