FWA optimiert biologische Reinigungsstufe mit Turbogebläsen von Atlas Copco
Im Zuge der Optimierung ihrer biologischen Reinigungsstufe erhielt die kommunale Kläranlage in Frankfurt (Oder) 2015 auch ein neues Druckluftkonzept.
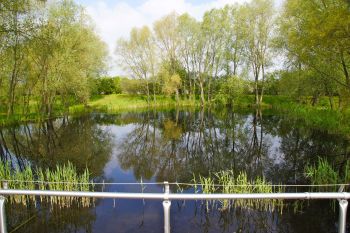
Letzte Station vor dem Vorfluter: Über die sogenannten Schönungsteiche fließt das gereinigte Abwasser in die Oder. (Bild: Atlas Copco Kompressoren und Drucklufttechnik)
Heute versorgen zwei drehzahlgeregelte, magnetgelagerte Turbogebläse von Atlas Copco die Belebungsbecken zuverlässig mit Sauerstoff. Die Frankfurter Wasser- und Abwassergesellschaft profitiert von der energieeffizienten Technik und einem leisen, nahezu wartungsfreien Betrieb.
Schaut man sich die Verbraucher elektrischer Energie einer kommunalen Kläranlage an, dann steht die biologische Reinigungsstufe mit Abstand an erster Stelle. Soll also Energie eingespart werden, kann es sinnvoll sein, dort anzusetzen. Die Frankfurter Wasser- und Abwassergesellschaft mbH (FWA) in Frankfurt an der Oder legt größten Wert auf einen effizienten Betrieb ihrer Abwasserreinigungsanlage, „denn wir wollen die Gebühren für die angeschlossenen Haushalte und Firmen natürlich so gering wie möglich halten“, erklärt Ronald Börner. Der studierte Verfahrenstechniker ist für den reibungslosen Betrieb der Kläranlage mitverantwortlich und hat in den vergangenen Jahren die Projekte zur Steigerung der Energieeffizienz auf der Anlage begleitet. „Durch die Verwertung des Klärgases im betriebseigenen BHKW können wir heute bereits 77 Prozent der benötigten elektrischen Energie und fast 100 Prozent der thermischen Energie selbst erzeugen“, erklärt Börner. „Unser Ziel ist es, diese Zahlen kontinuierlich zu verbessern. Aus diesem Grund haben wir bereits 2012 die biologische Reinigungsstufe in puncto Effizienz überprüft und in der Folge die bis dahin verwendeten Tellerbelüfter gegen Plattenbelüfter ausgetauscht.“
Ursprünglich für einen Einwohnerwert (EW) von 120000 ausgelegt, arbeitet die 1996 erbaute Anlage derzeit im Mittel mit einem EW von 85000. Neben privaten Haushalten in Frankfurt und den umliegenden Gemeinden ist auch eine größere Brauerei an die Kläranlage angeschlossen. Die Abwasserreinigung beginnt im Rechengebäude mit der Separierung grober Feststoffe. Es folgt der belüftete Sandfang, wo sich der Sand absetzt, mittels Mammutpumpen abgezogen und entsorgt wird. Anschließend erreicht das Abwasser die Vorklärung. Hier setzt sich der Primärschlamm ab, wird mit einem Räumerwagen abgezogen und über einen Trichterbehälter in die Faulbehälter der Klärschlammaufbereitung gepumpt.
Vier Belebtschlammbecken für biologische Abbauprozesse
An die Vorklärung schließen sich vier Belebtschlammbecken an, von denen derzeit drei aktiv sind. Die Becken sind 5 m tief und fassen jeweils 6500 m³. Hier finden im Wechsel die aeroben und anaeroben biologischen Abbauprozesse statt, in deren Rahmen Kohlenstoff, Stickstoff und Phosphat aus dem Abwasser eliminiert werden. Im Anschluss an die biologische Reinigungsstufe durchläuft das Wasser die Nachklärung und fließt dann über die sogenannten Schönungsteiche in den Vorfluter – die Oder. Der Überschussschlamm aus der Nachklärung wird eingedickt und gemeinsam mit dem Primärschlamm aus der Vorklärung behandelt. Der Schlamm fault etwa 30 Tage unter Luftabschluss und der Mitwirkung von Bakterien aus. Dabei entsteht Methangas, das im BHKW in Strom und Wärme umgewandelt wird.
