Leipa setzt bei der Abwasserreinigung auf Schraubengebläse von Atlas Copco
Als im Werk Schwedt Nord der Leipa Georg Leinfelder in Schwedt – damals noch Teil der finnischen UPM-Gruppe – die Erneuerung der Druckluftversorgung für die Belebungsbecken der Abwasserreinigungsanlage anstand, wollte der Papierproduzent eigentlich wie gehabt mit Turboverdichtern arbeiten.
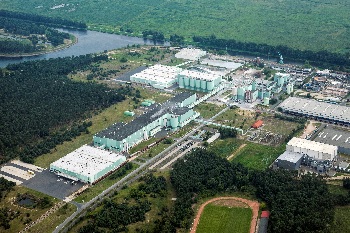
Der Leipa-Standort aus der Luft. (Foto: Leipa)
Doch während der Planung überzeugten die ölfrei verdichtenden Schraubengebläse von Atlas Copco aufgrund ihrer größeren Flexibilität und des besseren Preis-Leistungs-Verhältnisses. Auch in puncto Energieverbrauch können die Schrauben mit der hocheffizienten Turboverdichter-Technologie mithalten.
Die Stadt Schwedt in der Uckermark, Produktionsstandort der Leipa Georg Leinfelder, zählt mit rund 30000 Einwohnern zu Brandenburgs Mittelzentren. Mit der Abwasserreinigungsanlage im Werk Schwedt Nord der Leipa-Papierfabriken ließen sich theoretisch die Abwässer der rund zehnmal so großen Stadt Augsburg reinigen, denn die Anlage besitzt einen sogenannten Einwohnerwert von rund 300000. „Papierhersteller haben verfahrensbedingt einen hohen Wasserbedarf und produzieren auch entsprechend große Mengen an Abwasser“, erklärt Ulf Riege, Leiter der Mechanischen Instandhaltung bei Leipa. „Doch haben sich die Prozesse bei uns in Schwedt über die Jahre dahingehend verbessert, dass sich die Abwassermenge von rund 20 Litern pro Kilogramm produziertes Papier auf nur noch acht Liter verringert hat.“
Das Problem dabei: Bislang belüfteten zwei große Turbokompressoren die aerobe biologische Stufe der Abwasserreinigung, wobei eine der beiden Maschinen jeweils als Redundanz fungierte. Durch die gesunkenen Abwassermengen liefen die Turbos aber nicht mehr im optimalen Betriebsbereich, der bei dieser Technologie sehr eng ist. Als dann Ende 2013 nach 20 Jahren Betrieb eine größere Reparatur anstand, entschloss man sich, die Belüftung der insgesamt vier Belebungsbecken komplett neu zu planen und die beiden Turbos durch vier Schraubengebläse von Atlas Copco zu ersetzen – je zwei Geräte mit fester und zwei mit variabler Drehzahl. „Wir haben jeweils ein Gebläse mit fester und eins mit variabler Drehzahl in Betrieb, die anderen beiden stehen als Redundanz zur Verfügung“, beschreibt Riege das neue Anlagenkonzept. „Die Verfügbarkeit der Druckluft ist an dieser Stelle äußerst wichtig, denn wenn die Biologie nicht richtig arbeitet, steht die komplette Produktion, und das wird dann teuer.“
Energieverbrauch wichtiger Aspekt beim Druckluftkonzept
Auf der Papiermaschine im Werk Schwedt Nord werden derzeit pro Jahr 280000 Tonnen grafische Papiere für den Zeitungsdruck hergestellt. Seit Ende 2001 gehörte der Standort zur finnischen UPM-Gruppe, wurde dann im Sommer 2016 von der Leipa Georg Leinfelder GmbH übernommen. Die fertigt bereits seit 1992 im Werk Süd auf dem Nachbargrundstück mit drei weiteren Papiermaschinen Magazin- und Verpackungspapiere, Spezialpapiere und Karton. Als Rohstoff wird in beiden Werken ausschließlich Altpapier in verschiedenen Qualitäten verwendet. „Die Themen Energieeffizienz und Umwelt haben bei uns im Unternehmen einen hohen Stellenwert“, betont Ulf Riege. „Wir sind nach EMAS (Eco-Management and Audit Scheme; Anm. d. R.) zertifiziert und betreiben ein Energiemanagementsystem gemäß ISO 50001. Darin verpflichten wir uns, unseren Energiebedarf jährlich um mindestens ein Prozent zu reduzieren. Die ISO 50001 gibt auch vor, dass bei Neuanschaffungen der Energieverbrauch immer berücksichtigt werden muss – das war bei der Konzeption der neuen Druckluftstation ein wichtiger Aspekt.“
Seit Anfang 2015 arbeiten in der Station insgesamt vier ölfrei verdichtende Schraubengebläse des Typs ZS 132+ von Atlas Copco. Zwei der Maschinen tragen das Kürzel VSD und sind mit einer Drehzahlregelung ausgestattet, so dass der Volumenstrom automatisch genau an den Luftbedarf angepasst wird. Die Gebläse stellen jeweils maximal 4100 Normkubikmeter pro Stunde bei einem Überdruck von 0,9 bar bereit. „Der Überdruck ergibt sich aus der maximalen Tiefe der Belebungsbecken“, erläutert Riege. „Diese beträgt neun Meter, und weil die Druckluft am Beckenboden eingeblasen wird, muss der Überdruck mindestens der Wassersäule entsprechen.“ Ein weiteres wichtiges Kriterium ist die absolute Ölfreiheit der erzeugten Druckluft, denn, so Riege, „wir wollen selbstverständlich kein Öl in unsere Biologie oder in die Umwelt eintragen“.
