Wastewater treatment in the Swiss Alps with technology from AERZEN
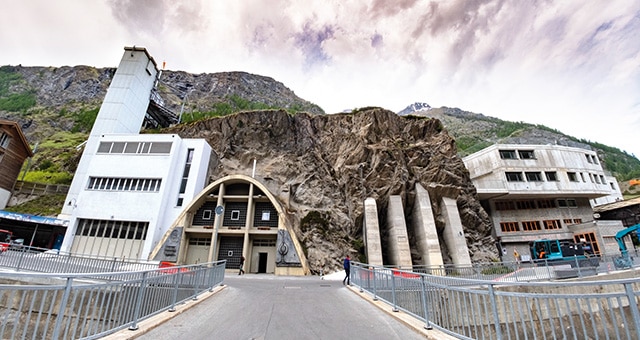
Not much to see: the Zermatt wastewater treatment plant clings to the Alpine massif unobtrusively. Behind the door, state-of-the-art process technology is revealed. (Image source: Aerzener Maschinenfabrik GmbH)
Zermatt lies in a narrow valley, called the Mattertal. “The wastewater enters the treatment plant from both sides of the valley,” says Beni Zenhäusern, Production Manager. The street that runs in front of the entrance portal to the ARA Zermatt therefore has an underground cellar. The computer system and the sand-grease collector are installed here. “A pumping station delivers the pre-treated wastewater 11 meters upwards, before it is separated into two identical treatment lines.”
Zermatt is a phenomenon in wastewater technology. This place has only 5,600 inhabitants. However, the treatment plant has a capacity of 76,000 population equivalents (EEC). Some background to this: During the peak season in winter and summer, dirt loads arrive that reach a chemical oxygen demand (COD) of 60,000 for complete degradation. A COD value of 60,000 EEC corresponds to that of a medium-sized city. The high freight volume and the enormous COD value for wastewater treatment can be explained by the discharge gastronomy.
Energy-optimised and standardised blower technology
Biology lies further inside the Alpine massif. The two basins of denitrification are connected in a Y-shape to two filter lines, which are functionally part of nitrification. Five filter cassettes form one filter line. Each cassette has 48 hollow fibre units. For the necessary oxygen supply, ARA Zermatt uses identical AERZEN Delta Blower machinery in two blower rooms. Five positive displacement blowers, type GM 50 L (max. 90 kW, 3.300 m³/h, max. 700 mbar) are installed. These fifth generation blowers from AERZEN are energy-optimised and deliver up to 50 standard cubic meters per minute with an engine power of 45 kW. A special feature of the design was that Zermatt lies more than 1,600 metres above sea level. This has a corresponding effect on the density of the air sucked in. The significant temperature differences between winter and summer also pose a challenge.
From each of the two machine rooms, two Delta Blowers supply the nitrification with sufficient oxygen. Two more Delta Blowers are assigned to the diaphragm filter. “The hollow fibres must always stay in motion during operation. We do this with air,” Zenhäusern notes. The remaining fifth blower is mainly assigned to the filter as a reserve, but can also be used for nitrification via a corresponding slide valve position. This design, with identical machinery, makes the power distribution of the blower air flexible, and, as a result of standardisation, reduces the cost of spare parts.
ARA Zermatt works closely with Aerzen Switzerland on service and maintenance issues with regard to operational safety. Michael Schüpbach, the head of the Service Centre in Frauenfeld, south of Lake Constance, has drawn up a revision plan for all blower packages for the wastewater treatment team.
Diaphragm filters are also important in connection with operational reliability and long-term availability. After ammonium nitrate degradation, they separate the activated sludge from the biologically purified water. The water is sucked through the diaphragm into the interior of the hollow fibres by vacuum. The pressure difference is generated by a rotary piston pump. The air from the blowers acts as continuous coarse ventilation. This is necessary to keep the diaphragms moving, as the diaphragm openings only measure 0.04 micrometers, which is too small for bacteria. Therefore, the diaphragms would clog immediately if the air-water flow fails.
In total, underground biology has a filter area of 32,500 square metres. This is roughly the size of 4.5 soccer pitches, and it all happens in the smallest of spaces. Adding up the hollow fibres, their total length of around 5,000 kilometres would stretch from Zermatt to Dubai. “We make a living from tourism,” says Beni Zenhäusern. For this, the town has invested in a wastewater treatment plant which has ten times more capacity than the population actually needs. In addition, there are the strict wastewater regulations. Whereas in Switzerland the limit value is 0.8 mg. phosphate per litre, in Zermatt it is only 0.5 mg due to the receiving water. In view of these constraints, the wastewater treatment plant in Zermatt exclusively uses technology which meets the highest demands on availability. AERZEN holds the position of manufacturer and partner at the same time - in addition to providing pure technology, the company also passes on its know-how over the entire life cycle.
Source: Aerzener Maschinenfabrik GmbH