Biologie trägt mit 55 % zum Gesamtenergieverbrauch bei
Die biologische Reinigungsstufe verbraucht ungefähr 55 % der insgesamt auf der Anlage benötigten elektrischen Energie, davon entfallen wiederum rund 80 % auf die Gebläse für die Beckenbelüftung. Bis zu ihrem Umbau gelangte der für die aeroben Abbauprozesse notwendige Sauerstoff über Tellerbelüfter in die Becken, die damals noch in aerobe und anaerobe Zonen unterteilt waren. Die neuen Plattenbelüfter wurden auf der gesamten Grundfläche der Belebungsbecken installiert und versorgen die Biologie nun intervallweise mit Sauerstoff, so dass sich aerobe und anaerobe Prozesse im kompletten Becken abwechseln. Darüber hinaus übernehmen die Belüfter die Durchmischung und ersetzen so die energieintensiven Rührwerke in den anaeroben Zonen. Ebenso die Zirkulationspumpen, die für die Rückführung von nitratreichem Belebtschlamm in die anaerobe Zone zuständig waren.
„Unsere früheren Turbogebläse kamen hier mit einem Maximaldruck von 610 Millibar an ihre Grenzen“, erinnert sich Börner. Man habe die Anlage damals in einem Druckband von 580 bis 610 mbar gefahren, aber dieser Druck habe mit den neuen Plattenbelüftern und dem neuen Regelsystem nicht mehr funktioniert. „Denn seit wir nicht mehr mit Rührwerken, sondern mit der Druckluft durchmischen, brauchen wir vor allem in der Einlaufzone einen höheren Druck.“ In der Folgezeit setzten sich die Platten in diesen Zonen immer mehr zu, und die Biologie lief Gefahr, nicht mehr optimal mit Sauerstoff versorgt zu werden. „Parallel ging der Energiebedarf wunderbar nach unten“, beschreibt Börner ironisch den schleichenden Prozess, „denn je mehr Schlamm auf den Platten lag, desto höher war der anliegende Druck, und die über Diffusoren geregelten Gebläse haben ihre Leistung runtergefahren. Wäre das weiter so gelaufen, wäre uns die Anlage irgendwann umgekippt.“
Magnetgelagerte Turbos überzeugen mit Effizienz und wenig Wartungsaufwand
Aus diesem Grund entschloss man sich, die Druckluftversorgung an die neue Beckenbelüftung anzupassen. Zunächst sollte Atlas Copco einen sogenannten AirScan durchführen, in dessen Rahmen der genaue Druckluftbedarf festgestellt wurde. Es folgte die Ausschreibung für die neue Gebläsestation, die Atlas Copco mit zwei ölfrei verdichtenden drehzahlgeregelten Turbogebläsen des Typs ZB 110 VSD gewann. Die magnetgelagerten, 110 kW starken Gebläse liefern einen maximalen Überdruck von 1000 mbar. Sie konnten vor allem mit ihrer Effizienz und dem aufgrund der Ölfreiheit minimalen Wartungsaufwand überzeugen. „Es ging uns darum, einen für die neue Belüftungstechnik ausreichenden Druck aufbauen zu können und dabei gleichzeitig eine Technologie zu nutzen, die eine hohe Effizienz zur Verfügung stellt“, erläutert Börner die Auswahlkriterien. „Die Atlas-Copco-Turbos besitzen durch ihre Magnetlagerung einen sehr guten Wirkungsgrad und waren außerdem bezüglich ihrer Lebenszykluskosten am günstigsten.“ Darüber hinaus sei die äußerst geringe Lärmemission der neuen Maschinen ein weiterer Pluspunkt.