Datenerfassung und Dokumentation über Prozessleitsystem
Die Gebläse werden über das Prozessleitsystem des Unternehmens gesteuert. „Jedes Aggregat hat eine eigene eingebaute Gerätesteuerung von Atlas Copco“, erklärt Maximilian Borngräber, Prozessingenieur bei Leipa und mitverantwortlich für die Konzeption der neuen Druckluftstation. „Wir übergeben dann alle Werte an unser Prozessleitsystem. Dort haben wir eine übergeordnete Steuerung abgebildet, über die wir die Prozesswerte der Anlage jederzeit anpassen und optimieren können.“ Alle Daten werden erfasst und dokumentiert. Betriebszustände, Volumenströme und Energieverbräuche können jederzeit abgerufen werden. „Das Prozessleitsystem erfasst unter anderem auch die Leistungsaufnahme der Aggregate“, beschreibt Borngräber. „Dadurch, dass wir diese Daten sammeln und entsprechend auswerten, lassen sich die notwendigen Einsparungsnachweise für unser Energiemanagementsystem einfach generieren.“
Effizienter und flexibler Betrieb
Die Schraubengebläse aus der Serie ZS+ von Atlas Copco werden als einsatzbereite Komplettpakete mit SPS-basierter Elektronikon-Steuerung, integriertem Umrichter, Gabelstaplertaschen, Rückschlagventil, Luftfilter, Abblasventil und Schalldämpfern geliefert. Durch die kompakte Bauform sind keine Extras erforderlich, und der Installationsaufwand ist minimal. Der Preis für die vier neuen Gebläse mit einer Liefermenge von insgesamt 16400 Normkubikmetern pro Stunde entsprach dem für einen neuen Turbokompressor mit 12000 Normkubikmetern pro Stunde. „Im Vergleich zu den alten Turbos – die allerdings nicht im optimalen Betriebsbereich liefen – sparen wir mit der neuen drehzahlgeregelten Anlage 700000 Kilowattstunden pro Jahr“, rechnet Borngräber. „Diese Einsparungen dokumentieren wir zum einen im Rahmen unseres Energiemanagementsystems. Vor allem aber bedeuten sie für uns natürlich bares Geld, denn wir können nur etwa ein Viertel des benötigten Stroms in unserem BHKW selbst erzeugen, die restlichen drei Viertel kaufen wir zu.“
Neben ihrem energieeffizienten Betrieb waren es vor allem zwei Faktoren, die zur Entscheidung für die Atlas-Copco-Gebläse führten. „Wir haben uns für den Wechsel von Turboverdichtern auf Schraubengebläse entschieden, weil die Gebläse zum einen kostengünstiger und zum anderen in der Produktion flexibler sind“, erklärt Borngräber. „Sie können eine größere Schwankungsbreite effizient bedienen, was im Bereich der biologischen Abwasseraufbereitung beispielsweise aufgrund der temperaturbedingt unterschiedlichen Luftbedarfe wichtig ist.“ Die höhere Flexibilität sei ein Resultat der Drehzahlregelung und der kleineren verfügbaren Gerätegrößen. „Bei den Turbos gehörten unsere bisherigen Maschinen mit circa 14000 Normkubikmeter pro Stunde schon zum Kleinsten, was der Markt damals im Niederdruck zu bieten hatte“, weiß Borngräber. „Diese Menge können wir mit drei Gebläsen à 4000 Normkubikmetern sowie einem Gerät als Redundanz realisieren. Bei den Turbos hätten wir inklusive Redundanz zwei Aggregate mit jeweils 12000 Normkubikmetern pro Stunde benötigt.“ Das aber hätte neben den Investitions- auch die Instandhaltungskosten gesteigert.
Produktionsumstellung erfordert Erweiterung der Druckluftversorgung
Als nächstes kann die Druckluftstation unter Beweis stellen, dass sie sich auch flexibel erweitern lässt. Denn zum Jahresende 2017 wird die Produktion im Werk Schwedt Nord von grafischen Papieren für den Zeitungsdruck auf sogenannte weißgedeckte Testliner umgestellt. Diese wesentlich schwereren Papiere kommen als Decklage in der Kartonagen-Produktion zum Einsatz und werden unter anderem vom stetig wachsenden Versandhandel nachgefragt. „Durch diese Prozessumstellung erhöht sich die produzierte Papiermenge von derzeit 280000 Tonnen auf rund 450000 Tonnen pro Jahr“, erläutert Ulf Riege. „Entsprechend steigt auch die zu reinigende Abwassermenge an.“ Die Abwasserreinigung wird deshalb zurzeit von zwei auf drei Linien erweitert, und auch bei der Druckluft ist die Aufstockung um zwei bis drei weitere Gebläse in der Planung. „Die biologische Reinigungsstufe wird zwar nicht größer, aber durch geeignete Maßnahmen und mehr Sauerstoff effektiver“, resümiert Riege. „Die erweiterte Anlage wäre dann mit einem Einwohnerwert von rund 500000 auch für eine Großstadt wie Dresden oder Hannover passend.“
Quelle: Atlas Copco Holding GmbH