Poresta Systems bringt Wannenträger mit drehzahlgeregelter Vakuumpumpe von Atlas Copco in Form
Die Poresta Systems schlägt bei der Vakuumerzeugung einen komplett neuen Weg ein und wird dafür mit einer Effizienzsteigerung von mehr als 50 Prozent belohnt. Der Hersteller von Wannenträgern und bodenebenen Duschplatzlösungen erzeugt das für die Fertigung seiner EPS-Formteile notwendige Vakuum heute mit einer ölgefluteten Schraubenvakuumpumpe von Atlas Copco.
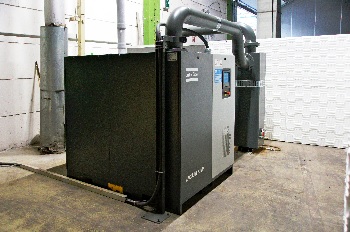
Eine intelligente Prozessgaskühlung macht den Austausch der hier traditionell verwendeten Flüssigkeitsringpumpen möglich.
Der Mut, neu und manchmal auch unkonventionell zu denken, prägt die Firmenphilosophie der Poresta Systems GmbH in Bad Wildungen. So revolutionierte das Unternehmen bereits vor mehr als 40 Jahren mit seinem damals entwickelten Wannenträger aus expandiertem Polystyrol (EPS) die Gestaltung deutscher Badezimmer. Seitdem wurde das intelligente System europaweit mehr als 30 Millionen Mal ausgeliefert. Es hat den Einbau von Badewannen radikal vereinfacht. Danach folgten Systeme für bodenebene Duschplatzlösungen, die nicht nur in puncto Design überzeugen, sondern auch den steigenden Anspruch nach barrierefreiem Komfort im Blick haben.
„Wir investieren Jahr für Jahr überdurchschnittlich in Forschung und Entwicklung“, beschreibt Marcus Trier, Leiter Technische Dienste bei Poresta Systems, die Grundlage der Innovationskraft des Unternehmens. „Jedes Jahr melden wir neue Schutzrechte auf unsere Innovationen an und arbeiten aktiv in Forschungsprojekten mit. In den letzten Jahren haben wir uns stark darauf konzentriert, viele anwendungstechnische Fragestellungen zu lösen, wie Abdichtung, Schallschutz, Barrierefreiheit – also die ganzen flankierenden Themen rund um unsere Produkte.“
Vakuum beschleunigt Stabilisierungsprozess der EPS-Formteile
„Die stecknadelkopfgroßen EPS-Perlen, die wir geliefert bekommen, sind mit Gas beladen“, erläutert Marcus Trier. „Wir beaufschlagen sie mit Wärme. Dabei dehnt sich das Gas aus. Die Perlen vergrößern sich und werden dann in speziellen Silos zwischengelagert.“ Danach werden die nun linsengroßen Kugeln in einen der insgesamt 23 Formteilautomaten gefüllt. „Die Form ist ein in sich abgeschlossenes System“, erklärt Marcus Trier. „Wir leiten heißen Dampf hinein, wodurch das Material zu expandieren beginnt. Es versintert dann zu einem festen Körper. Nach einer Verweilzeit wird die Form wieder auf etwa 60 Grad Celsius gekühlt.“ An dieser Stelle kommt die neue Vakuumanlage ins Spiel: Die Form wird auf 0,3 bar absolut evakuiert, das Formteil beginnt sich zu stabilisieren. Anschließend wird es durch ein Handling-System aus der Form entnommen.
„Ohne das Vakuum würde der Stabilisierungsprozess deutlich länger dauern, denn nach dem Sinterprozess ist das Formteil nass“, ergänzt Denny Szabó, Instandhaltungstechniker bei Poresta Systems und mitverantwortlich für die Sanierung der Vakuumanlage. „Mit der Vakuumpumpe entziehen wir dem Prozess die Energie und Feuchtigkeit, die im Material nach dem Phasenübergang in Form von gesättigtem Wasserdampf enthalten sind.“ Der hohe Wasseranteil im abgesaugten Gas ist der Grund dafür, dass in der EPS-Herstellung traditionell Flüssigkeitsringpumpen eingesetzt werden. Wasser beziehungsweise eine wässrige Flüssigkeit gehört zum Funktionsprinzip dieser Pumpen; hohe Feuchtigkeitsanteile sind daher unproblematisch. Nachteilig ist jedoch die vergleichsweise geringe Effizienz der Technologie. Bis 2015 wurden in Bad Wildungen 22 dieser Pumpen in drei Stationen betrieben. Diese sind jeweils einer Gruppe von Formteilautomaten zugeordnet. Heute ersetzt eine ölgeflutete Schraubenvakuumpumpe GHS 1900 VSD+ mit Drehzahlregelung von Atlas Copco bereits zwei Stationen mit 15 Pumpen, die letzten sieben werden in Kürze folgen.
