Retrofit o sostituire? Alla scoperta del risparmio per il settore degli idrocarburi
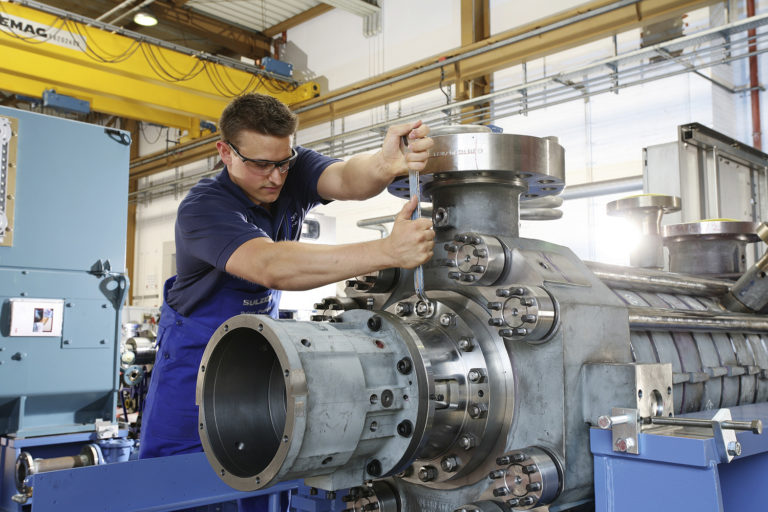
Elaborazione chimica
In quanto risorse importanti, devono fornire un servizio affidabile pur rimanendo efficienti. Con una maggiore attenzione ai costi operativi, ridurre il consumo di energia ove possibile è sempre più importante ed è anche uno dei compiti che possono essere raggiunti attraverso un progetto di retrofit.
Luca Lonoce, specialista di retrofit per Sulzer, esamina i vantaggi dell'utilizzo della tecnologia di retrofit per soddisfare le mutevoli esigenze del settore della lavorazione degli idrocarburi.
Anche se la maggior parte delle persone non li vedrà mai, le pompe industriali ei compressori sono parti cruciali della vita quotidiana. Gli impianti petroliferi, di gas e chimici utilizzano pompe e compressori per il trasporto e la lavorazione; creando carburante e materiali su cui tutti facciamo affidamento. Questi pezzi vitali dell'attrezzatura rotante aiutano a mantenere le nostre vite scorrevoli.
L'industria della lavorazione degli idrocarburi presenta un ambiente difficile per le apparecchiature rotanti in cui pompe e compressori devono gestire fluidi e gas che possono contenere solidi, il che può avere un effetto negativo sulle prestazioni. I cambiamenti nella materia prima, nei parametri di processo e nelle considerazioni operative possono tutti influire sulle richieste fatte su molte risorse nell'ambiente di produzione.
Le moderne apparecchiature rotanti sono progettate e prodotte per funzionare all'interno di piccole finestre operative, il che significa che c'è una tolleranza minima per i cambiamenti nelle prestazioni della materia prima. Le apparecchiature più vecchie hanno una maggiore tolleranza al cambiamento, ma hanno anche lo scopo di accogliere modifiche nel design del rotore senza influire sulla custodia esterna.
Pertanto, quando sono necessarie modifiche al design, sia per problemi di prestazioni che di affidabilità, gli impianti spesso hanno solo due scelte: investire in un nuovo asset, che può avere un tempo di consegna prossimo a due anni, o sviluppare un progetto di retrofit che adatterà il design esistente per soddisfare i parametri desiderati - una scelta che riduce notevolmente i tempi di progetto.
Compressori
Valutazioni iniziali
Il processo inizia con una valutazione iniziale per determinare l'idoneità delle apparecchiature per la rerating utilizzando un processo sistematico che considera le condizioni operative esistenti e richieste. Nel caso di un compressore, i dati minimi necessari per questa prima revisione sono la pressione di ingresso, la temperatura, la portata, l'umidità relativa e le proprietà del gas (compressibilità, peso molecolare e capacità termica specifica) per ciascuna condizione. La pressione finale desiderata è l'unico valore richiesto per il lato di mandata.
I calcoli iniziali forniscono le temperature di scarica, i requisiti di alimentazione e la velocità di rotazione. I dati calcolati vengono confrontati con le misurazioni effettive sul campo o con i record operativi e regolati per abbinare efficienza, velocità e potenza. Il confronto del nuovo punto operativo con i dati operativi originali del compressore determina l'entità delle modifiche richieste.