Seit Ende 2015 liefern die beiden Turbos nun im wöchentlichen Wechsel einen Betriebsüberdruck zwischen 595 und 635 mbar. Die jeweils andere Maschine steht als Redundanz zur Verfügung. Über ihre integrierte Elektronikon-Steuerung arbeiten die Verdichter direkt mit dem Regelsystem der Plattenbelüfter zusammen. Der komplette Belüftungsprozess ist wiederum ins Betriebsleitsystem eingebunden und wird in der Leitwarte der Kläranlage visualisiert und überwacht. „Von den Belebungsbecken ist rund um die Uhr mindestens eines aktiv“, erläutert Börner die Betriebsweise. „Wenn die Belastung überdurchschnittlich hoch ist, dann werden auch mal zwei Becken parallel belüftet, um die Belüftungszeit zu verlängern. Im Schnitt benötigen wir dafür etwa 4600 Normkubikmeter Druckluft pro Stunde, wobei der Wert zwischen 3100 und 5600 Normkubikmeter pro Stunde schwankt.“
Der Drucksollwert der Gebläse ist über eine in der Regelung hinterlegte Kennlinie an die Ammoniumbelastung im Becken gekoppelt. Der Sauerstoffgehalt im Becken wird dann über Blenden-Regulierschieber geregelt. „Wir geben einen Druck vor, und die Regulier-Schieber öffnen oder schließen, je nachdem wie viel Sauerstoff sich im Becken befindet“, erklärt Börner. „Das ist eine relativ komplexe Regelung, die uns die Rudolf Messner Umwelttechnik AG zusammen mit den Plattenbelüftern geliefert hat.“
Die Installation der beiden Turbos gestaltete sich durch ihr Plug-and-play-Prinzip und die integrierte Elektronikon-Steuerung äußerst einfach. Sie mussten nur an die Stromversorgung, ans Leitsystem und an die Belüftung angeschlossen werden. „Wir mussten keine zusätzliche Steuerung entwickeln“, erläutert Börner. „Die Atlas-Copco-Gebläse brauchen nur einen Strom- und einen Busanschluss sowie einen Druckwert, den wir vorgeben.“ Die Aufschaltung des Bus-Protokolls der Atlas-Copco-Maschinen auf das Betriebsleitsystem von Siemens sei die einzige Herausforderung gewesen; sie habe der Programmierer nach Rücksprache mit den Atlas-Copco-Technikern aber meistern können. Heute läuft die Anlage zu Ronald Börners voller Zufriedenheit.
Schritt für Schritt zum optimalen Betriebsdruck
Nachdem die Prozesssicherheit mit den neuen Turbos sichergestellt ist, wird derzeit am optimalen Betriebsdruck und somit an der Effizienz der neuen Druckluftversorgung gearbeitet. Denn nach der Umstellung stieg der Energieverbrauch der Gebläsestation aufgrund der notwendigen Druckerhöhung zunächst an. „Der mit der Umstellung gestiegene Energieverbrauch resultierte aber auch daraus, dass wir den Druck über einen längeren Zeitraum über die Maßen erhöht haben, um das Blasenbild in den Becken wieder in Ordnung zu bringen“, erklärt Börner. Derzeit taste man sich von oben langsam wieder an einen Punkt heran, an dem die Durchmischung funktioniere und man gleichzeitig energetisch sinnvoll fahre.
Hierbei sei durch die Beckentiefe und die Plattenbelüfter eine natürliche Grenze nach unten gesetzt. „Energetisch gesehen bieten uns die drehzahlgeregelten Turbos bereits das Optimum, und mit einem Anteil von 40 Prozent am Gesamtenergieverbrauch sind wir mit unserer Gebläsestation sehr gut aufgestellt“, ist Ronald Börner überzeugt. Die jährlichen Energieeinsparungen schätzt der Ingenieur auf mindestens 5%. Das entspricht etwa 50000 kWh oder 8.500 Euro. „Aber das wichtigste Kriterium bei der Erneuerung der Druckluftversorgung war die Betriebssicherheit unserer Anlage“, sagt Börner, „also der höhere Druck für unsere Plattenbelüfter und die Fähigkeit der Gebläse, Druckspitzen und Belastungswechsel besser zu verkraften als unsere Altanlage.“
Als weitere Maßnahme zur Effizienzmaximierung wurde bereits über eine Wärmerückgewinnung aus den Gebläsen nachgedacht. Derzeit fehlt hier aber noch ein permanenter, ganzjähriger Abnehmer, der den Aufwand rechtfertigen würde. „Dies könnte in Zukunft beispielsweise eine interne Schlammtrocknung sein“, erläutert Börner, „denn seit Januar 2017 steht ein Regierungsbeschluss, der das Ausbringen von Klärschlamm in der Landwirtschaft bis 2030 schrittweise beenden will. Dann muss der Schlamm getrocknet und verbrannt werden.“
In puncto Energieautarkie wird die Abwasserreinigungsanlage bereits im kommenden Jahr noch einen Schritt weiter sein. „Dann werden wir eine große Photovoltaikanlage auf den Dächern installiert haben, die unser Blockheizkraftwerk sinnvoll ergänzt“, blickt Ronald Börner in die Zukunft. „Das 16 Jahre alte BHKW werden wir noch in diesem Jahr erneuern. Davon versprechen wir uns eine weitere Verbesserung des elektrischen Wirkungsgrades.“
Quelle: Atlas Copco Holding GmbH