Progressing Cavity Pump MX Stands Up to Even Aggressive Cleaning Media
Knoll Maschinenbau has developed an elastomer and joint-free variant of its proven MX progressing cavity pump. Robust PTE is used for the stator and the secondary seals, which means that neither colors and paints that contain solvents nor aggressive detergents can harm the pump.
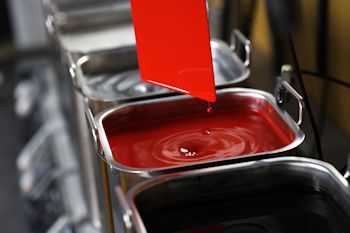
The renowned long-established company FreiLacke, Bräunlingen, in the Baar region of the Black Forest, has more than 85 years experience in the development of innovative colors and paints, and also broad expertise in various industries, and with many applications, manufacturing processes, and requirements. For brilliant colors, optimal gloss, and perfect structure on all surfaces, the company offers a branded component system in which all important paint technologies (powder, liquid, electrodisposition, and Durelastic) come together harmoniously and are used in perfect coordination with one another.
However, so that colors and paints can be used to finish a wide variety of surfaces, a lot of knowledge of the manufacturing and handling of these media is required. For example, the pumps used enjoy great attention, for they must perform well and prove resistant to chemicals. When searching for an optimal pump for conveying and filling colors and paints, the people in charge at FreiLacke made contact with the pump specialist Knoll Maschinenbau, Bad Saulgau. The special design features of the MX progressing cavity pump had piqued their interest.
Design Principle Enables High Performance Level
The essential feature of this pump is its use of the EvenWall technology, which differs considerably from conventional designs. With EvenWall the stator sheathing is adapted to the contour of the rotor, and - in the standard model - it has an elastomer coating with an even wall thickness. This provides numerous benefits as compared to conventional designs that feature a cylindrical exterior geometry of the stator sheathing and accordingly varied wall thicknesses of the elastomer. The MX progressing cavity pump achieves much greater pressure stability, less backflow, longer durability, better efficiency, less shearing of the product, and better suction behavior. In addition, with a closed chamber, the MX pump provides pressure of at least 10 bar, while conventional progressing cavity pumps are limited to 4 to 6 bar.
This standard variant is suitable for many areas of application. During the manufacturing of colors and paints, special conditions prevail, which do not permit the use of elastomers on the stator and for the shaft seal. The cause: precisely during the manufacturing of colors, frequent cleaning procedures are required, at least with each change of product or color tone. The mixture of solvents used is collected, treated, and thus changes its composition and concentration. These chemically-aggressive components make the elastomer swell and render the pump unusable.
Special MX Model
The solution: FreiLacke needs an elastomer-free progressing cavity pump - a challenge for Knoll, one that this pump specialist gladly takes on. In order to fulfill the customer s needs, Knoll modified the vertical MX20T submersible pump. A special model was developed, one that contains a solid stator made of PTFE. This plastic, known by its brand name Teflon, is a material with great chemical resistance; it reacts only very slowly and can be used up to 260 °C. It even stands up to the frequent use of aggressive detergents.
In addition, the MX 20T progressing cavity pump used at FreiLacke is joint-free. A titanium member that balances out the eccentric motion of the rotor and eliminates the need for cardan joints ensures this. Since the rotor and drive shaft are shrunk on the titanium member, it is possible to avoid elastomer seals here too. This way, only VA steel and the sealing material PTFE come into contact with products and detergents inside the pump.
The MX progressing cavity pump achieves the required chemical resistance yet still maintains the typical Knoll properties. These include easy servicing and cleaning (CIP and SIP) as well as very good pump behavior. The pulsation is low, the pressures that can be achieved are high. In addition, the pump is suited for high viscosities.
Simon Reichhardt, Assistant Technical Manager at FreiLacke, praises the MX20T as a successful development achievement: "Knoll Maschinenbau has addressed our needs admirably with this special design. We have been using these progressing cavity pumps for two years already, and we can gladly confirm their outstanding performance data and their chemical resistance." He also points out that for this special design, Knoll paid attention to ensuring that the modular nature of all essential components was maintained. Thus FreiLacke can adapt its pump to changing conditions in the manufacturing process as necessary.
Properties of the MX
- Intelligent separation points for easy disassembly
- Maximum chamber utilization
- Vertical or horizontal position possible
- Can be used regardless of direction of rotation
- Self-priming pump up to 0.2 bar absolute
- Available as mobile or stationary pump
- CIP and SIP cleaning standard
- Closed pump system and therefore suited for safety-critical media
Picture: For brilliant colors, optimal gloss, and perfect structure on all surfaces, FreiLacke offers a branded component system in which all important paint technologies (powder, liquid, electrodisposition, and Durelastic) come together harmoniously and are used in perfect coordination with one another. (Image: Knoll Maschinenbau / FreiLacke)
Source: KNOLL Maschinenbau GmbH