Custom-Fabricated Structural Bearings for High Stress Applications
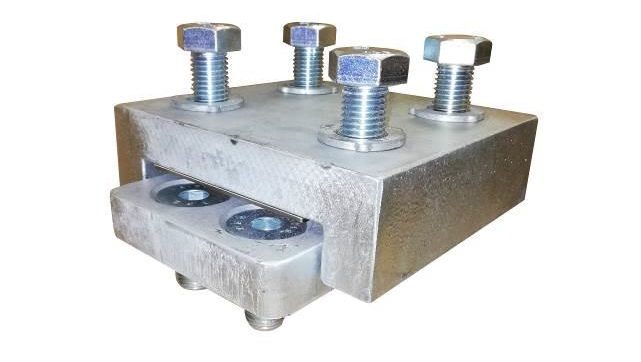
H-Glide technolgy is being incorporated into Herculon structural bearings custom-fabricated for extreme loads. The material is proven internationally. (Image source: Hercules Engineering)
Custom-fabricated structural bearings are being introduced by Hercules Engineering for extremely high stress applications in resources projects requiring outstanding load-bearing performance, even in compact or wet spaces in mineral processing applications, power generation, ports loaders and land and marine exploration and structures .
The latest Herculon structural bearings are manufactured by integrating H-Glide fibre-reinforced composite pads sliding on 2B finish stainless steel to achieve an exceptionally low sliding coefficient of friction compared with other engineering bearing materials, even under water.
Unlike metal bearings that may rust or require continual lubrication and maintenance, the environmentally safe yet hard-wearing H-Glide bearing pads are dry sliding and will not release contaminants into surrounding environments or adjacent processes.
“H-Glide’s excellent sliding properties (including friction coefficients from 0.05 – 0.1) are invaluable to infrastructure developers, engineers, architects and specifiers because lower coefficients of friction will transfer less stress onto the load-bearing structural components when the bearing does its job of protecting them against surrounding movement, says Mr David Booty, Manager, Hercules Engineering (a division of Cut To Size Plastics Pty Ltd).
Hercules Engineering and Cut To Size Plastics provide a wealth of experience and application guidance, based on almost 50 years of operation in Australasian and Asia-Pacific regions in applying engineering polymer technology to construction, infrastructure, energy, mining, manufacturing, maritime, oil and gas, food and beverage, safety and water and wastewater applications.
Hercules Engineering’s latest example of bearings incorporating H-glide was in an extensive roof which required extreme load-bearing capacity in a confined space, as close as possible to the axis of the load. The same high performance is equally useful in major energy and resources structures, including wharves, platforms and steel structures, where compact bearings must withstand long-term stresses to protect valuable structures with optimum levels of safety for those within or around them .
“With their incompressible H-Glide sliding layer, these bearings can withstand extreme point pressures of 350-500 megapascals, depending on bearing design and application,” says Mr Booty.
“This outstanding performance – which is up to 40 times greater than conventional water-resistant and non-lubricated fibre-reinforced elastomeric bearing pads – is complemented by the material’s ability to function well in a variety of environments including, but not limited to, damp or under water applications. It is suitable for:
- Oil process and production platform applications, as well as resource development infrastructure and mineral processing plants subject to changing operational loads and ambient conditions
- Maritime and logistics structures, port and rail facilities, water and wastewater environments requiring a combination of high engineering performance combined with environmental compatibility
- Energy structures, including wind, wave and tidal power generators, where bearings must provide outstanding performance over varying loads for extended periods.
- Industrial and manufacturing process plant, including food and beverage, plant and process engineering applications requiring low maintenance, with high requirements for safety and hygiene
- Construction, infrastructure, engineering and architectural projects involving high point loads on bearings, including commercial, retail and public infrastructure ranging from health facilities to parking stations
“A major advantage of this type of composite bearing is that they do not require lubrication, which minimises any disruption to processes,” says Mr Booty. “H-Glide bearings’ already excellent lifespans can be increased by the use of a mirror polished stainless steel sliding plate. “Absorption of water and other fluids is negligible. The material is virtually inert, reactions with food and cleaning substances, for example, almost never occur,” says Mr Booty.
The company’s standard ranges of Herculon™ structural bearings and Hercuslip™ composite slip joints are widely proven product designs that have performed over decades since 1972 in applications ranging from landmark metropolitan construction projects, through to major international industrial and resources projects. The new custom bearings that incorporate H-Glide are a new extreme performance addition to Hercules Engineering’s easily installed and cost-effective range of products that gives architects, engineers and specifiers a high performance and more durable bearing option.
The H-Glide bearing pad is available in different formulations, including conductive materials. It is equally suitable for a wide variety of high-load structures requiring extreme load-bearing capability combined with non 'stick-slip' behaviour, where static and kinetic coefficient of sliding friction are virtually equal.
“By using new generation composite formulations, H-Glide bearings allow the highest loads, with ultra-low wear rates and friction values,” says Mr Booty. “The material is resistant to a majority of common industrial chemicals and environments, whether it is immersed in water or used in dry applications, or anywhere in between, from freezing to tropical conditions.”