Intelligentes Temperaturmanagement und Prozessgaskühlung
Dass der Umstieg auf diese wesentlich effizientere Technologie möglich wurde, ist dem intelligenten Temperaturmanagement der GHS-Pumpen sowie einer zusätzlichen Prozessgaskühlung vor der Vakuumpumpe zu verdanken. „Normalerweise würde der Wasserdampf in der Pumpe kondensieren, wenn ich ihn komprimiere“, erklärt Wolfgang Holtapel, Technischer Berater bei der Essener Atlas Copco Kompressoren und Drucklufttechnik GmbH. „Für eine ölgeschmierte Pumpe ist das problematisch, denn das Wasser unterbricht den Schmierkreislauf und führt zu Korrosion. Das macht so eine Pumpe in der Regel ein bis zwei Wochen mit, bevor sie den Geist aufgibt.“
Wärmetauscher unterstützt und verstärkt die Vakuumpumpe
Aus diesem Grund hat Wolfgang Holtapel zusammen mit Denny Szabó eine zusätzliche Prozessgaskühlung entwickelt. Der aus den Formteilautomaten abgesaugte Dampf durchläuft zunächst einen Wärmetauscher, bevor er die Vakuumpumpe erreicht. „Wir kühlen den Dampf so weit wie möglich herunter“, erläutert Holtapel. „Der kondensiert zu großen Teilen und kann dem Prozess in Form von Wasser entzogen werden. Parallel verkleinert sich das Dampfvolumen, und das erzeugt ein zusätzliches Vakuum, was die Effizienz des Gesamtprozesses steigert.“
Nun komme man natürlich prozesstechnisch nicht auf so tiefe Temperaturen, dass man die Feuchtigkeit komplett eliminieren könne. „Mit der neuen Technologie unserer GHS-Pumpen sind wir aber in der Lage, sehr hohe Wasserdampfanteile zu fahren“, erklärt Holtapel. „Wir halten die Pumpe durch ein Temperaturmanagement heiß, so dass es nicht zur Kondensation im Öl kommen kann. Auf diese Weise konnten wir hier vom System der Flüssigkeitsringpumpe auf ein ölgeschmiertes System übergehen, was wesentlich effizienter ist.“
Steuerung nach Bedarf spart 15.000 Euro Strom pro Jahr
Für die Fertigung der Wannenträger und Duschplatzlösungen wird grundsätzlich ein kontinuierliches Vakuum benötigt, jedoch schwankt der Bedarf aufgrund der unterschiedlichen Taktzeiten der Formteilautomaten stark. „Diese Schwankungen haben wir vorher nicht mit drehzahlgeregelten Motoren abgebildet, sondern mit einer reinen Kaskadenschaltung“, blickt Szabó zurück. „Das heißt, bei Bedarf schalteten sich die Pumpen nacheinander zu. Und wenn kein Bedarf da war, lief nur eine Grundlastpumpe. Jetzt haben wir eine Drehzahlregelung und können unser Vakuum nach Prozessbedarf steuern. Das läuft sehr gut.“
Die neue GHS-Pumpe besitzt einen maximalen Saugvolumenstrom von 1750 m3/h bei 100 mbar absolut und eine Leistungsaufnahme von 37 kW. Die 15 Flüssigkeitsringpumpen, die sie zurzeit ersetzt, haben zwischen 4 und 5,5 kW. Das heißt, die installierte Leistung konnte um die Hälfte reduziert werden. „Allein durch die Drehzahlregelung und den Austausch der alten Pumpen haben wir eine Energieeinsparung von rund 55 Prozent im Vergleich zu unserer früheren Lösung erreicht“, beziffert Marcus Trier den Effizienzgewinn. „Dadurch werden wir pro Jahr etwa 15.000 Euro an Stromkosten sparen. Außerdem konnten wir die Lärmbelastung reduzieren, indem wir die neue Pumpe nicht in der Produktion, sondern eine Etage höher im Lagerbereich aufgestellt haben.“
Hannover Messe 2014 gibt den Startimpuls
„Die Aufstellung der Pumpe oberhalb der Produktion und des Kondensators ist auch aus prozesstechnischer Sicht geboten“, begründet Wolfgang Holtapel. „Denn wir wollen das entstehende Kondensat ja ausschleusen und nicht weiter in die Pumpe verschleppen. Und wenn ich die Pumpe eine Etage höher stelle, dann müsste das Wasser mit dem Saugstrom mitgerissen werden und zudem die Schwerkraft überwinden. Stattdessen läuft es zurück.“
Den Impuls, die Vakuumversorgung umzugestalten, gab ein Besuch der Hannover Messe. Eigentlich habe man sich dort zum Thema Kompressoren informieren wollen, erinnert sich Trier, und sei dabei am Stand von Atlas Copco auf die GHS-Schraubenvakuumpumpe gestoßen. Da die verwendeten Flüssigkeitsringpumpen bereits zwischen 15 und 20 Jahre alt und sehr wartungsintensiv waren, habe man die Gelegenheit genutzt und sich über mögliche Alternativen informiert.
