Lutz Centrifugal Pumps: Two Pump Series, One Concept
The demands placed on vertical immersed plastic pumps in treatment plants for chemical waste fluids are extreme in some cases. The situation becomes particularly critical if the media to be pumped are close to boiling point and the NPSH value of the system is very low - which means that the pumps are operating very close to the cavitation point.
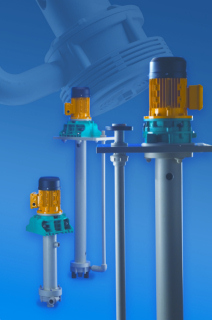
Lutz B80 HME and KME Centrifugal Pumps
In order to meet these requirements even more effectively in future, Lutz Pumps has developed a new range of plastic pumps - the B80 series. These pumps are based on the modular concept of the AM and TMR series magnetic centrifugal pumps, which have been used very successfully for many years. The hydraulic system used in the horizontal and vertical pumps is identical, which also has a beneficial effect on pricing, spare part management and system planning.
The HME model series is a vertical, single-stage cantilever pump developed to pump gaseous and steam-laden fluids with which low suction head heights exclude the use of horizontally installed pumps for technical reasons. Primary fields of application include gas scrubbers, flue gas cleaning systems, water treatment plants, surface treatment plants and heat exchangers.
At the heart of the new pump is the structurally complex but at the same time simple connection between the motor and the pump. The motor flange on the one hand and the shaft guide tube for the pump on the other are supported and centred radially and axially by means of generously dimensioned bearing shells. All the tolerances required to ensure safe operation of the pump are clearly defined by the bearing shells.
Corresponding adapter flanges are available for the various applicable motor sizes. The bearing shells that connect the pump and motor are securely fixed by two bolts. The bearing shells are moulded so that they also act as a base plate to facilitate the unit s installation in the system. This eliminates the need to align the pump.
The generously sized pump shaft is bolted to the motor shaft by means of a rigid coupling. By using this configuration, it was possible to minimise the radial and axial forces that otherwise act on the motor bearing, thus reducing the primary cause of failure of vertical pumps. To protect against chemical attack, the pump shaft is integrated in a shaft guide tube sealed using static seal rings and does not therefore come into contact with the pumped medium. The pump shaft is overhung. As a result, it was possible to dispense with an additional main bearing.
A gas seal that can be safely run dry is integrated in the upper area of the shaft guide tube and protects the coupling and motor from aggressive vapours. The gas seal is fixed by the bearing shells so that radial or axial deflections cannot occur. This configuration guarantees excellent operational safety.
The HME model series is designed for vertical dry-well installation and is available with installation dimensions of 275 and 450 mm. The power spectrum extends to a flow rate of 50 m³/h and a pumping head of 40 m. The pumps are designed for fluids up to a density of 1.8 kg/dm³ and temperatures up to 90°C. A choice of versions made from glass-fibre or carbon-fibre reinforced PP and PVDF is available. IEC motors of the type B5/V1 are fitted as standard.
The suction and discharge connections can be specified either as BSP/NPT or ISO/ANSI flange.
The KME model series is a vertical, submersible centrifugal pump based on the identical design principle and offering the same advantages as the model series described above. The pumps are designed for immersion depths of up to 1500 mm and are supported along the entire motor bearing in large main bearings, available either as PTFE/AI203 or SiC/SiC.
The bearing shells are used to secure the pump to the base plate, into which the delivery line is integrated. Connections are provided either by BSP/NPT thread or ISO/ANSI flanges.
The pump s simple layout combined with the sophisticated bearing shell design ensures that it can easily be integrated into plants and systems. With minimum assembly work, the operational reliability of the motor bearing and the main bearings for the pump significantly increased, which has a positive impact on system availability.
Source: Lutz Pumpen GmbH