Meeting the Challenges of Pumping Latex
There are certain liquids, which, due to their composition, their characteristics, or how they react to process conditions (and in some situations, a combination of all three) will present challenges to achieving efficient, trouble-free pumping. Emulsions are an example of a ‘difficult’ liquid and users should be aware of the potential problems that can occur if the ‘wrong’ type of pump is specified.
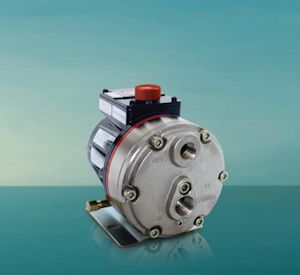
Michael Smith Engineers
The basic definition of emulsions, ‘a mixture of two or more liquids that are normally unblendable’ hints at the difficulties that exist in producing and handling them. There are many types of emulsions which exist naturally or have been successfully developed, ranging from milk to cutting fluids and also latex. Described as a complex but stable emulsion consisting of micro-particles contained in an aqueous medium, latex presents two basic challenges to the pumping process. Firstly, latex emulsions are extremely shear-sensitive and require pumps that can reliably deliver a low shear rate. Secondly, any contact with air will further polymerise the latex, so it’s imperative that the pump is a sealless design.
A recent example of the importance of understanding the challenges of pumping latex and specifying the most suitable type of pump for them is at Bituchem Building Products. Part of the Bituchem Group of companies based in Gloucestershire, their building division manufactures a range of products which help to protect and increase the longevity of highway surfaces. To enhance both the quality and consistency of their products they have a process whereby they pump latex into their bitumen lines with the latex metered in proportion to the bitumen flow. Therefore, it was important for Bituchem to understand the potential pitfalls and to specify the most suitable type of pump from the beginning.
Bituchem approached Michael Smith Engineers with the details of their application and design of their process. The requirement was to pump between 2 – 20 litre/minute of a latex solution with a viscosity of around 600 cP at 10 bar discharge pressure. The capacity was to be adjusted using an inverter and the pump speed altered in proportion to the flow through the bitumen pipeline.
Following discussions they specified and purchased a Wanner Hydra-Cell, sealless, positive displacement high-pressure diaphragm pump, Model G25. The pump, which featured a stainless steel wet end and operates between 70 and 650 rpm, was installed around a year ago and has worked well on the latex pumping application ever since.
Commenting on how the Hydra-Cell pump has operated on their application, John Shirley, engineering manager at Bituchem said, “We were aware of the problems involved when pumping latex and thanks to Michael Smith Engineer’s understanding of our requirements and recommending the most suitable type and model of pump, it is working perfectly”. He continued, “We have not had any issues from day one, the pump saves us time as we now add the latex as part of the overall process. We also appreciate how the pump operates with the combination of low speeds and medium to high pressures”. The ability of Michael Smith Engineers to quickly understand the important requirements of this pumping application, combined with the specification of the most suitable pump, has proved very beneficial to Bituchem Building Products saving them time and ultimately enhancing product quality and improving consistency.
Positive displacement diaphragm pump technology does not have the disadvantages of other designs of pump when handling emulsions, such as latex. The sealless leak-free configuration ensures total product containment while the design of the wetted path reduces internal friction enabling the pump to deliver the level of shear-sensitive operation that is so important when working with latex. The pump’s positive displacement operating principle also guarantees that the product flow rate will remain volumetrically consistent.
The Hydra-Cell range covers flow rates up to 140 lit/min at maximum discharge pressures between 70 and 170 Bar, depending on the model. The absence of seals, cups or packing eliminates the issues associated with seal failure and therefore lowers maintenance costs. They can also be run dry without damage.
They are available in a wide choice of liquid end materials ensuring versatility in their ability to handle most ‘challenging fluids’ along with the flexibility to be adapted to a wide range of pumping duties. They have a proven track-record of robust and reliable operation in applications such as metering, dosing, injecting and spraying chemicals, solvents, acids, hydrocarbons, natural gas liquids, alkalis, polymers, aqueous ammonia, resins, slurries, recycled or dirty liquids.
Source: Michael Smith Engineers