Le dimensioni degli ugelli di ingresso e di uscita determinano i limiti finali per l'involucro e l'area disponibile per il passaggio del flusso di volume aumentato senza soffocare o superare i limiti di velocità consentiti. Se l'involucro è in grado di gestire i nuovi requisiti di flusso, può iniziare la valutazione dettagliata.
Modifiche al design
Una semplice equazione regola la portata e le tre quantità che possono essere modificate per aumentare la portata volumetrica: area di flusso, velocità di flusso e densità del gas.
Portata = Area del flusso x Velocità del flusso x Densità del gas
La modifica dell'area di flusso è il metodo più complesso per aumentare la portata. Questa misura implica un nuovo assemblaggio aerodinamico comprendente giranti, diaframmi e parti strutturali. Un aumento dell'area di flusso è ottenuto da giranti più larghe, giranti con diametro maggiore, nuovi design delle pale della girante, passaggi del diffusore più grandi o una combinazione di tutti questi. A condizione che le nuove parti si adattino al vecchio spazio dell'involucro, il progetto è fattibile.
Le moderne tecniche di progettazione, come la fluidodinamica computazionale (CFD) e le tecnologie di produzione, hanno consentito la produzione di profili tridimensionali delle pale della girante. Questi hanno notevolmente aumentato la superficie attiva della lama, che fornisce maggiore velocità e capacità volumetrica a ogni fase, nonché una migliore efficienza.
In effetti, i miglioramenti sono tali che tre stadi che utilizzano un design 3-D possono sostituire un rotore a quattro stadi dotato di giranti bidimensionali e fornire la stessa potenza utilizzando fino al 10% in meno di energia. Allo stesso modo, la produzione può essere aumentata rispetto alle cifre originali senza dover modificare le dimensioni esterne o le apparecchiature circostanti e tutto ciò può essere ottenuto durante una finestra di manutenzione programmata.
Miglioramento delle prestazioni
La velocità del flusso viene migliorata aumentando la velocità di rotazione dell'unità o il diametro della girante. Le sezioni stazionarie del compressore convertono la maggiore velocità del gas all'uscita della girante in una prevalenza maggiore, che dà lo stesso risultato di un aumento del coefficiente di flusso effettivo.
Un aumento dell'1% della velocità equivale a un miglioramento della portata del 3%, con la resistenza meccanica delle parti rotanti e le tolleranze di montaggio delle giranti e degli accoppiamenti che determinano i limiti del progetto finale. Tutti questi calcoli e valutazioni possono essere effettuati durante la fase di pianificazione del progetto per determinare il progetto più fattibile che fornirà il risultato desiderato.
Pompe
Miglioramenti dei materiali
Per le pompe, sia monostadio che multistadio, i retrofit seguono un percorso molto simile in termini di valutazione e modifica del progetto. Le pompe a barilotto hanno chiaramente molti aspetti di progettazione in comune con i compressori, mentre le pompe centrifughe monostadio possono trarre vantaggio dal moderno design della girante 3-D e dall'uso del CFD per stabilire un design più efficiente.
Determinare il miglior design e miglioramenti dei materiali per un design originale richiede una notevole esperienza. Tuttavia, ciò deve essere contestualizzato con l'applicazione più ampia, considerando i requisiti di alimentazione, i progetti di accoppiamento e di tenuta, nonché l'impatto sulle apparecchiature a valle dell'asset stesso.
Diagnosi dei guasti
Esempio 1: pompa diesel idrotrattata a caldo.
Una pompa back-to-back a 8 stadi, che produce 193 m3 / h (708 gpm) a una prevalenza di 1'143 metri (3'750 piedi) con un intervallo di temperatura di esercizio di 10-230 ° C (50-446 ° F) stava mostrando una perdita di prestazioni nel tempo quando un guasto imprevisto ha causato la fuoriuscita del fluido di processo nell'atmosfera. È stata eseguita un'analisi della causa principale (RCA) per determinare l'azione correttiva più appropriata.
La pompa era dotata di parti soggette ad usura in polimero, progettate per funzionare con giochi più stretti, migliorando così l'efficienza ed eliminando il rischio di usura metallo su metallo. Tuttavia, RCA ha rivelato che una boccola in polimero ad alta pressione era estrusa dal suo fermo, il che ha causato una pressurizzazione eccessiva della tenuta meccanica.
