Progressive Cavity Pumps Reduce Costs for Digesting Residual Sludge
Operators looking for the most reliable, low-maintenance and efficient solution for discharging digested residual sludge at a sewage plant in Germany recently began a comparison of an inclined conveyor versus four-stage progressive cavity pumps.
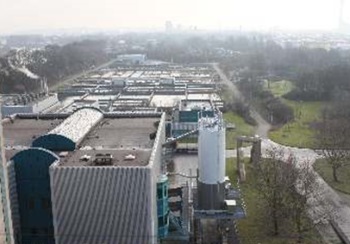
Plant showing sludge silos
The results show that use of the progressive cavity pumps helped the plant save significant amounts of energy and lower maintenance costs, while simultaneously reducing downtime compared to an inclined conveyor.
Sewage plant looks for cost reduction and high availability
The Duisburg-Kasslerfeld sewage plant serves a large catchment area in western Germany. Approximately 50 percent of the wastewater volume comes from households, with the remainder from a variety of industrial operations, including tank cleaning, beverage production, and the Duisburg zoo.
The sewage plant is designed for 450,000 resident equivalent units; its dry-weather inflow is approximately 1.3 cubic meters per second (m3/s) and rainy-weather inflow is up to 4.1 m3/s. In recent years, the plant operator replaced the chambered filter presses with two centrifuges. In the next step, the best possible methods for discharging the dewatered sludge should be determined. The operator decided to compare reliability and economic efficiency of two methods: a centrifuge with an inclined conveyor and a centrifuge with a progressive cavity pump. The pump solution could operate 24 hours per day, which would lower costs.
The residual is stored in two silos before being transported for incineration. The picture shows the two feed tubes into the residual sludge silos. In the front silo, an inclined conveyor moves sludge from the top; in the rear silo, a pump moves it from the bottom.
Comparing progressive cavity pump with inclined conveyor
Ruhrverband, the non-profit water management company that operates the plant, decided to test the performance of Allweiler AE-RG series four-stage solid-substance progressive cavity pumps as the residual sludge discharge pump. About 80 percent of all pumps in the plant are from Allweiler, including progressive cavity pumps for pumping excess sludge, primary sludge, and polymers, as well as for digestion treatment operations.
Ralf Wilms, Ruhrverband’s regional operational group leader, notes, “We wanted to know whether a discharge pump would be a more economical and reliable solution than a conventional inclined conveyor.”
The sludge contains approximately 25 percent dry substance, and the selected AE-RG four-stage progressive cavity pump has several design characteristics that ensure reliable continuous operation with such a high proportion of dry substances. Two force-feed screws arranged in parallel next to each other ensure continuous operation. A wide feed funnel that prevents bridging of the material is another important element to ensure movement of the sludge and disturbance-free operation of the plant. This special pump design does not require a bridge breaker, and the pump’s design height is significantly smaller than similar pumps. Even when starting, there are no disturbances because the break-out torque (starting torque) is very low. The pump is controlled by a frequency converter and runs at 30 to 60 Hertz (Hz). The low rotational speed helps the pump achieve a long service life.
The pumps can move drained sludge with dry substance proportion of up to 45 percent. The two edge-to-edge feed or mixing screws in the feed funnel and the extra-long stuffing housing ensure reliable filling of the pumping elements without bridging or formation of deposits.
Progressive cavity pump wear and maintenance costs lower than inclined conveyor
Since starting operations, wear and associated maintenance costs for the four-stage progressive cavity pumps are significantly lower than those of the conveyor. In addition, the pump requires about 4 to 5 kilowatt/hour (Kw/h) less energy than the conveyor. The pump moves a daily volume of approx. 55 m³ of sludge with a dry substance proportion of approximately 25 percent. Pressure ranges from 4 to 9 bar (58-87 pounds per square inch (psi)). Maximum discharge pressure is about 20 bar (290 psi), so the plant’s silo can be completely filled with no difficulty.
In addition to lower energy consumption, the plant has also reduced its spare parts and maintenance costs. As one of only a few manufacturers that make its own stators and rotors, Allweiler can offer 17 different stator elastomers. This means operators can find the combination that best matches the pumped liquid’s chemical and physical characteristics. This results in the longest possible service life – with long maintenance intervals, minimal downtime, and very reliable, continuous operations.
The plant operator has found significant benefits from using original Allweiler spare parts due to their significantly greater durability. Repair, assembly, and technical consultation services have also proved valuable. In particular, if conditions in the plant change or if pumps will be used in other processes, the manufacturer recommends the materials that will have the longest service life and the configuration with the greatest efficiency.
For example, when a new flocculent is used, a durability test is conducted with several different elastomers to determine the mixture that is precisely adapted to the conditions. According to Heinz-Peter Sildatke, the plant’s manufacturer’s representative, “Getting the right combination of elastomers for the chemical and physical properties of the liquid is one of the consultation services that pays real dividends.”
Proven results
As of November 2018, the Allweiler AE-RG pump on centrifuge 1 has been in operation for more than 20,000 hours, with one change of stator at approximately 9,300 operating hours and the first service at 16,000 hours. The pump on centrifuge 2 has been operating since January 2018 without maintenance and no failure in operation. The manufacturer anticipates that the pump will complete up to approx. 20,000 operating hours before needing overhaul. Concludes Ralf Wilms, “The progressive cavity pump has really proven itself.”
Source: ALLWEILER GmbH