Installierte Probemaschine konnte überzeugen
Es folgte die Installation einer Probemaschine und eine Phase des „experimentellen Herantastens“ an die optimale Lösung. „Wir haben einen Messaufbau gemacht und die Stromaufnahme über einen definierten Zeitraum verglichen“, sagt Holtapel. „Dabei wurden relativ hohe Energieeinsparungen sichtbar. Das hat uns gezeigt, dass der geplante Umbau sinnvoll ist.“
„Die Probemaschine haben wir hier aufgestellt, weil wir noch keine Erfahrungswerte mit dieser Technik hatten und nicht gleich ins kalte Wasser springen wollten“, ergänzt Szabó. „Die Versuche liefen dann sehr gut, und nachdem das Konzept mit dem vorgeschalteten Wärmetauscher komplett abgeschlossen war, haben wir die Pumpe im Dezember 2015 bestellt und im Januar 2016 in Betrieb genommen.“ Vorher seien noch das Rohrleitungsnetz und die Elektrik angepasst worden.
Vakuumkonzept soll auf komplette Produktion erweitert werden
Nach einem guten halben Jahr Betrieb war man in Bad Wildungen mit der neuen GHS so zufrieden, dass nun auch die letzten sieben Flüssigkeitsringpumpen ersetzt werden sollen. Die Auslastung der neuen Pumpe liegt derzeit bei 60 bis 70 Prozent. Es wäre also theoretisch möglich, auch noch die verbleibenden Formteilautomaten ins Konzept zu integrieren. „Die neue Anlage bietet uns noch Reserven, aber wir überlegen zurzeit, ob wir die gewünschte Redundanz mit den Altanlagen herstellen oder noch eine weitere GHS-Pumpe von Atlas Copco einbinden“, erklärt Denny Szabó. Außerdem denke man darüber nach, einen alten 30 m³ großen Dampfspeicher als Puffer für das Vakuum zu nutzen. Das würde auf der einen Seite eine weitere Reserve schaffen und auf der anderen den Lärmpegel der Anlage noch einmal reduzieren, da diese ruhiger regelt, wenn sie ein Puffervolumen zur Verfügung hat.
„Wenn es so läuft wie bisher, kommen wir auf eine Amortisationszeit von rund zwei Jahren“, resümiert Marcus Trier. „Wenn wir noch die dritte Station mit sieben weiteren Flüssigkeitsringpumpen in die jetzige Lösung einbinden könnten, würden wir – den zusätzlichen Rohrleitungsaufwand mitgerechnet – deutlich unter zwei Jahren bleiben. Wir werden jetzt testen, ob wir mit einer Schraubenvakuumpumpe auskommen, und dann entscheiden, ob wir noch eine zweite anschaffen.“
Bild: Die ölgeflutete Schraubenvakuumpumpe GHS 1900 VSD+ mit Drehzahlregelung von Atlas Copco ersetzt in Bad Wildungen zurzeit 15 Flüssigkeitsringpumpen mit Leistungen zwischen 4 und 5,5 kW. Die GHS-Pumpe besitzt einen maximalen Saugvolumenstrom von 1750 Kubikmetern bei 100 mbar absolut und eine Leistungsaufnahme von 37 kW, das heißt, die installierte Leistung konnte um die Hälfte reduziert werden. (Bild: Atlas Copco Kompressoren und Drucklufttechnik)
Quelle: Atlas Copco Holding GmbH