La 150 000e pompe péristaltique Bredel vendue au client au Mexique
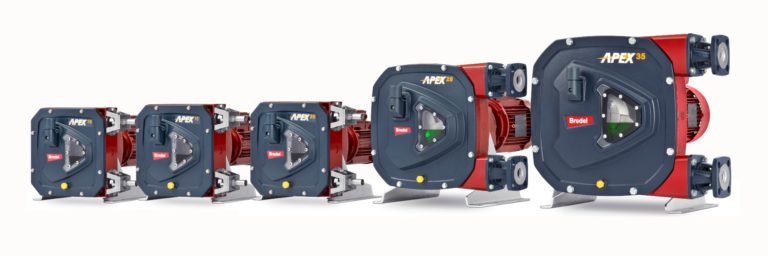
150 000e pompe péristaltique Bredel vendue à un client au Mexique. (Source de l'image: Watson Marlow Fluid Technology)
La dernière décennie a vu une augmentation considérable de l'utilisation des pompes à tuyau Bredel dans des secteurs tels que l'exploitation minière et la construction, où elles respectent des réglementations environnementales strictes dans des conditions de travail très difficiles.
Cela fait plus d'un demi-siècle que Bredel a développé la pompe péristaltique à tuyau à usage industriel. Aujourd'hui, ces unités de haute performance transfèrent et dosent une multitude de fluides et solides agressifs, visqueux et abrasifs dans des secteurs tels que le brassage, le traitement de l'eau, la construction, la chimie et l'exploitation minière. Les droits de transfert de produits chimiques dans la production de batteries lithium-ion sont actuellement une application qui connaît une croissance particulièrement rapide. La commande la plus importante à ce jour pour les pompes à tuyau Bredel était de 174 unités APEX à un fabricant de matériaux pour batteries lithium-ion en Chine.
La vente de la 150 000 e pompe à un client au Mexique faisait partie d'un envoi expédié de l'usine de fabrication de Bredel à Delden, aux Pays-Bas, qui constituait 16 pompes réparties sur huit modèles différents. Le débit combiné de ces pompes est d'environ 1 560 l / min.
Décennie d'innovation
Les pompes Bredel continuent d'évoluer, avec de nombreuses réalisations notables au cours des 10 dernières années. La gamme APEX, lancée en 2012 et élargie en 2015, en est un bon exemple. Les pompes APEX sont conçues pour offrir un rapport prix / performances très compétitif. La gamme offre des débits allant jusqu'à 6 200 l / h et une pression de refoulement jusqu'à 8 bars, tandis que la gamme plus large de pompes à tuyau Bredel comprend des unités qui fournissent un débit jusqu'à 108 000 l / h et une pression jusqu'à 16 bars.
En ce qui concerne le principe de fonctionnement, les pompes Bredel n'ont pas de joints, vannes, diaphragmes, stators, presse-étoupes ou autre matériel coûteux à remplacer, garantissant ainsi leur entretien facile sur place sans déplacement dans un atelier. Seul le tuyau nécessite un remplacement occasionnel, ce qui est une tâche simple.
Longue durée de vie
La technologie des tuyaux de Bredel a également franchi un certain nombre de progrès notables ces dernières années. Un exemple typique est le Bredel NR Endurance, qui a fait ses débuts sur le marché en 2018. Ce tuyau avancé offre une durée de vie jusqu'à 50% plus longue dans les applications de pompage abrasif, comme l'a récemment illustré un client de l'industrie chimique.
L'usine chimique pompe le lisier de PCC (carbonate de calcium précipité) jusqu'à une viscosité de 1000 cPs. Grâce à une configuration optimisée, le tuyau en caoutchouc standard de Bredel a duré 4 468 800 occlusions, ce qui équivaut à 110 jours ou 2 660 heures. Cependant, en passant au Bredel NR Endurance, la durée de vie s'est étendue à 7 056 000 occlusions, soit environ 175 jours ou 4 200 heures (un gain de 57%). Ce succès a contribué au retour sur investissement de ses nouvelles pompes à tuyau Bredel en 12 mois.
Ventes directes
Aujourd'hui, WMFTG propose des ventes directes de pompes Bredel dans 43 pays et en croissance, la Finlande, la Norvège, les Pays-Bas, la Belgique, l'Allemagne, l'Espagne, le Portugal et la République tchèque (y compris la Slovaquie) rejoignant la liste en 2021. Tous ces pays ont des bureaux de vente existants ou récemment créés, dotés des propres ingénieurs d'application et spécialistes de produits expérimentés de WMFTG. Les clients bénéficient ainsi de la commodité et de l'attention personnelle qu'offrent les vendeurs directs.
Pour soutenir ses efforts de vente, un investissement important à l'usine de Bredel à Delden facilite des livraisons encore plus rapides aux clients. L'arrivée récente d'un centre de tournage-fraisage CNC avancé capable d'usiner des composants présentant à la fois des caractéristiques cylindriques et prismatiques en une seule configuration, évite non seulement le besoin de deux machines distinctes, mais réduit considérablement les délais. Complété avec un chargement / déchargement automatisé et un système de stockage avancé, l'investissement s'est élevé à 3,4 millions d'euros.