Special Design for Viscous Media Reduces Wastewater Treatment Plant Downtime
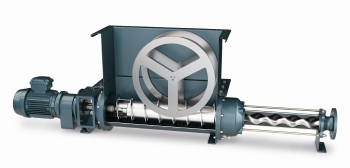
Nemo BF progressing cavity pump with integrated aBP-Module reduces sewage sludge bridge building. (Image source: Netzsch Pumps & Systems)
Designed for viscous media, the pump with the aBP-Module eliminates high media cohesiveness that can cause repeated entanglements and bridge building. The result is significant reduction or elimination of wastewater treatment plant operational shutdowns.
The aBP-Module is made up of a hopper extension with two spoked wheels attached to its internal sides. Sitting deep inside the hopper and very close to the walls, the turning wheels generate the effect of moving hopper walls, which creates a shearing effect in the medium. This shear effect tears the bridges apart in the early stages of formation, so the mix can be conveyed continuously. The structured surface of the stainless steel wheels further supports this effect and assists agitation in the hopper. The middle of the chute remains free, and the fill level can be assessed at any time and readjusted if necessary. The wheels are driven by independent worm gears with settings that can be tailored to each medium being conveyed. To convey larger quantities to a wastewater treatment plant, the aBP-Module is also available in a version with four wheels, two on each side.
The Nemo BF progressing cavity pump was specially developed for highly viscous to compacted media and ensures pressure-stable, low-pulsation conveyance. Sewage sludge drops directly out of the hopper chute into the force-feed chamber. As the dewatered, flocculated sludge is no longer free-flowing, it is moved evenly via the aBP-Module’s patented, horizontally positioned screw conveyor into the pump chamber itself.
Between the progressing cavity pump s rotor and stator, equal cavities are formed that take up the medium and transport it on with the turning of the rotor. In this process, dosing can be precisely controlled by the speed to achieve a continuous material flow. The filling of the conveying cavities is supported by the hopper-shaped inlet, which is already established in the shaping of the stator.
Depending on the size, the Nemo BF can achieve pumping capacities of up to 52,830 gallons per hour (gph) and differential pressures of up to 652.67 pound-force per square inch (psi).