Maggiore durata e stabilità del processo con l’uso di rivestimenti speciali
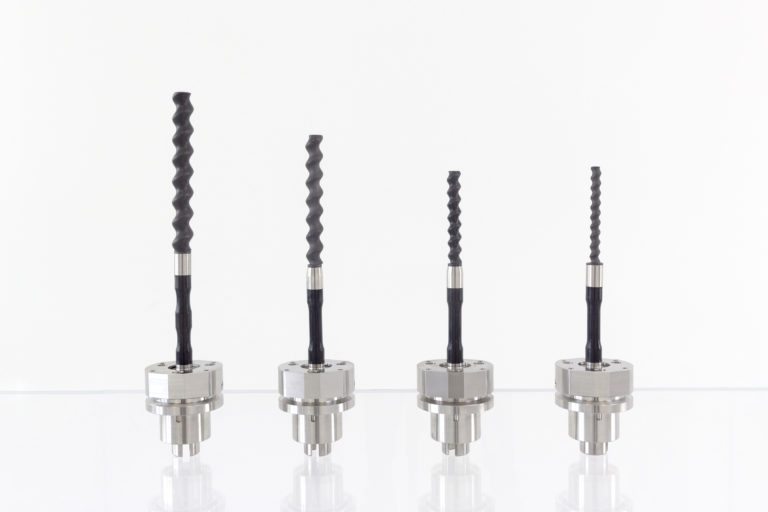
Il nuovo rotore ceramico per la serie RD-Dispenser di ViscoTec. (Fonte immagine: ViscoTec Pumpen- u. Dosiertechnik GmbH)
Requisiti crescenti nella produzione di componenti elettronici
Il design sempre più piccolo e compatto dei componenti elettronici, con densità di energia e prestazioni in costante aumento, richiede una gestione precisa della temperatura per garantire il loro funzionamento sicuro durante la vita del prodotto. Il collegamento termico dei moduli elettronici o dei moduli batteria al dissipatore di calore è fondamentale per dissipare il calore generato attraverso il dissipatore di calore e quindi prevenire il surriscaldamento. A tale scopo vengono utilizzate paste termoconduttrici e adesivi con conducibilità termiche sempre più elevate per eliminare il traferro.
Fino ad ora, le solite paste termoconduttrici avevano solo conduttività termiche comprese tra 0,8 e 2,0 W / mK. Grazie a proporzioni più elevate di particelle solide termicamente conduttive e alla selezione specifica di distribuzioni granulometriche e diversi tipi di riempitivi, ora sono stati raggiunti valori fino a 7 a 8 W / mK. Questi riempitivi per lo più ceramici, come l'ossido di alluminio o il nitruro di alluminio, hanno una conducibilità termica notevolmente elevata combinata con l'isolamento elettrico. Tuttavia, a causa della loro elevata durezza Mohs fino a 9 o 10, stanno generando sfide per la tecnologia di erogazione per quanto riguarda l'usura e gli intervalli di manutenzione.
Per decenni ViscoTec si è specializzata in applicazioni di dispensazione così impegnative in un'ampia gamma di settori. La vita utile del sistema può già essere notevolmente aumentata mediante un'attenta selezione dei componenti del sistema in relazione alle rispettive esigenze del cliente. Tuttavia, l'usura è inevitabile per ogni tecnologia durante l'erogazione di fluidi abrasivi.
I test a lungo termine spesso confermano una maggiore durata dei componenti di nuova concezione
Tuttavia, per aumentare in modo significativo la durata dei componenti di erogazione, il collaudato rotore in acciaio inossidabile è stato ulteriormente sviluppato mediante l'uso di rivestimenti speciali basati su Diamond Coating.
Più nello specifico, la nuova versione di rotore, realizzata in una tecnica completamente ceramica, rivoluziona l'erogazione volumetrica di paste termoconduttrici: in numerosi test interni a lungo termine, così come nei test sul campo effettuati nei sistemi esistenti del cliente, una chiara ottimizzazione essere dimostrato. Lo speciale rivestimento può raddoppiare o triplicare la durata dei componenti principali. Secondo le esperienze attuali, con la versione con rotore ceramico la durata utile dei componenti centrali può essere estesa da circa 9 a 10 volte.
I vari test a lungo termine con tempi di funzionamento che vanno da diversi mesi a più di un anno e quantità di materiale erogato da diverse centinaia a migliaia di litri non mostrano quasi alcun segno di usura sul rotore ceramico fino ad oggi. È ancora possibile un'erogazione stabile e sicura per il processo, il che rende concepibile un periodo di utilizzo molto più lungo. Pertanto, il costo in uso può essere notevolmente ridotto.
"Combatti il fuoco con il fuoco: questo è il motto del rotore in ceramica", afferma Manuel Paintmayer, Relationship Manager Material Manufacturing presso ViscoTec. "Grazie alla durezza della superficie da 3 a 4 volte superiore rispetto alla precedente versione in acciaio inossidabile con cromatura dura di il rotore, i test a lungo termine con riempitivi all'avanguardia non hanno ancora mostrato alcuna usura misurabile o danni alla superficie del rotore ceramico ", continua Paintmayer. La controparte del rotore nell'erogatore è lo statore, che è fatto di elastomeri speciali.Gli statori hanno anche una vita utile molto più lunga a causa della superficie invariata del rotore.
I rotori in ceramica per granulometrie da 50 µl non hanno mostrato segni di malfunzionamento o usura dopo più di 100 l di riempimento del gap di erogazione. Ciò corrisponde a più di 2.000.000 di colpi singoli. Risultati identici sono stati mostrati per dispenser più grandi con dimensioni del colpo da 1,7 ml. Dopo più di 4.000 l di materiale erogato, non è stato possibile misurare alcun segno di usura sul rotore ed era ancora possibile un'erogazione precisa e stabile. Questi risultati sono stati ottenuti anche utilizzando un solo statore.
L'utilizzo di rotori ceramici si traduce quindi in numerosi vantaggi per i clienti:
- Massima affidabilità di processo grazie alla precisione di dosaggio inalterata del sistema di dosaggio volumetrico
- Riduzione al minimo dei tempi di configurazione e inattività
- Riduzione dei costi grazie alla richiesta minima di parti di ricambio e al minimo costo di utilizzo
- Facile da integrare nei sistemi esistenti
I clienti di ViscoTec sono entusiasti: "Non è stato necessario ricalibrare il sistema di erogazione una sola volta durante un intero anno di produzione per compensare la possibile usura". Un vantaggio per tutte le parti.