Diverse opzioni per riparare la pompa erano a disposizione della raffineria, che ha deciso di eliminare completamente il rischio di un guasto ripetuto adottando materiali ceramici per le boccole ad alta pressione. Le parti in ceramica di zirconia solida sono state selezionate per le boccole fisse, mentre gli anelli di usura e le parti rotanti hanno applicato rivestimenti ceramici spruzzati termicamente.
Le parti e i rivestimenti in ceramica offrono un'elevata resistenza meccanica, un'eccellente resistenza all'usura e all'abrasione nonché un coefficiente di espansione simile all'acciaio al cromo, che eliminerebbe il rischio di compromissione dell'accoppiamento con interferenza. Pertanto, il retrofit delle parti in ceramica ha offerto una soluzione molto migliore per l'applicazione e ha garantito che la pompa avrebbe continuato a funzionare in modo affidabile ed efficiente per gli anni a venire.
Esempio 2: aumento della produzione di raffinerie
Una raffineria stava esaminando la possibilità di modificare una pompa a barile di grandi dimensioni da 38'000 bpd a 43'000 bpd e di aumentare la prevalenza da 1'420 m (4'600 ft) a 1'798 m (5'900 ft) , senza superare la potenza massima del motore esistente. Inoltre, il progetto prevedeva di includere un aggiornamento dall'API 610 6a edizione all'API 610 8a edizione per garantire la conformità con gli attuali standard di settore.
Per ottenere il risultato desiderato, la cassa interna e le giranti a bassa capacità sono state sostituite con componenti ad alta capacità, pur mantenendo la canna originale. Il progetto è stato completato in modo tale da garantire che la portata e l'altezza richieste fossero fornite entro le capacità del motore di azionamento esistente.
Questa soluzione economica richiedeva un investimento notevolmente inferiore rispetto a un nuovo asset della pompa, che avrebbe richiesto modifiche aggiuntive alla piastra di base e alle tubazioni di aspirazione e scarico. Anche la ripetizione è stata completata in un lasso di tempo molto più breve rispetto a un progetto di sostituzione.
Soluzioni all'avanguardia
Esempio 3: estensione della durata del rotore del compressore
Un cliente nel settore petrolchimico stava riscontrando problemi di prestazioni con un turbocompressore a ossido di etilene a tre stadi che necessitava di un'estensione della sua durata operativa. Il progetto richiedeva un alto livello di precisione nella produzione per creare tutti i componenti necessari.
Era necessaria una considerevole esperienza di produzione per decodificare la geometria della girante e la conoscenza dei materiali per ottenere il necessario adattamento a caldo delle giranti. La combinazione di competenza nelle turbomacchine, esperienza di progettazione e tecnologia di saldatura laser ha consentito di creare nuovi componenti con tempi di consegna minimi.
La capacità di eseguire il rivestimento laser ed eseguire il bilanciamento ad alta velocità del rotore è stata fondamentale per la fornitura di un rotore e una girante di precisione che hanno allungato notevolmente la durata del compressore.
Retrofit e riparazione
Sebbene, in circostanze ideali, i progetti di retrofit siano completati durante i periodi di manutenzione programmata, possono anche offrire una soluzione conveniente in caso di guasto. Quando i tempi di consegna di nuove parti ritardano in modo significativo un progetto di riparazione, un progetto di retrofit ha la capacità di ridurre i tempi di fermo e fornire una maggiore affidabilità per il futuro.
Utilizzando tecniche di reverse engineering, abbinate a processi di produzione rapidi, inclusa la produzione additiva, è possibile creare parti di precisione che corrispondono, o addirittura superano, le specifiche del produttore di apparecchiature originali (OEM). Collaborando con fornitori di manutenzione esperti, in grado di raccogliere rapidamente tutte le conoscenze e le risorse necessarie, gli operatori possono ottenere tempi di inattività ridotti nonché una maggiore affidabilità e produttività.
Competenza nel settore
Per fornire una soluzione chiavi in mano per il petrolio a valle & amp; settore gas, sono richieste molte aree di competenza, non ultima una conoscenza approfondita del settore e delle applicazioni in cui opera l'attrezzatura rotante. Insieme a capacità di progettazione specializzate, risorse di produzione e strutture di collaudo, è possibile fornire soluzioni ingegneristiche all'avanguardia che combinano affidabilità, efficienza e prestazioni, senza le implicazioni di tempo e costi associate a nuovi investimenti di asset.
Fonte: Sulzer Ltd.