Regulator and Air-Actuated Valve Team Up to Eliminate Pressure Fluctuation
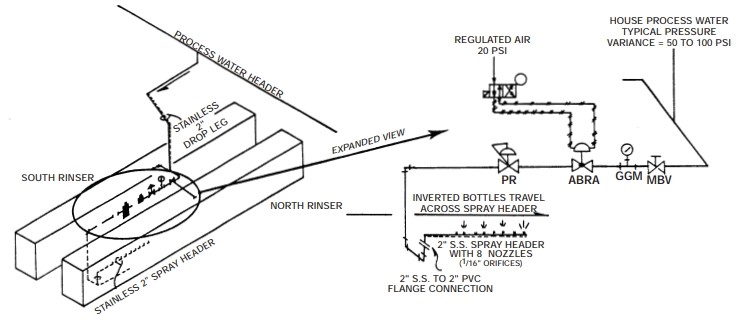
Regulator and Air-Actuated Valve Team Up to Eliminate Pressure Fluctuation at Craft Brewery (Image source: Plast-O-Matic Valves, Inc.)
Usually, a final rinse of RO water ensures that any potential residue from the bottle cleaning and purification process will be removed before filling. It also rinses out any airborne particles that might detract from the intended flavor. Problem is that fluctuating demand on other cleaning lines can result in overpressure as high as 150 PSI / 10.3 Bar that blows bottles off the line, or low pressure that fails to clean.
By using a Plast-O-Matic Pressure Regulator and Air-Actuated Ball Valve at each rinse station, pressure can be maintained safely throughout the bottling operation. The regulator is an automatic, spring-controlled valve that converts varying inlet pressure to a constant, lower downstream pressure. By installing a regulator at each point of use, high pressure surges - and resulting drops elsewhere - are eliminated across the plant.
This type of rinse process isn't limited to beverage bottling; packaging systems from healthcare to specialty chemical benefit from the same technology.
Source: Plast-O-Matic Valves, Inc.